Obtaining the properties for steel is relatively easy since most of the high-formability steels are a single alloy (low carbon) and one temper (O or recrystallized). In contrast, aluminum has a large number of possible alloys and an extremely complex system of tempers. To illustrate property comparisons, the table below shows two automotive alloys with good formability: aluminum-killed draw-quality (AKDQ) steel and a copper-magnesium heat-treated aluminum alloy (2036-T4). The table provides the data necessary to assess the relative formability of the two samples.
1) The elastic modulus for aluminum is one-third that of steel. Therefore, aluminum springback will be three times that of steel.
2) The YS is the basis for this comparison and therefore they are equal. However, many regions of the world use UTS for comparison purposes.
3) The UTS of the aluminum is higher than the UTS of steel. This may be a result of heattreating the aluminum to a T4 temper. The UTS is a parameter only found in the tensile test and rarely is a parameter in sheetmetal forming.
4) The work-hardening exponent (n-value) is the key measure of the stretchability of sheetmetal. A high n-value: a) reduces any localized strain distribution (strain gradient) that attempts to form and b) increases the maximum allowable stretch defined by the forming limit curve. Over the measurement range of 10 to 20 percent stretch in the tensile test, the n-value for AKDQ steel is constant.
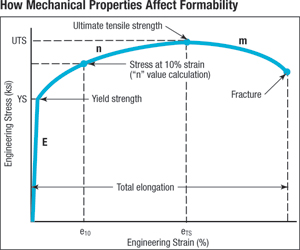 |
The n-value for 2036-T4 aluminum, however, is nonconstant and the value decreases with strain. The 0.28 value is the initial n-value, while the (0.20) value is the average value over the entire measurement range. Since the average value is well below the initial value, the n-value operative during the latter portion of the measurement range must be well below the 0.20 value. As a result, the aluminum begins with better stretchability than the steel but soon becomes equal and then less than the AKDQ steel. Thus, portions of the aluminum stamping with low strain values have the advantage of the increased stretchability. Unfortunately, the high strain areas of the stamping that need higher n-values must survive with the lower n-values.
5) The positive strain-rate hardening coefficient (m-value) of the steel also acts like the n value to reduce any localized strain gradients and assists in improving stretchability. A positive m-value means that the onset of the strain gradient gains strength over its neighbor elements and retards its growth. A negative m-value means that the onset of the gradient loses strength and accelerates the gradient growth. Therefore, the negative m-value of the aluminum sample increases the formation of localized strain gradients and thereby tends to negate some of the advantages of the n-value. The aluminum part will have more severe localized strain gradients and the accompanying localized thinning. These severe gradients mean that springback variation of the aluminum sample will be more difficult to control.
6) The bendability of sheetmetal is proportional to the total elongation. Therefore, the AKDQ steel is capable of a smaller R/t (punch radius to sheet thickness) ratio than the 2036-T4 aluminum.
7) The normal anisotropy ratio (rm) for the steel sample is more than twice that of the aluminum sample. This means a slightly larger limiting draw ratio (LDR) is available to draw a deeper cylindrical cup from a circular steel blank.
8) The higher set point (FLC0) for the forming limit curve means that the whole forming limit curve is higher for the AKDQ steel sample than for the 2036-T4 aluminum sample. Therefore, the steel has higher limiting strains than the aluminum.
This type of material comparison using textbook values at least provides an early warning of forming problems ahead. Having the mechanical properties of the actual coils of sheetmetal determined by a test laboratory is an even better method to assess the conversion from one metal to another. MF
Technologies: Materials, Quality Control