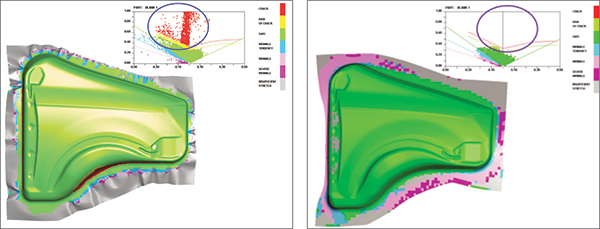
|
Advances in optimization have enabled simulation software to cut weeks off of development time. Within a day, sophisticated solving work can take a simulated part (such as this vehicle fender, left) and optimize it (right) with the ideal draw-bead placement. Photo courtesy of ETA. |
“To achieve profitability, these businesses must produce a good product on a timely basis while achieving cost savings,” Hayden says, “and simulation analysis tools go a long toward enabling companies to make decisions that result in quality, cost-effective products.”
Hayden offers the example of a customer that throughout the recent recovery has improved profitability two to three times due to controlling and understanding fixed assets and direct labor, because it can predict tool performance and perform precise scheduling.
“Productivity and efficiency leads to profitability,” he says, “and this technology allows users to better determine per-piece price so that they have confidence in their costs beforehand.”
Gaining confidence in the analysis and accuracy of simulation tools enables expansion into new markets and projects.
“Companies can bid on more complex parts and grow their comfort zone, perhaps expanding from automotive to appliance or aerospace,” Hayden explains. “Capabilities in simulation systems can help open doors to new processes that enable entry into new types of businesses.
“Tool-and-die is constantly evolving,” continues Hayden, “so players in this arena must be conscious of the new high-strength steels and other new alloys, and need a tool such as simulation to deal with what’s new. Standing pat will put you behind the eight ball.”
Springback in the new materials Hayden references offers an area where simulation pays big dividends, allowing users to predict how materials will react to force. This leads to improved tool performance and higher-quality parts from the start.
Not only does new simulation technology enable new-market and new-process entry, it continues to quicken development time upfront. Optimization is a case in point. “Proper draw-bead placement for medium or large stampings had not long ago been a week-long testing project,” says Hayden. “Now, it can be done in one day.”
Complementing Designer Expertise
Placed in the hands of an experienced designer, die-design software reaches its pinnacle and provides an excellent cost- and time-saving tool.
For example, “two designers can proceed with part nesting in two different s,” explains David Lindemann, application engineer for Cimatron Technologies Inc., Novi, MI. “One approach is to eliminate as much scrap as possible and form as tightly as you can. The other considers the tool, noting that parts placed tightly together results in fragile tooling. Some software may provide every possible nesting configuration along with scrap-percentage factors, and the designer can choose with the goal of achieving the optimal scrap-percentage factor while retaining good tooling conditions.
“But an experienced designer who understands what process is necessary for making the proper, most-stable tooling in the shortest amount of time can enter a minimum set of conditions based on knowledge and experience,” Lindemann continues. “He knows, for example, that the hunk of tool steel should not be less than 1 in. thick given the grade of material to be stamped, so he enters that as a minimum condition. He sees that a certain angle is needed in a certain location, so he sets a condition there. Throughout all of this, the experienced designer can see the scrap-percentage factor change on the screen as the software automatically calculates it.”
At this intersection of expertise between designer and software, conditions are optimized, yielding an ideal balance of scrap generation and tool robustness.
“Designers can use their experience, and through that the software helps them arrive at the best solution,” Lindemann says.
Die-design software also assists experienced tool designers and adds efficiency by thinking like designers think.
“They know that they must punch holes in the steel before forming,” Lindemann adds. “They know that when pulling a punch it must go through a particular piece of steel with so much clearance and then go through another piece of steel with even more clearance, and then go into another piece of steel and hold it. The software stores that in job memory, making it repeatable and ensuring a proper design while saving time in trying to recreate everything.”
Through such interactions, the experienced designer adds to the knowledge base in the software system, and through the system makes that knowledge available to those who are less experienced—junior designers, for example, or those in the quote department.
“Good designers know what different features and operations will cost,” concludes Lindemann, “and can build up the knowledge database inside of the quote system, for example. Less experienced personnel draw from that, leading to more accurate quotes.”
Consider the Big Picture
With simulation software gaining acceptance throughout the industry, lead-time-reduction arguments are losing some luster. Going forward, users of simulation software can differentiate themselves if they leverage its capabilities to see the bigger picture. So stresses Eric Kam, product manager at AutoForm Engineering USA, Troy, MI.
“We challenge people in that, because since computers are so fast and simulation tools have automated things to a high degree, don’t we owe it to ourselves to simulate the road not taken?” Kam asks. “Look, for example, at cam trimming versus direct trimming and then flanging down in a later operation. A designer may choose to eliminate the cam and go with the second option, saving money on the initial tooling investment. But how much are you really saving? If eliminating the cam can be shown to save $20,000, is doing so justified? Try simulating with and without a cam, and predicting the cost of both processes. Robust simulation may show that employing the cam-trim operation results in better overall production repeatability, with a 0.1-percent scrap-rate prediction as compared with a 0.5-percent rate by eliminating the cam. The reduction in downtime due to increased repeatability could save tens or hundreds of thousands of dollars over the life of the job. You saved $20,000 upfront but spent perhaps $100,000 more overall. What was the correct decision?
“The future goes beyond feasibility simulation,” Kam continues, “and uses simulation results as a factor when considering the overall comprehensive cost for forming the product in a process.”
Eliminating process concepts without sufficient justification can be a danger when only using simulation for feasibility, Kam cautions.
“Take, for example, a three-die process that draws, trims and flanges,” he says. “Simulation might say, ‘yes, that works.’ Then, upon springback analysis and other testing, designers decide that they must modify the part to fit into the process window, and allow for a certain amount of part variation due to striking only three times. By simulating an alternative, made possible due to advancements in simulation technology, designers may find that part quality improves enormously without modifications in a four-hit process using a cam. Not modifying the product design could save tens of thousands of dollars over what the simplified process saves upfront.
“So now,” Kam continues, “some designers use simulation to validate a suggestion for customers to change the product. They might say to the customer, ‘You need a product concession for the part to be makeable, and I have simulation to prove it.’ But changing the product can cost hundreds of thousands of dollars in assembly costs if, for example, a carryover mating component won’t fit the new part and that component must be redesigned, too.”
The Conclusion?
“People must think in a larger, more holistic ,” Kam says. “That is the next rung on the ladder for finding cost savings through simulation. Quantify the potential costs of the tools, blank material and production. Then factor in the potential repeatability of not only the ‘leading process,’ but also those that we traditionally eliminate due to subjective opinions about costs. Finally, make a balanced decision about the quality, cost and repeatability of the processes we choose and those we eliminate. Many in the industry are just not there yet.” MF