For slower-running applications, such as those often associated with AHSS, capacitors have more time to accept a charge, enabling full charging, and providing more energy, more efficiently, throughout the stroke for forming.
Quicker Advance and Return Aids Strokes/Min.
Even if more forming energy becomes available with a servo-driven press, strokes/min. and, in turn, productivity suffer due to the need for slower forming speeds when working with AHSS, right? Not so, Patil explains, thanks to the adjustable velocity along the stroke length, an important advantage inherent in servo-driven presses.
Suppose that part production includes a relatively deep draw of dual-phase (DP) 1400-MPa steel. Obviously, forming this material requires more energy than when working with DP 600-MPa steel, and may, for example, entail the need for six draw stations instead of three. And again, forming speed must be slowed. Whereas parts from the lower-strength material may be produced at 30 strokes/ min., working with the stronger material may require speeds not surpassing 15 strokes/min.
Stampers employing a servo-driven press can run at 15 strokes/min. during forming, but during all nonforming portions of the stroke, the press runs at top speed, thus achieving an overall speed of 30 strokes/min. and keeping production on track.
Effective in Battling Springback
Springback represents a huge challenge when stamping AHSS. At the EWI conference, Patil provides the example of a wing-channel project, where DP 350-MPa steel exhibits significant springback. Due to workhardening, separate restrike stations won’t work. A shop-floor servo-press solution involved restrikes in the same cycle at bottom dead center, again, owing to the ability of servo-driven presses to control motion during the stroke. Within that single cycle, the tool restrikes two more times at bottom dead center for about 0.2 sec. each time, and uses heat as an ally to provide improved part definition and set the wings at required 90-deg. positions.
Reverse-Tonnage Reversal
Patil sees more and more cases of reverse tonnage, or snapthrough, in his travels, especially on older presses built before the dawn of AHSS. Reverse tonnage results from the release of pressing force when the part material fractures. This energy and vibration transfers through the tooling and press, and may result in significant damage. Presses not built to deal with the stresses and strains of forming AHSS are candidates for succumbing to reverse tonnage. Patil asks how a metal former without tonnage-monitoring capability knows if a press is experiencing reverse tonnage.
“When you see pieces falling off of your press, that’s a sign of reverse tonnage,” he bluntly assesses.
Shock dampeners provide some protection on traditional mechanical presses, says Patil, who offers the variable-stroke-speeds benefit of servo presses as a reverse-tonnage answer. Using a pressroom example, Patil describes a blanking die placed in a standard crank-motion mechanical press. Measurement reveals 114 tons of forward press force and reverse tonnage of 9 tons. The same die then is placed in a servomechanical press, with the ram descending rapidly prior to slow blanking. Not only does the bottom-stroke speed reduction lower the noise level significantly, from 101 to 75 dB, but forward force reduces to 104 tons, with reverse tonnage dropping to 2.6 tons, well within the recommended reverse-tonnage limit of 20 percent. Aida-America, Patil reports, will present this demonstration of a 70-percent-plus reverse-tonnage reduction at FABTECH in Booth D46027. MF
View Glossary of Metalforming Terms
See also: Aida-America Corp.
Technologies: Materials, Stamping Presses, Tooling
Comments
Must be logged in to post a comment. Sign in or Create an Account
There are no comments posted.Stamping Prog.-Die Parts on 300-Ton Straightside Servo Press
Thursday, June 12, 2025
Avoiding the 7 Deadly Sins of Stamping: Part 6; Using the 10...
Art Hedrick Friday, April 25, 2025

Seyi Partners with Field Service Mechanical Co.
Friday, April 11, 2025
Mexico Stamping Technology Webinar Series 2025: Day 4
Thursday, April 10, 2025
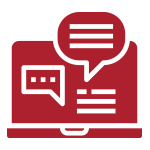