When It Comes to Safety Efforts, More is Best
November 1, 2017Comments
c But there is an alternative for employers willing to work with the enforcing agencies. It’s the extra-steps alternative, effective when the Occupational Safety and Health Administration agency, employer, employees and their representatives come together to focus on best safety pratices, corporate-wide or industry-wide worksite safety improvements, and safety-program incentives to settle citation issue.
Some examples highlight the success of extra-steps alternatives. The first involved two willful classified citations following a fatality, removed when the employer developed a mitigation plan to reduce or eliminate a potential workplace hazard. Included in the plan, a best-practices regiment that included defined work-area responsibilities, assigned work roles, commitment to educating the industry and setting up an industry task force for identifying and assessing specific, latent worksite-property conditions.
Another example saw an employer develop a best-practices safety manual, and make copies available for the enforcing agency to use in the field. In return, the employer gained a major penalty reduction and reversal of two willful classifications. The enforcing agency provided the safety manuals to their inspected companies to help them better understand how to comply with general safety standards.
In another case, a wall-to-wall set of lockout-tagout (LO-TO) citations were resolved when alternative safety die-changing power-press procedures were accepted as equivalent to LO-TO protection in another citation settlement agreement.
Finally, one agency, in return for a major mega-penalty reduction, recognized and spelled out these extra steps:
- Hired an experienced safety professional whose job duties included reevaluating all training programs, reviewing and updating the employee handbook, and reviewing and enhancing all LO-TO policies and procedures. The agency agreed to retain the safety professional for a minimum of three years.
- Revised its performance evaluations and compensation structure for addressing and evaluating adherence to safety rules and regulations on an annual basis.
- Developed and implemented bi-weekly leadership-team meetings with the owners, vice president and leadership team. The meetings address safety expectations, safety training, safety processes and procedures, and auditing of those programs.
- Conducted and documented regular auditing of the facility to abate hazards identified in inspections, and to review and identify additional potential hazards.
- Hired outside professional agencies to conduct additional safety training. MF
Technologies: Safety
Comments
Must be logged in to post a comment. Sign in or Create an Account
There are no comments posted.Toolroom Safety
Peter Ulintz Monday, September 25, 2023
Mexico Stamping Technology Webinar Series 2023: Day 2
Thursday, March 30, 2023
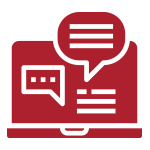
Pilz Digital Maintenance-Safeguarding System an Efficient Al...
Thursday, March 16, 2023