3M Brings Digital Science to PPE Management
November 1, 2015Comments
Environmental, health and safety (EHS) professionals typically find themselves inundated with paperwork to document issuance, maintenance and inspections of personal-protective equipment (PPE). A recent study by 3M finds that most safety and health professionals still manually document their safety programs using pen and paper, word processing or spreadsheets. To help reduce paperwork and time spent on documentation and compliance tasks, 3M has developed Active Safety, a digital PPE-management system.
Says Hugh Murphy, 3M business development manager: “Active Safety is a software tool to help EHS professionals reduce the time spent on paperwork, access data when and where they need it, identify trends and ultimately help employers keep workers safe and healthy.”
Active Safety uses radio-frequency identification (RFID) tags and cloud-based software that runs on mobile and desktop devices. To deploy Active Safety, EHS professionals add each piece of PPE onto the platform. They attach an RFID tag to each piece, and a user scans the tag with a mobile device to record PPE history, usage and location. The EHS professional also can schedule upcoming events, such as worker inspections and PPE fit testing, and can access data from the PPE program on a simple dashboard.
By gathering PPE data from across a facility or multiple sites, Active Safety allows EHS professionals to connect with their employees and focus on improving safety, rather than completing paperwork.
Additional features of Active Safety include worker-specific PPE-record management, inspections and maintenance, PPE audits, inventory management and trackers for employee training, medical evaluations and fit-testing.
www.3M.com/PPESafetyTechnologies: Safety
Comments
Must be logged in to post a comment. Sign in or Create an Account
There are no comments posted.Toolroom Safety
Peter Ulintz Monday, September 25, 2023
Mexico Stamping Technology Webinar Series 2023: Day 2
Thursday, March 30, 2023
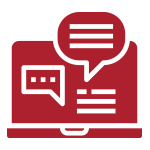
Pilz Digital Maintenance-Safeguarding System an Efficient Al...
Thursday, March 16, 2023