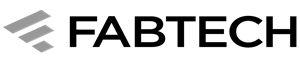
Monitor Forming-Process Parameters and Equipment
October 2, 2019Comments
Schuler Inc.
Booth D46055
Schuler showcases smart forming technology via sophisticated sensors and actuators in its latest machines.
Machine components can be monitored for changes, wear and damage to optimize the maintenance process. For this purpose, regular test runs of the system are performed in which vibration data, torque progressions and energy consumption, among other things, are measured, stored and compared. Sensors in the press bed and slide record the acceleration per stroke for example, enabling stampers to monitor the forming processes in detail.
The most recent example is the completely redesigned MC 125 stamping press. Thanks to additional integrated sensors, its condition can be fully monitored at all times, even from mobile devices.