Immel will be responsible for engaging with
3D-printer OEMs, additive manufacturers, academic institutions and
research organizations. A veteran of the AM industry, Immel frequently
presents at industry conferences, has written about myriad AM topics
including mass customization and MRO, authors the AM: Ideation to
Industrialization blog and has been a contributor to numerous AM-expert
panels.
Paramatters’ CogniCAD 4.0 Generative-Design Software Offers Improved Automated Workflow
Paramatters has released CogniCAD 4.0
generative-design software, an upgrade designed to improve automated
workflow for manufacturers. The software provides a fully automated
workflow based on inhouse-developed topology optimization,
high-resolution finite-element analysis (FEA) and computational
geometry, and that requires no manual adjustment or reconstruction,
according to company officials.
Designs generated by CogniCad, satisfying all
input design requirements, reportedly are ready for manufacturing within
a few hours at the longest. The software considers a variety of loading
conditions as well as design goals and restraints related to stress,
stiffness, deformation and vibration. STL and STEP outputs then are
validated by built-in proprietary FEA. It requires no manual re-modeling
or geometry reconstruction.
Automatically generating optimized, lightweighted
structures, CogniCAD 4.0 supports processes including AM, multi-axis
CNC milling, and die and investment casting. Version 4.0 reportedly
offers increased control over geometry, with an advanced
support-structure generator better enabling users to prepare files for
AM.
“Manufacturers now have access to a one-of-a-kind technology that enables them to create lightweighted and structurally validated parts to meet their design and manufacturing needs,” says Dr. Michael Bogomolny, Paramatters cofounder and chief technology officer. “Designers and engineers can automatically generate high-performance designs that consider various manufacturing technologies and make decisions based on a cost, performance and time-to-market basis.”
CogniCAD 4.0 is available as an annual
subscription cloud-based service or as an annual local installation
lease using a Windows-based installation. The company is offering
several subscription and enterprise-based models, and engages in several
complementary strategic partnerships.
Cloud-Based Platform Interconnects Markforged Printers Worldwide to Learn, Improve Printing
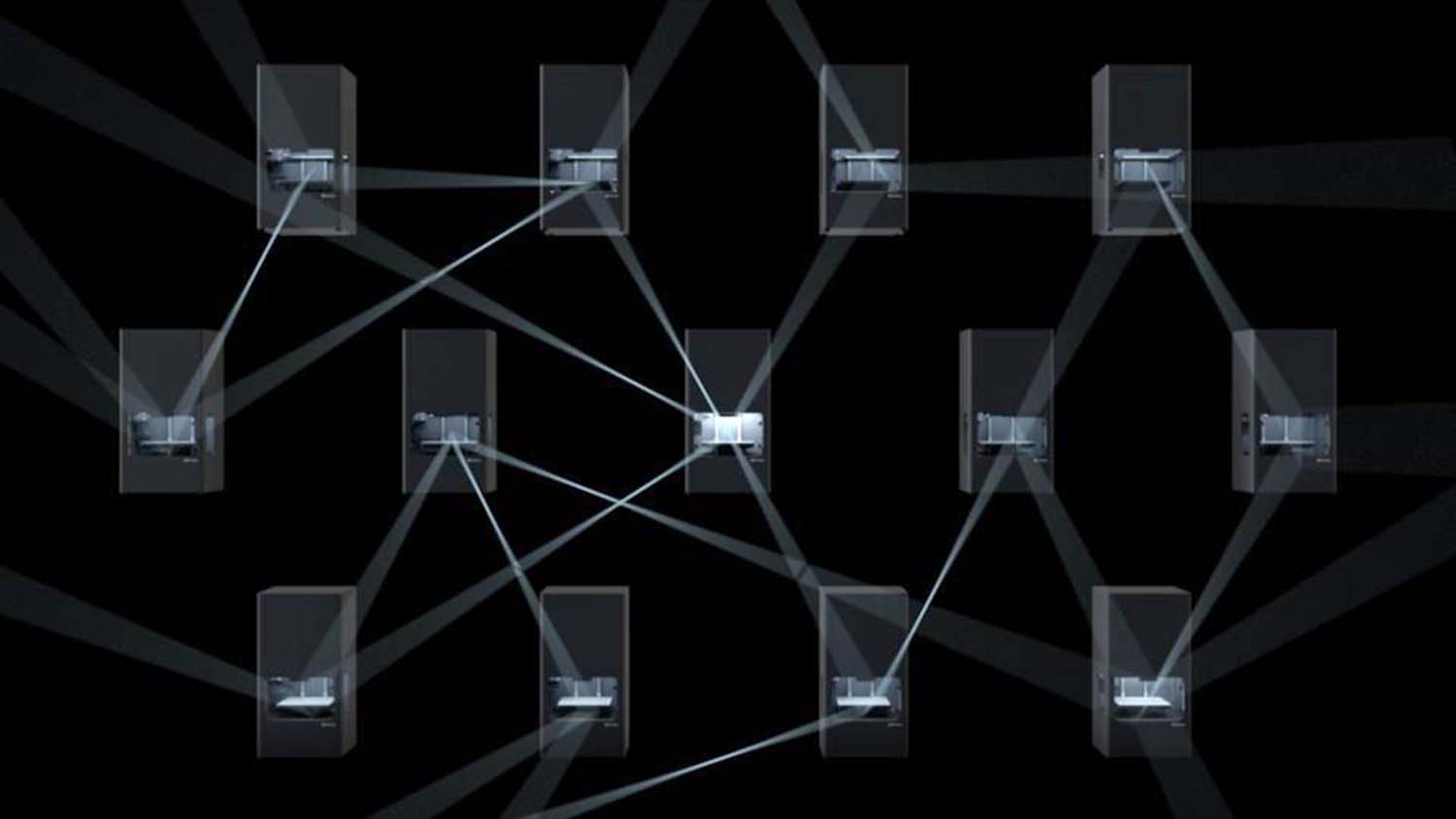
|
The new Markforged cloud-based industrial 3D-printing software platform, Digital Forge, reportedly can connect more than 12,000 Markforged systems in use worldwide. The platform’s machine-learning feature enables the company’s Eiger print-preparation software to constantly learn from the interconnected systems, in theory making every print on a connected Markforged system more accurate than the last. |
Markforged
has launched a cloud-based industrial 3D-printing software platform,
the Digital Forge, designed to interconnect all Markforged systems,
employing machine learning (ML) to improve printing on all connected
machines, according to company officials.
The platform, which can connect more than 12,000 Markforged systems in use worldwide, claims to be the first of its kind to use ML. This feature reportedly enables the company’s Eiger print-preparation software to constantly learn from the interconnected systems, in theory making every print on a connected Markforged system more accurate than the last.
The Digital Forge uses what the company calls fleet-federated learning, an interconnected form of ML that relies on data from other nodes, or other printers, in an expansive network. By sharing and receiving printer data on an ongoing basis, the platform itself gets ‘smarter’ day-by-day, enabling users to leverage the latest advancements over the cloud. The idea is that the Digital Forge and its printers should become better equipped at correcting print jobs mid-print, reducing the number of global print failures on Markforged systems over time, all while increasing part quality.
Because the platform is cloud resource-based, it
takes the load off of local systems, according to Markforged officials,
who note that this allows use of the Digital Forge to print metal and
carbon fiber-reinforced parts from just a single browser tab.
“Through the Digital Forge, manufacturers can use our software to fabricate strong, accurate and durable metal and composite parts for orders of magnitude cheaper than they’ve traditionally been made—on-demand and directly at the point of need,” says Greg Mark, chairman of Markforged.
New Portal Gives Manufacturers Online Digital Presence for Order Development and Processing
3Diligent has launched its 3Diligent Portal,
which allows manufacturers to build an online digital presence, reach
new customers, receive RFQs and, ultimately, process orders remotely and
securely, no matter their levels of Internet savvy.
The Industry 4.0 software company and on-demand manufacturing provider now makes available a page on portal.3diligent.com where manufacturers can create a free account for 3Diligent’s Shopsight shop-management software. Upon creating a Shopsight profile, manufacturers receive a free 3Diligent Portal page, where they can share information about their business, receive RFQs and process them using the Shopsight software.
“With the launch of 3Diligent Portal, we are empowering manufacturers with the tools they need to be successful during a pandemic environment,” says Cullen Hilkene, founder and CEO of 3Diligent. “It is an increasingly digital world, and it is vital that manufacturers digitize their operations in order to succeed. 3Diligent Portal will enable manufacturers to augment their online presences while providing customers the information they need to identify the best manufacturer for their job.”
The application will enable manufacturers around
the world to build out a robust online presence, which has become
increasingly important as the pandemic continues to significantly impact
the manufacturing industry, Hilkene explains. Manufacturers and their
customers have faced shutdowns and significant disruptions in their
supply chains, and it is paramount that manufacturers can identify,
engage with and secure new business. With 3Diligent Portal, Hilkene
offers, customers can accurately identify solutions and fulfill
manufacturing requests.
In addition to helping manufacturers build an online presence, the 3Diligent Portal page syncs with 3Diligent’s ProdEx manufacturing-as-a-service application and Shopsight software, allowing customers seeking parts and manufacturers receiving part requests to do so seamlessly and securely. Suppliers with paid Shopsight subscriptions also can issue instant quotes to customers using Portal.
3Diligent Portal is part of 3Diligent’s Vulcury Industry 4.0 software platform. Vulcury also includes ProdEx, Shopsight and 3Depot, 3Diligent’s database of digital-manufacturing technologies and materials.
ML Software Aiding Air Force in Determining Airworthiness of Laser-AM Parts
Senvol’s data-driven ML software for AM, Senvol ML, currently is being used to assist with a U.S. Air Force program focused on developing methodology for demonstrating airworthiness of multi-laser AM. The program, a collaboration between the Air Force Research Laboratory and Air Force Life Cycle Management Center with the University of Dayton Research Institute (UDRI) as the prime contractor, utilizes an EOS M400-4 quad-laser powder-bed fusion machine.
The FlexSpecs program focuses on qualifying the EOS M400-4, developing baseline mechanical properties and design allowables, and ultimately making demonstration builds of heat exchangers and hypersonics-relevant parts—an area of need identified by the Air Force.
“AM recently has demonstrated the ability to rapidly deliver complex geometries and production-quality parts that enhance the capabilities of Department of Defense (DoD) weapons systems,” explains Jessica Orr, program manager and materials engineering team leader for AM and repair technologies at UDRI. “A major challenge facing the use of AM for producing DoD-relevant end-use parts: The number of available large-scale printers likely will be limited for the next five to 10 years. In this collaborative program we are developing and demonstrating methodology to use a new multi-laser AM printer to produce airworthy, end-use parts.”
The Senvol ML software assists with the
development of the process optimization and characterization plan, and
helps to analyze all project data.
“Our machine-learning software, Senvol ML, is well-suited to assist with AM qualification, and this is a great example of that,” says Annie Wang, Senvol president. “In addition to helping to develop baseline mechanical properties and design allowables, the software will analyze data to evaluate laser-to-laser consistency, optimize bulk scan settings, identify preferred overlap patterns and parameters, and confirm uniformity over the entire build plate.”
Mobayen Appointed AlphaStar CEO
Amir Mobayen has been appointed CEO of AlphaStar,
an Irvine, CA, engineering-software company that provides physics-based
simulation technologies.
A key member of AlphaStar’s board of advisors since 2012, Mobayen brings 20-plus years of industry-related new-business-growth experience; an international perspective with a multicultural/multilingual background; and proven success in market-driven customer focus, product innovation and development of best-in-class talent, according to company officials.
“It is extremely exciting and an honor to be named AlphaStar’s CEO” says Mobayen. “We are uniquely positioned in the center of the simulation and additive manufacturing technology value matrix. As we enter our next growth phase in 2021, our strategy will build on AlphaStar’s prior customer successes in the aerospace, automotive, defense and energy industries by augmenting our talented people, outpacing the industry with continued product innovations, and leveraging our strong relationships to deliver profitable growth.”
Materialise Introduces Build Processor for Desktop Metal Binder-Jetting Systems
Materialise, Leuven, Belgium, introduced a
Desktop Metal build processor to support Desktop Metal binder-jetting
technologies, including its Shop System and Production System platforms.
This strategic partnership will help reduce complexity for companies
looking to scale their 3D-printing operations, by providing a more
seamless, end-to-end workflow.
Materialise build processors find use in industrial printing, translating 3D designs into machine-specific build files for a variety of machines. As part of the announcement, Materialise also has introduced sintering support generation for metal binder jetting, as part of Magics’ SG+ module, and metal binder jetting enhanced 3D nesting. This integrated solution, compatible with the Materialise software suite, will help to create a better-connected workflow and improve productivity.
“Our partnership with Desktop Metal supports our next-generation build-processor strategy to remove some of the remaining barriers to adoption of 3D printing as part of a connected, industrial manufacturing process,” says Stefaan Motte, vice president and managing director of Materialise Software. “Removing barriers of speed, scale and cost requires a closer integration between software and machine.”
Desktop Metal will make the build processor
available as an add-on software offering with its advanced metal 3D
printing solutions, the Shop System for mid-volume manufacturing and the
Production System for high-volume production.
New Software Overcomes Shrinkage and Other Sintering Challenges
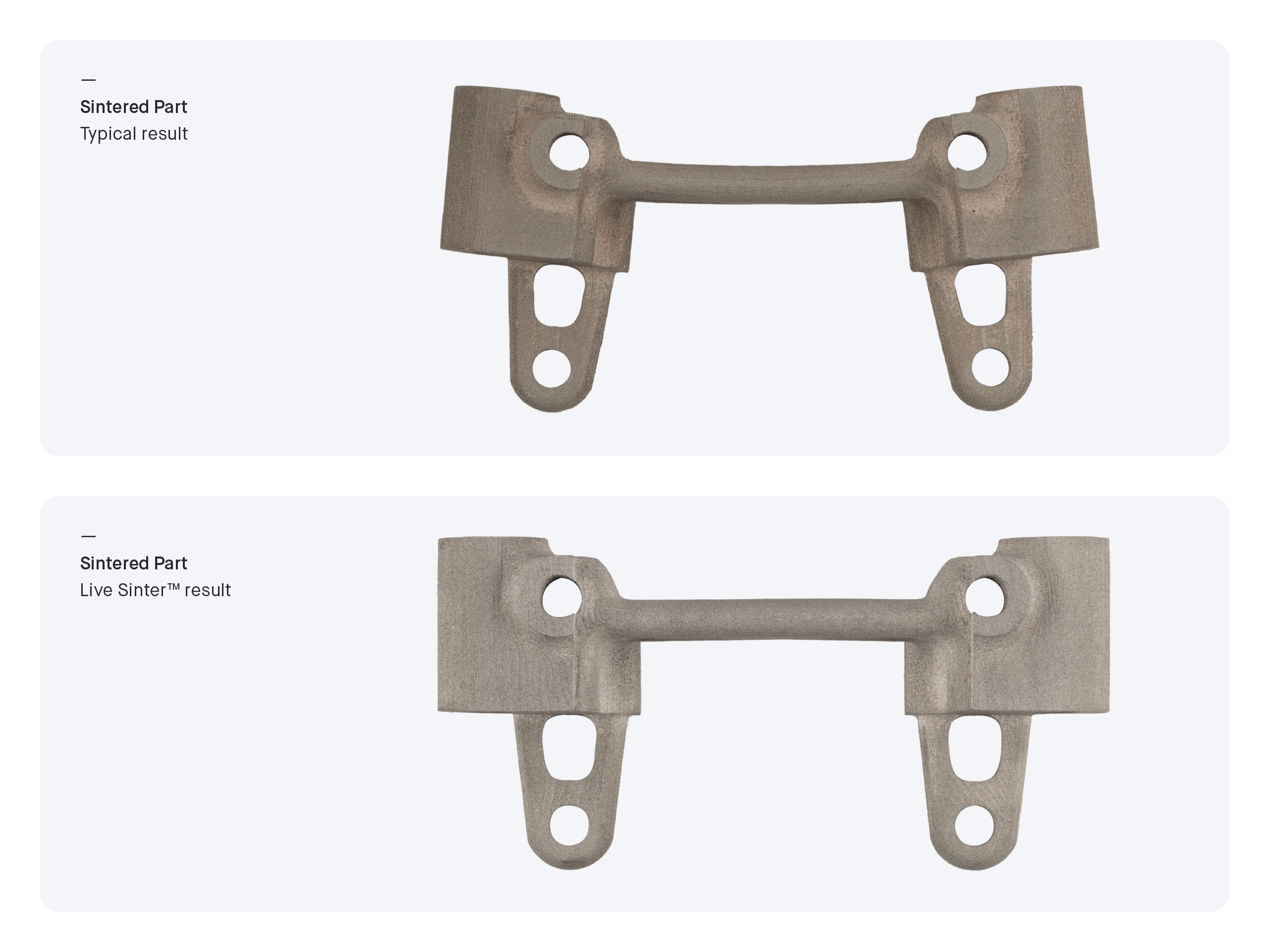
|
See how the use of Live Sinter (bottom), new software from Desktop Metal, corrects for the shrinkage and distortion that parts typically experience during sintering. |
In relation to the previous item, Desktop Metal has
launched Live Sinter, software that corrects for the shrinkage and
distortion parts typically experience during sintering, and which also
enables printing of geometries that, without the software, would prove
difficult.
Live Sinter eliminates the trial and error
required to achieve high-accuracy parts via powder metallurgy-based AM
processes such as binder jetting. By improving the shape and dimensional
tolerances of sintered parts, first-time part success for complex
geometries is improved and the cost and time associated with
post-processing are minimized, according to company officials, who note
that in many cases, the software enables parts to be sintered without
the use of supports.
While compatible with any sintering-based powder metallurgy process, including metal injection molding, Live Sinter will first be available to customers of Desktop Metal’s Shop System, shipping now, and Production System, shipping later in 2021.
During the sintering process, improperly
supported parts face significant risk of deformation, resulting in parts
that emerge from the furnace cracked, distorted or requiring costly
post-processing to achieve dimensional accuracy. Until the debut of Live
Sinter, trial and error represented the best approach for dealing with
sintering challenges, note Desktop Metal officials.
Live Sinter, which users can calibrate to a variety of alloys, predicts the shrinkage and distortion that parts undergo during sintering, and automatically compensates for such changes, creating ‘negative-offset’ geometries that, once printed, will sinter to the original, intended design specifications. These negative offsets are the result of a GPU-accelerated iterative process, in which the software proactively pre-deforms part geometries by precise amounts in specific directions, allowing them to achieve their intended shape as they sinter.
“Live Sinter was developed by joining forces with, instead of fighting against, sintering-based challenges,” says Andy Roberts, Desktop Metal vice president of software. “In doing so, the software generates negative-offset part geometries that sinter to the intended shapes and dimensional specifications. It also tackles some of sintering’s biggest challenges, such as the use of setters. For years, creating setters that prop up parts in the furnace relied on the intuition of few engineers with years of hands-on experience. Now, the process is easier, more predictable and more controllable using Live Sinter.”
Live Sinter reportedly can simulate a typical
sintering furnace cycle in as little as 5 min. and generate
negative-offset geometries that compensate for shrinkage and distortion
in as little as 15 min. This compares favorably to more general-purpose
simulation tools that use complex meshes and require complex setups and
hours to complete, according to company officials. And, the software can
be calibrated to new materials, sintering hardware and process
parameters with minimal additional effort.
New AM Build Manager Promises Universal Adaptability and Scalability
HP Inc. has introduced Universal Build Manager, which leverages proprietary HP software and data processing as well as Dyndrite’s Accelerated Geometry Engine to simplify and automate build preparation across AM technologies at high speeds, according to HP officials. The new product reportedly benefits from GPU-accelerated processing and Python-programming-language scriptability inherent to the Dyndrite Corp. engine, and is designed to improve the AM technician’s efficiency, productivity and quality, thus enabling mass-personalization, complex workflow automation, and scalability and extensibility in manually driven and automated workflows.
Speaking to the product’s “Universal” tag and its ability to function across a variety of AM technologies and processes, HP and Aconity3D, Aon3D, Aurora Labs, EOS, Essentium, ExOne, Open Additive, Photocentric, Plural AM, Renishaw and SLM Solutions have committed to exploring ways for the HP Universal Build Manager to support their 3D-print systems. Additionally, the open-architecture platform is designed to support interoperability with complementary solutions from software vendors, including Ansys.
“We are addressing software challenges in the additive industry that have prevented it from becoming mainstream, and are providing capabilities to help customers accelerate the journey to digital manufacturing,” says Ryan Palmer, global head of software, data and automation for the HP Personalization & Industrial Business. “The new HP Universal Build Manager simplifies, automates and delivers a digital-first approach to manufacturing. This solution will enable customers to explore new areas of complexity and value, push the boundaries of sustainable production, and automate critical steps in their digital workflows.”
The Universal Build Manager includes universal
support for a variety of AM processes; support for industry-standard CAD
and vendor-neutral formats; a GPU-accelerated geometry engine that
reportedly accelerates computational tasks such as support generation,
slicing and tool pathing; and scalable architecture designed to support
high-part density builds to optimize throughput and minimize cost.
And, its plug-in framework aids in accessibility
to every user, machine manufacturer and software vendor, according to HP
officials, who note that this facilitates the creation of
process-specific solutions without having to share potentially sensitive
IP.
HP officials report that Cobra Aero and Cobra
Moto, a family of companies specializing in the design and manufacturing
of propulsion systems for racing, aerospace and other vehicles, are
deploying HP Universal Build Manager to simplify and automate workflows
across HP Jet Fusion and Renishaw AM systems.
Link3D Tapped for Digital Upgrade of 3D Systems’ On-Demand Manufacturing
Link3D has been selected by 3D Systems to digitally transform 3D Systems’ On Demand manufacturing operations, with a focus on 3D-printing workflow compliance and post-production management.
The partnership enables 3D Systems to establish a
single source of truth for its AM value stream, thus eliminating manual
and redundant systems, according to officials from both companies. 3D
Systems officials see this capability as driving improved customer
satisfaction by increasing production efficiency and transparency from
request-to-delivery.
Along with core software offerings, Link3D
provided 3D Systems with newly released features including its
Post-Production Management app, which allows 3D Systems to optimize
end-to-end processes with the Production Dashboard that automatically
keeps track of queued, completed and failed jobs. Now, 3D Systems can
eliminate paper trails and mobilize the work for operators, reducing
hours spent navigating hundreds of orders per day.
And, Link3D’s ITAR & Export Controlled Deployment solution provides 3D Systems with controlled functionality to ensure regulatory compliance. Key features include government cloud deployment, permissioning and access control, and the ability to support routing to ITAR-approved facilities.
“3D Systems’ On Demand operates multiple AM processes inhouse, and as our offerings grew, we realized that a world-class workflow automation solution was needed,” says Tracy Beard, 3D Systems On Demand director of operations. “Partnering with Link3D helped us take our AM offering to the next level, and the efficiencies gained from implementing Link3D are having an immediate impact on both on-time delivery and quality, with the benefits of real-time analytics. The onboarding process was very smooth and easy.”
Simufact Offering Simulation for Metal Binder Jetting
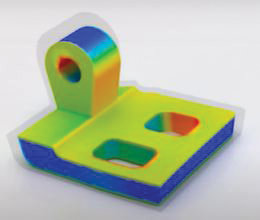
|
A new tool for metal binder jetting extends Simufact Additive software so that manufacturers can predict shrinkage caused by factors such as thermal strain, friction and gravity during sintering without special simulation knowledge. |
Simufact, part of Hexagon’s Manufacturing Intelligence division, has introduced metal binder jetting simulation, enabling manufacturers, at the design stage, to predict and prevent distortion that sintering processes will have on parts.
An emerging AM technology, metal binder jetting
can produce high volumes of parts with minimal spacing, does not require
support structures and enables large lot sizes. Many see it as a
replacement for low-volume, high-cost metal injection molding in medial,
automotive and aerospace applications, among others. But it poses
challenges for early adopters, according to Simufact officials,
including the ability to predict changes during the sintering process: A
part can shrink as much as 35 percent and the simple shrinkage models
used for other processes cannot predict distortion during the post-build
sintering process. Thus, costly physical trials were required to
perfect the printing of each part.
The new tool extends Simufact Additive software so
that manufacturers can predict shrinkage caused by factors such as
thermal strain, friction and gravity during sintering without special
simulation knowledge. By compensating for these changes, parts can be 3D
printed as they are designed, and production teams can significantly
reduce the proportion of parts that must be scrapped or reprocessed,
offer Simufact officials. Sintering-induced mechanical stress is also
predicted before printing to indicate where defects might occur.
Manufacturers can use this information to make changes earlier in their
product development and reduce the need for redesign.
Designed for AM professionals, the tool can
automate the model setup, preparing the CAD or CAE file for
manufacturing simulation, and simulations also can be automated through
Python scripts. To validate the sintering compensation and increase
confidence in quality, the optimized geometry from the tool can be
compared immediately to both the initial design (CAD) geometry and a
metrology scan of a manufactured part within user interface.
Says Dr. Gabriel McBain, senior director of product management for Simufact and sister organization FTI: “We know that customers see metal binder jetting as a pivotal technology for manufacturing, particularly where there’s a need to produce intricate parts at high volumes, such as in the automotive industry.” 3DMP
See also: 3D Systems, Simufact Engineering Gmbh, Senvol, Desktop Metal, Inc., 3Diligent Corporation
Technologies: