One Hydraulic Press Supplants Three Mechanicals
June 1, 2011 Ilsco Corp., Cincinnati, OH, is no stranger to changing with the times and technology.
Ilsco Corp., Cincinnati, OH, is no stranger to changing with the times and technology. Founded in 1894 as a family-owned business, the firm began as the Incandescent Light and Stove Company, selling gas systems. Today it manufactures 15,000 UL-listed electrical components in copper and aluminum, and is one of the largest direct suppliers of mechanical connectors to U.S. and Canadian electrical OEMs. It operates out of six locations throughout North America, including its 250,000-sq.-ft. plant in Cincinnati, with 220 employees.
The Move from Mechanical to Hydraulic
For many years, Ilsco relied on mechanical presses to form its products, at one time operating as many as 50 mechanical presses from 5 to 150 tons. Now, thanks to more efficient equipment and press automation, its press count is down to just 15.
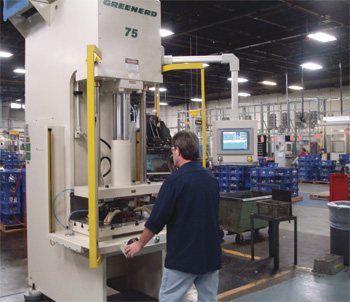 |
Ilsco’s 75-ton hydraulic press features an integral knockout cylinder mounted in the main ram for punching, trimming and marking electrical connectors in aluminum up to ½ in. thick, and for forming copper. |
One key trend, notes manufacturing engineer Keith Tipton, is the switch from manufacture of copper connectors to aluminum. As the availability of aluminum extrusions grew, the company was able to receive shaped extrusions and, depending on the part, machine, stamp and form completed connectors on one press.
However, says Tipton, the firm continued to seek to consolidate dies and processes, and reduce the number of presses on its floor.
“We consider full-revolution presses old technology,” he says. “They are laborious to set up and are not on the leading edge of safety. The more we learned about hydraulic, the more interested we became.” Besides solving maintenance and setup difficulties, Ilsco believed that hydraulic-press technology would allow it to consolidate dies and reduce the number of mechanical presses by providing adjustable stroke length and adjustable tonnage.”
Ilsco’s hydraulic press of choice: a 75-ton model (from Greenerd Press & Machine Co., Nashua, NH) with an integral knockout cylinder mounted in the main ram for punching, trimming and marking electrical connectors in aluminum up to ½ in. thick, and for forming in copper. The press includes a heavy, welded frame that optimizes rigidity and minimizes deflection, to ensure dimensional accuracy and repeatability, and provide long tool life. A large daylight and throat depth accommodates large dies, and long stroke lengths are adjustable from 1 to 18 in.
One Press Replaces Three
“With the addition of the Greenerd press,” says Tipton, “we significantly increased productivity in several s. Its adjustable stroke length and tonnage capabilities provide us with tremendous versatility. Due to the large 18-in. stroke capacity, we’ve been able to standardize our dies and replace three mechanical presses–30-, 25- and 60-ton models–with the one hydraulic press.”