Consumable Use Drives Costs
The majority of the technology advances reside inside the PAC torch (managing a 35,000 F plasma arc literally is rocket science). Further, torch consumables are the primary drivers of plasma quality and operating costs.
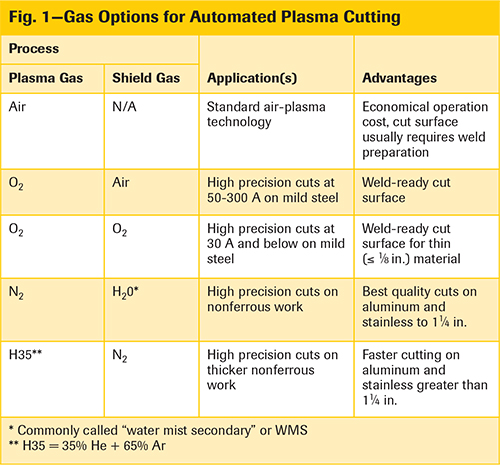
As the plasma tip and electrode wear, cut width gradually increases; arc starts/stops and arc stability become less than ideal. Eventually, cut tolerance or system performance becomes unacceptable and users change consumables.
Standard-definition consumables cost less ($20 for a tip and electrode vs. $45), but high-precision plasma consumables last at least five to 10 times longer. A shop with low table utilization will be less concerned about the cost of consumables and more concerned about the price of the power supply. Conversely, an operation with a high arc-on time will want to maintain productivity at the highest possible level. Such a shop won’t want the rework or other issues related to loose tolerances, while seeking to minimize downtime related to changing consumables, as well as unplanned downtime. Only a high-precision system enables such performance.
As a side note, consider torch designs with quick-change torch cartridges that twist off and on in less than 1 min. Fabricators can minimize downtime by keeping a spare cartridge pre-loaded with fresh consumables.
Because consumable costs play such an important role, plasma-system suppliers can provide a cost-per-cut or cost-per-part calculator that enables the fabricator to compare purchase price, operating costs and return-on-investment for a specific application.
How Much Power?
As a good starting point for balancing cut quality and speed, consider that almost every system manufacturer recommends a cutting output of 10 A per 1 mm of material thickness. Thus, cutting 6-mm-thick material requires setting an output of 60 A, ±10 A; a 100-A, 100-percent-duty system provides more than sufficient capabilities for optimized productivity.
Note that more power is not necessarily better. An excessive current setting creates top-edge rounding. The cut also will have a larger bevel and excess dross, both of which will require post-cut grinding or machining. The added labor cost and increased cycle time negate any speed advantage.
Understanding Cut Quality
|
With the balance of power, speed and quality in mind, users should expect a maximum cutting speed of about 100 in./min. from a high-precision PAC machine. If cut quality is less of an issue or cuts are on long, straight edges, cutting speeds can increase to 150 in./min. or more. Conversely, to maintain cut quality on corners, holes and intricate parts, cutting speed will be slower.
Keep the System in Mind
A good-quality cutting table can hold tighter tolerances than the plasma process itself. However, many believe that purchasing a high-precision plasma power supply lets fabricators skimp on other components. That’s like buying a Corvette and then trying to save a buck with discount tires.
A fully integrated system includes the plasma power source, CNC controller, torch-height control, torch lifter and its associated motors and drives, and an automatic gas-control console. In an automated plasma system, these components work in perfect harmony to control cutting amperage, torch height, speed and gas pressure.
While CNCs for integrated systems and their software add significant cost, they also provide fast payback. For example, a CNC automatically can set and control parameters for “best cut quality” or “fastest cut,” after the operator selects the material type and thickness and cutting-gas combination.
Other CNC benefits:
- Greater productivity and reduced errors. Operators become productive after just hours of training, instead of weeks; one less manually programmed variable is one less item that can go wrong.
- Hole/process optimization technology. After loading a cutting program (or even just a DXF file into a controller from a flash drive), the CNC will examine the file and determine which parameters need to be optimized. Then the controller quickly can recalculate the optimum parameters and cut paths. Without any operator or programmer input, fabricators can obtain bolt-ready holes and better part fit, and eliminate hours of post-cut grinding. Similar technologies exist for optimizing cutting order and pierce methods, as well as locations for complicated nests.
- Automatic nesting tools. For fabricators lacking a separate engineering department, these tools prove invaluable for reducing plate waste and cycle time.
- Bridge tools typically reduce the number of pierces in a cutting program. They automatically assign cut segments between parts to reduce the number of pierces and cycle time. Cost savings as great as 40 percent are possible.
![]() |
Optimized parameters produce weld-ready cuts; notice the angle of the cut lines, which indicates proper travel speed. |
Fabricators determined to minimize their initial expense could forgo a CNC and settle for a manual gas console. However, never skimp on a height controller and torch lifter. As with arc welding, voltage is directly proportional to arc length, or torch height. If torch height varies, cut quality will vary from part to part and even within a single part. At a minimum, use a controller with functions for pierce-height control, pierce delay and pierce retract.
These functions extend consumable life by reducing electrode wear during arc starts and stops, and by minimizing the amount of molten metal that splashes up during arc start.
Approximate Investment
![]() |
Fabricators can use high-precision systems for plasma marking without changing consumables. |
Fabricators seeking a good-quality system should expect to invest $80,000 to $120,000 for a high-precision machine, and $35,000 to $80,000 for a standard setup. Ballpark costs for components:
- 100-A precision power source: $30,000
- Standard-definition power source: $6000
- Height controller, torch lifter, torch, gear boxes/motors/drives, gas console: $20,000 to $30,000
- Integrated CNC (replaces height controller and basic monitor): $10,000 to $20,000
- 5- by 10-ft. table, gantry, motors and drives: $20,000 to $30,000
Depending on specific needs, fabricators may also consider investing in process-optimization software, for another $20,000 or so. However, and the author cannot stress this enough, those considering an automated PAC machine must consider the impact of any component on cut-cost per part and calculate ROI accordingly. MF
View Glossary of Metalforming Terms
See also: Thermal Dynamics
Technologies: Cutting, Pressroom Automation