Multiple Materials, Multiple Welds
Resulting from the detailed consultation and planning was a custom overhead gantry system employing two Fanuc robotic arms. In action, the robotic system welds large buckets, to 22 cubic yards and weighing as much as 28,000 lb., for use in quarries and steel mills.
The entire robotic-welding assembly was mounted in a 5-ft.-deep pit, 40 ft. long by 20 ft. wide and dug into the ACS factory floor to keep the 26-ft.-high assembly under the overhead crane. The system welds the bucket in six different axes, with a variety of wire diameters at each axis, starting with as little as 0.035 in. dia and going up to 1⁄16-in. dia.
With efficiency improving from 60 to 80 percent since employing the custom robotic-welding system, ACS Industries has seen its bucket orders jump, according to company officials.
“We will do anywhere from 3⁄8-in.-thick fillet welds to 1-in.-thick groove welds that require multiple passes,” says Bob Willoughby, ACS president. “Above a 3⁄8-in. thickness are all multiple-pass welds that require multiple movements and multiple programs for all of the axes.
“In many of our buckets we are welding two different grades of steel, which requires two different processes,” he continues. “Lincoln has helped us develop those processes and select the wire and gas required to weld the different grades. So it isn’t a process where you just stick a bucket up there and use one wire. The machine has to pause for us to change to the proper wire. We’ve been very successful at that.”
And given the rigorous demands of the buckets’ end use, quality and precision are paramount concerns, says Willoughby.
“These buckets are digging at the face of a granite wall, or they could be handling molten slag at 2800 F out of the furnace,” he explains. “So the welding of these products is critical, and ultimately impacts how they perform.”
While the development of processes and procedures is ongoing, initial results using the new robotic-welding system are exceeding expectations. Thus far, non-value-added labor has been reduced, and consistency of quality has improved.
“We know how much time these buckets take us to weld manually, and we know how much time they’re parked on our factory floor,” says Zeno. “Instead of parking there for 5 weeks, as they have in the past when we were welding them strictly on a manual basis, they’re usually only there for a matter of days. So the reduction in non-value-added labor is significant, exceeding 60 percent. That’s enabled us to offer quality products in a price-competitive way, and in most cases at a significant pricing advantage over our competitors.”
“Our efficiency has gone from about 60 to 80 percent,” adds Willoughby. “We’re obviously aiming for 100 percent. I don’t know that it’s possible to ever maintain 100 percent on a continuing basis, but it’s a goal that we continue to work toward.”
More importantly, ACS believes that the introduction of this technology has made a statement about the level of quality and service the company is prepared to provide to its customers. The results have been multi-layered: increased growth and profitability in its existing business, as well as new opportunities in yet-untapped markets. For example, the robotic-welding technology has helped ACS initiate a bucket-development program, culminating in a major OEM increasing bucket orders by $1,500,000 to date. ACS also has accelerated sales growth into the aggregate-mining and steel-production industries.
Look for Future Technology Investment
Integrating the gantry robot with their existing processes took time and persistence.
“We’re still in that learning phase,” says Zeno, “but we’ve covered a lot of ground, and we’re beginning to see the real tangible benefits of all the work that’s gone into this activity.”
Even with the system up and running, Lincoln Electric continues to provide guidance, support and fine tuning in response to ACS’s processing needs and the changing demands of the industry.
“Things continue to change,” says Zeno. “The things that you put to bed today may not necessarily be put to bed tomorrow. If our business continues to grow in a way we believe it will, there’s going to be a need for additional equipment and robots. With our past success as a great foundation, ACS and Lincoln Electric will be able to incorporate all of the things we’ve learned collectively on this robot into what we’re planning for the future.” MF
Article provided by Lincoln Electric Co., Cleveland, OH; 888/935-3878, www.lincolnelectric.com.
See also: Lincoln Electric Co.
Technologies: Pressroom Automation
Comments
Must be logged in to post a comment. Sign in or Create an Account
There are no comments posted.Four on the Floor—Toledo Integrated Systems at FABTECH 2024
November 5, 2024
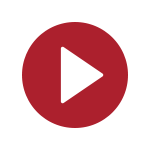
Canway Equipment Mfg. Tandem Line in Operation
Wednesday, July 16, 2025
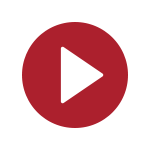