Those partnerships have led to the development of new curricula. “Nucor, working with the Association for Iron & Steel Technology, has spearheaded the implementation of new courses,” Brooks says. “Industry moves faster than academia. In addition, at several schools we help operate summer bridge programs, where we introduce new students to material science and metallurgical engineering and talk about the opportunities in industry for those majors. We also provide laboratory equipment and steel samples to enable students to perform tensile tests, conduct corrosion testing and the like. In some cases, they’re even working on real projects to help us study new processing techniques.”
Last but not least are internship programs and job opportunities for those students interested in careers in steelmaking upon graduation.
“We focus on eight universities,” Brooks says, “primarily small engineering schools (except for Purdue). These schools need resources that we can help provide. We send our teammates to these campuses regularly to maintain our presence and work alongside their students. Since 2012 we’ve brought hundreds of teammates on at the undergraduate level through internships, most of which then become full-time employees. Some even have progressed through the company to become general managers at our divisions. Identifying talent early, and nurturing it, is the overriding strategy.”
New Diversity Initiatives
Recently, Nucor has focused efforts on diversifying its talent pool, “again, to ensure that supply exceeds demand when it comes to engineering talent,” Brooks shares.
As such, earlier this year Nucor launched partnerships with three national organizations—the Society of Women in Engineering (SWE), Society of Hispanic Professional Engineers (SHPE) and the National Society of Black Engineers (NSBE). “Early returns on these partnerships are excellent,” Brooks says. “Already we’ve hired interns from all three organizations. When we look at diversity, we believe that we need diverse mindsets within the company to help us become more efficient and profitable.”
Student athletes represent yet another talent pipeline for Nucor, “because athletics at universities are by their nature diverse,” Brooks adds. “Now, as we’ve already made great strides in diversifying our talent pool, we can go back and ask our diverse employees to help recruit, since diverse students can see themselves in the reflection of our company.
“These efforts have made their way to the very top of Nucor,” Brooks continues. “Our new CEO, Leon Topalian, appointed in 2020, has been up front with diversity challenges facing U.S. manufacturing companies. He fosters communication throughout the company on race issues, and works to ensure that we support our diverse employees—not only at work but also within the communities in which they live.”
The Nucor Academy
In addition to metallurgy and material science, plant maintenance also takes on a critical role for Nucor, fostering a continuous need for degreed electrical engineers—“an area where we’ve seen growing demand and waning supply,” Brooks shares. “Here’s where the Nucor Academy plays a vital role.”
Born at Shelton State Community College in Tuscaloosa, AL, the academy is run from the Nucor Tuscaloosa steel mill (which manufactures carbon and pressure-vessel steel coil, discrete plate, and cut-to-length plate). “We have teammates there working as electricians or that have training in electrical engineering,” Brooks says, “so they understand well the electrical needs at our plants, particularly those related to plant maintenance. They worked with the professors at Shelton State to design a curriculum to best fit our needs, and those of most manufacturing companies. We helped them develop the curriculum, and regularly review their KPIs every trimester.
“We support incoming students financially,” Brooks continues, “paying not only for their education at Shelton State but also their housing in Tuscaloosa. And, when the students are not in school, they work at the Nucor plant. They get their own space where they can complete their schoolwork if they want to, as well as perform hands-on work for the plant. They work alongside the team at the mill to apply their newly gained knowledge. Then, during the summer months they can go work at any other Nucor facility or rotate during the 3-yr. program to different divisions to experience a more diverse environment.
“We graduate 12 to 15 students annually from the program, a win-win,” Brooks adds. “School and housing is paid for, and they have excellent job opportunities when they graduate with a clearly defined career path.” MF
See also: Nucor Corp.
Technologies: Training
Comments
Must be logged in to post a comment. Sign in or Create an Account
There are no comments posted.Apprentices at The Bradbury Group Among Scholars in State Pr...
Wednesday, May 28, 2025
Plant Floor as Path to College? Must it be Either/Or?
Kate Bachman Thursday, March 27, 2025

PMA Educational Foundation Accepting Scholarship Application...
Wednesday, February 19, 2025
Insights on Workforce Development with Joe Barr of Mursix, E...
Tuesday, February 4, 2025
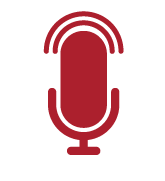