Spring Selection—Shoot for Two out of Three
When selecting the right coil spring for the job at hand, Osborne offers a simple and often-cited anecdote, along the lines of ‘good quality, low price and fast delivery.’
“Typically a metalformer can get any two of these three,” he says. “And with coil springs it’s the same—where the three variables are force, deflection and spring life, and you can only get two of the three. For example, if you need a lot of force over a large deflection, don't expect long life. In this case, nitrogen-gas springs might make sense.”
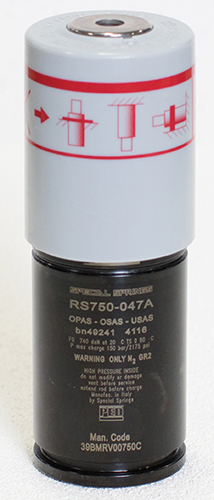 |
In gas-spring applications requiring a lot of die lube, be sure to protect the springs from contamination by using protective rod covers (shown here) or wipers. “Contamination is a leading cause of spring failure,” says Special Springs’ Jim Glynn. |
An exception to this rule, says Osborne: springs used for misfeed protection within, say, an in-die tapping device. “You need high force and long travel,” he says, “and you don’t care about life because the springs operate statically—in a healthy application they never cycle. So, even though they are under considerable preload and expected to travel a long distance, they rarely if ever actuate, so their life will not be a consideration.”
Lastly, Osborne issues a warning to manufacturers looking to use die springs for non-die or mold applications, which he says is becoming more common. Here the user needs to fully understand spring rate, or the spring constant, that governs the force-deflection curve.
“Typically, spring manufacturers provide a spring-rate tolerance of ±10 percent,” Osborne says. “This works fine for dies and molds, but in non-tooling applications it may not suffice; the application might require a tighter tolerance on spring rate. For these applications, many manufacturers offer (for a premium) springs with the constant controlled to within ±3 to 5 percent.”
Gas Springs: Heed the End Force
When it comes to specifying gas springs, Glynn notes that most are rated for a maximum speed of 1.8 m/sec., and, depending on press stroke, gas springs can run at press rates to 200 strokes/min.—depending, of course, on the amount of stroke.
“With just a shorter stroke, less than 12 mm,” he says, “you can run with gas springs at faster press speeds. But, with more than an inch of stroke, press speed can be limited to around 100 strokes/min.—the limiting factor being the heat caused from the friction and pressure rise in the springs. When selecting the right gas spring for the application, the stamper must carefully consider the force profile needed for the entire spectrum of forming, piercing and stripping requirements.
“Also important is understanding where you need the force,” Glynn continues. “Gas springs provide force on contact, and the force can increase as much as 50 percent as the piston rod compresses. If the stripping or forming force is calculated for the end of the stroke, then the die designer may be able to use fewer springs and reduce die cost, since the end-of-stroke force can be significantly greater than the initial contact force.”
While most gas-spring manufacturers offer a variety of sizes in terms of force, diameter and overall length, the industry, Glynn says, is settling in on ISO and VDI (The Association of German Engineer) standard gas springs. Most major gas-spring manufacturers comply with these standards, which allows the springs to be interchangeable and helping stampers reduce downtime and cost.
Glynn warns, however, that “when repairing gas springs, use the repair kit specified by the manufacturer—these are not interchangeable. And, as a general rule, I recommend that shops only repair gas springs with a body diameter larger than 50 mm.”
Sharing Other Best Practices
Glynn stresses that die designers should specify gas springs so that only a maximum of 90 percent of rated spring stroke is used. “The less stroke the better,” he says, “to reduce friction and pressure and prolong spring life.”
Also sound practice: Ensure that the spring sits on a flat surface, with the rod perpendicular to the striking surface or pad. This is critical to avoid side loading.
“To optimize spring life,” Glynn adds, “attach springs using a mount or the tapped holes in the bottom of the springs, so they’re not loose in the die. If the springs aren’t fastened, metal contaminants or debris can wedge their way underneath the springs, which would then create a misaligned or angled spring and lead to side loading.”
If stampers do elect to just drop the springs into the pockets machined into the die, Glynn suggests that they design the pockets with clearance based on the manufacturer’s recommendations, to minimize the chance of contamination. And, in applications requiring a lot of die lube, use springs with protective rod covers or wipers to guard against contamination, “a leading cause of spring failure,” he says.
Connecting Gas Springs to Control, Adjust Force
Hosed or linked nitrogen systems provide the most flexibility for metalforming. “Gas springs can be linked together,” Glynn explains, “with a series of high-pressure hoses, or via a 1-in. manifold plate. This system is the cleanest and, I believe, the most reliable.”
To take this a step further, designers can add pressure switches (electronic pressure monitors) to the system, Glynn says, allowing the stamper to set parameters based on the pressure profile that optimizes part quality. And, should pressure fall below a certain level, due to a leak in the system, it signals the press to stop.
A great example of the benefits of connecting gas springs via a manifold setup, says Osborne: in-die tapping, where considerable stripper travel is needed to locate and control the part during the tapping operation.
“In some cases,” Osborne notes, “the tapping unit is mounted in the upper die, within the stripper. It is critical that those gas springs be linked together to ensure uniform balance in the stripper pad. Otherwise, should one or two gas springs go flat in one corner, the stripper won’t hold down firmly in that corner, which can wreak havoc with the tapping unit and lead to broken taps and cause damage to the unit. It’s mandatory that stampers use a manifold when using nitrogen for in-die tapping operations.”
A Critical Note About Safety
Lastly, Glynn notes a relatively new focus on safe use of gas springs, which came to light in November 2015 when VDI added new safety guidelines to its VDI 3003 Standard, “Nitrogen Gas Springs in Large Stamping and Forming Dies.” These guidelines arose from the fact that gas springs, under high pressure require that safety be top of mind.
“Because these springs contain a lot of pressure,” Glynn says, “which can range from 2000 to more than 4000 psi during compression, they’re nothing to fool around with. Because of this, we and other manufacturers have focused on developing new safety features, following the VDI guidelines. These fall into three categories: protection from over-stroke and over-pressure, and protection from return stroke without counterforce.”
Here’s the language contained in the VDI standard:
• Return stroke of nitrogen-gas spring without counterforce
Do not use gas springs in such a way that the piston rod is released freely from its compressed position. This can be caused by a jammed pressure pad or cam. As a result, the nitrogen gas spring exceeds the permitted speed during the return stroke, causing the piston rod to slam unchecked onto bushing. This can damage the nitrogen-gas spring or cause it to fail (high-speed return of the rod). To avoid this, use only nitrogen-gas springs that are designed to vent gas, thereby depressurizing the spring.
• Over-stroke
Over-stroke occurs when the piston rod is pushed deeper into the gas-spring body than the nominal stroke length. This can damage the gas spring. Use only gas springs that are designed to vent the gas completely to atmosphere in a controlled manner in the event of over-stroke.
• Over-pressure
Gas springs can break if the pressure inside rises due to fluid penetration or incorrect charging above the permitted limit. If fluids are used, it is advisable to ensure that gas springs have over-pressure protection. When the over-pressure-protection system is triggered, the gas is vented safely. MF
Industry-Related Terms: Tapping,
Tolerance,
Nominal,
Penetration,
Perpendicularity,
Piercing,
Plate,
Run,
Scrap,
Spectrum,
Stripper,
Stripping,
Stroke,
Surface,
Cam,
Case,
Corner,
Die,
Form,
Forming,
Gauge,
LinesView Glossary of Metalforming Terms
See also: Moeller Precision Tool
Technologies: Tooling