A Heroic Die-Handling Effort
January 1, 2011 A heavy-duty two-position die cart with a retractable bridge extension improves die-locating repeatability while enabling a 70-percent reduction in die-change time at a Metalsa (formerly Dana) automotive plant.
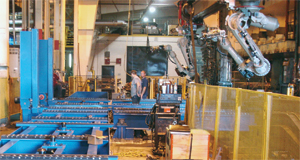 |
Automation abounds at Press 25 (3000-ton Clearing, 300- by 72-in. bed) at the Metalsa Structural Products (formerly Dana) facility in Hopkinsville, KY. Robots (right) move blanks and parts on and off the press, and a two-position die cart shuttles 80,000- to 100,000-lb. dies on and off the press bolster.
|
You won’t find too many presses as large as Press 25 at the Hopkinsville, KY, Tier One automotive plant of Metalsa. It’s one big press—a 3000-ton Clearing with 300- by 72-in. bed, blank-loaded to stamp frame rails for pickup trucks and motor homes. The press hit the production floor of the 420,000-sq.-ft. plant in 2000, commissioned for manual transfer work. For ergonomic reasons—the large frame rails proved a challenge for workers to man-handle—in 2004 plant management added four robots to the press line to move parts in and out of the dies. But while the robots solved one issue, they created others.
“When we were manually transferring stampings in and out of the dies at Press 25, precise die location was not a critical requirement,” says Barry West, a project engineer at the Metalsa Structural Products facility. The plant supplies structures for light and heavy trucks, buses and passenger cars. Die locating via a groove machined into the bottom of each tool and a ball-shaped locator in the press bed produced die-location repeatability to within ½ in. or so, accurate enough to accommodate manual parts transfer. However, when robots entered service, the half inch of die-position variability required operators to reprogram the robots with every die change—a regular occurrence.
“We’ve run anywhere from eight to 12 different tools on that press over the years, and we change the dies out at least once per shift,” says West. “Reprogramming the robots added at least 30 min. to each die-change cycle.”
Overall, die changes would take an average of 200 min., West recalls, thanks not only to robot reprogramming but also in part to yet another issue presented when the plant added the robots to Press 25: it had to add a blank feeder to the front of the press. “Every time we went to change dies,” West adds, “we had to use a crane to move the blank feeder out of the —there’s no room (in the 100- by 200-ft. press bay) behind the press to accommodate die changes.”
There’s Got to be a Better
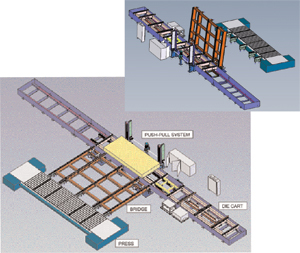 |
The die-change system includes a retractable drawbridge to span the 22-ft. gap between the die cart and press. Telescopic rigid-chain actuators combine with a gear motor to create a push-pull system that powers controlled die movement. |
When operators finally had had enough of completing 3-plus-hr. die changes using what West refers to as a flat-bed die hauler to move dies in and out of Press 25, West and the Hopkinsville team went looking for a more efficient and accurate solution. Goals included improving die-locating accuracy; enabling die changes without having to endure the time-consuming task of moving the blank feeder out of the and then back into position with each die change; and the ability to handle the newest dies sent to the press—huge two-piece 300-in. 100,000-lb. tools for stamping motor-home frame rails.
What the team settled on is a two-position die cart positioned at the rear of the press and outside of the operating bounds of the existing automated part-palletizing carts, which accept the robot-unloaded stampings. The system (engineered and manufactured by Serapid Inc., Sterling Heights, MI) moves the dies 22 ft. between the press and die cart via a retractable bridge extension. Serapid engineered the drawbridge concept to bridge the gap between cart and press when it was discovered that the press bay lacked sufficient room behind the press to accommodate telescopic bolster extensions.