The researchers performed their metal forming tests on 210-mm-dia. round blanks, drawn into 50-mm-square 40 mm deep for dual-phase steel and 50 mm deep for Gen3 steel and Al 6005. The holding force at the start of the forming stroke was set to 180 kN and a total of 3 g/m2 of lubricant was applied consistently on both sides of each blank. Draw depth: 40 mm for dual-phase steel and 50 mm for the Gen 3 steel and Al 6005. As a base line, they set forming speed to 20 rpm—approximately 270 mm/sec. or 245 mm/sec. at contact, depending on the draw depth. Later, they used motion profiles such as soft contact, pulsating, dwell and constant speed for comparison (Fig. 3).
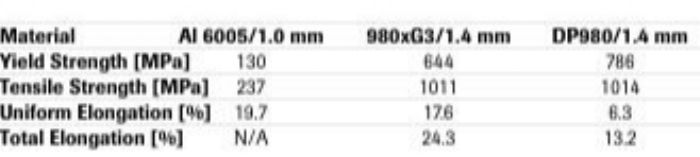
The first parameter of interest: forming speed, or whether a drawing operation should be conducted quickly or slowly. While the common opinion among stampers is to reduce forming speed to improve drawability, results of the tests using the servo press were counterintuitive. For all materials tested, researchers consistently observed better results at 20 rpm (245 to 270 mm/sec.) rather than at 5 rpm (61 to 67 mm/sec.). A lower force measured when drawing at 20 rpm supports these results (Fig. 4). Nevertheless, only adjusting speed proved useful only when forming the Gen 3-steel cups 50 mm deep; while drawability increased in all cases, they still observed fractures at 20 rpm when forming DP980 40 mm deep, and Al 6005 50 mm deep.
What About a Pulsed Press Profile?
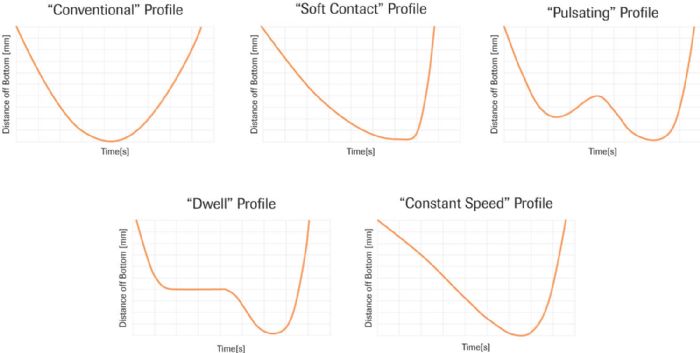
As an alternative, researchers investigated the use of a pulsating force profile (Fig. 3), designed with one pulse at 80 percent of the draw depth. This alternative method proved useful when drawing the Al 6005 cups (Fig. 5) but not DP980. Rather, to successfully form the DP980 cups, a dwell profile worked best, using a 0.5-sec. dwell at 50 percent of the draw depth. Finally, to improve the drawing process on the Gen 3 steel, a constant-speed profile proved ideal, along with the addition of a soft contact to reduce vibration on the tools and the press (Fig. 6).
While the fundamental principles behind the results obtained remain under investigation, one clear conclusion appears: Servo-motion profiles can help improve drawability. Nevertheless, a tradeoff must be considered. That is: Any of the proposed motion profiles require additional process time, leading to lower production rates in exchange for improved material formability and reduced press and die maintenance. Process engineers should compare the costs related to scrap rate, press downtime and tool maintenance versus the costs of a lower production rate.
To keep the production rate as high as possible using servo-motion profiles, it is important to use a servo press with low inertia and capable of quick accelerations and decelerations. In addition, some of the proposed motion profiles require a press with a special lubrication system that allows for dwell time under certain loads.
Finally, an optimized software is necessary to enable design of the motion profiles with the highest production rate while minimizing energy consumption. Here, be sure to work closely with your press manufacturer regarding press selection and motion-profile design. MF
See also: Nidec Press & Automation
Technologies: Stamping Presses