Perforated Metals Add Punch to Product Designs
August 1, 2011 We spoke with the Industrial Perforators Association and association member company Ferguson Perforating for a close look at the unique metal-perforating process, which competes with thermal hole-drilling processes due, in part, to its ability
to create thousands of holes per minute without creating a heat-affected zone.
Perforating presses precisely punch hundreds of thousands of holes in sheetmetal per minute, programmable to meet the whims of product designers seeking to vary hole spacing and develop custom hole patterns for aesthetic purposes, as well as to meet product-performance goals. Perforated panels find applications in numerous industries—architectural (lighting fixtures, wall panels, sound-absorbing structures), aerospace (fuel and air filters), appliances (strainers, microwave screens), automotive (diffusers, muffler guards), HVAC (ventilation, enclosures) and others.
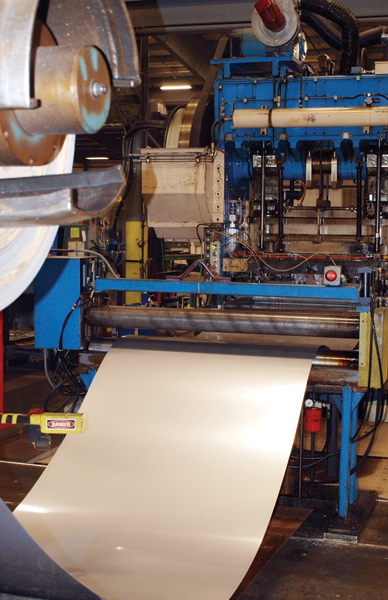 |
Nearly all of the material running through the Ferguson Perforating facility feeds its perforating presses as coil stock; 10 percent comes into the plant as blanked sheet and plate. Presses can punch as many as 400,000 holes/min., and 1000 holes/sq. in. |
Most metal perforators are job shops that change out their presses five to 10 times per shift, running lot sizes from a few to several thousand—at the low end, think ceiling panels for an airport; and the high end, think dishwasher strainers.
To learn about this unique process and the select few companies that specialize in it, we spoke with the Industrial Perforators Association (IPA), Milwaukee, WI. IPA represents 10 North American perforating companies, nine international perforators and seven associate members/suppliers to the industry. Among other services, it publishes the “Designers, Specifiers and Buyers Handbook of Perforated Metals,” developed as a resource for its member companies and their customers. Topics include strength and elastic properties of perforated metals, how perforated metals are used in acoustics and EMI shielding, and checklists for perforating cost influences and for ordering perforated metal. It’s available for download at www.iperf.org.
Controlled Breakage
“While metal stamping is controlled forming, perforating is controlled breakage,” we were told by Bob Colombi, sales manager for IPA member Ferguson Perforating. “The workpiece material has to break a in the die exactly the we want it to, to ensure we meet quality specifications for hole dimensions and surface finish. The press drives the punches about 30 percent through the thickness, then the material fractures when stressed to its shear strength. The process creates considerable compression in the bottom of the sheet and tension in the top, so secondary leveling plays a critical role in equalizing these stresses and creating a flat part, typically to meet IPA or customer standards for camber and flatness.”
We met up with Colombi at Ferguson’s plant in New Castle, PA; the company’s headquarters and 65,000-sq.-ft. main production facility are in Providence, RI, which also houses a fully equipped CNC machine shop and toolroom. “Levelers are not designed for perforated sheet,” says Ferguson plant manager Howard Turner. “Maintaining critical hole and web tolerances adds a whole new dimension to the process. We might have to run material through in different directions, using five or six passes in some cases.”
“When you’re talking about punching more than 1000 holes/sq. in., in some cases,” says Colombi, “alignment of the punch, stripper and die plate is critical during perforating. Designing and manufacturing our own tooling inhouse helps to ensure the required level of quality.”
Other critical technology focal points for Ferguson and other IPA member companies include punch coatings, to minimize heat input to the workpiece material during perforating, and new tool steels such as powdered-metal alloys, which prove particularly useful for those applications requiring punching hole diameters exceeding material thickness. Minimal heat input from the perforating process proves particularly beneficial in numerous applications, as customers consider competitive processes such as plasma and laser drilling.
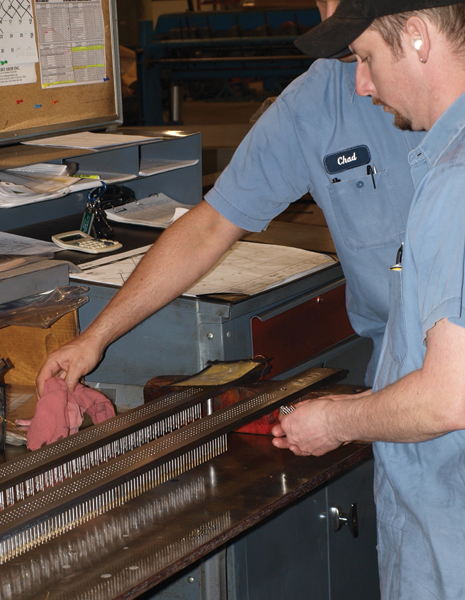
|
Ferguson press operators prepare a tool set loaded with hundreds of perforating punches, aligned in rows and staggered to control press tonnage. |
“Thermal drilling als creates some heat-affected zone on the rim of each hole,” says Ferguson plant manager Howard Turner, “which affects material properties. Perforating, being a purely mechanical process, avoids this concern. We’ve seen designers opt initially for laser drilling and then later come to recognize the negative impact from the heat-affected zone created—such as weldability—and switch to perforating. This has occurred in the aerospace and nuclear-industry applications, in particular.”
“The one-to-one ratio of hole diameter to workpiece thickness pretty much holds true when perforating carbon and stainless steels,” continues Turner, “but in aluminum and copper, we can exceed that ratio. For example, we routinely punch 0.040-in.-dia. holes in 0.080-in. aluminum-alloy sheet.”
Holes can be round (0.016- to 2.0-in. dia.), as well as oblong, square, hexagonal and conical; hole patterns can be straight or staggered. In addition to hole diameter, hole spacing becomes a critical variable—in design and in accurate production.
“While some applications call for a wire mesh product,” says Colombi, “where more strength is needed in the perforated part, we can precisely control hole spacing. The web typically should be equal to or larger than the material thickness.”