“Our supplied deep-drawn parts came to us with undefined and irregular addendum or overpress material,” says Quinn, “which made the trimming process in our five-axis waterjet-cutting machine very time-consuming. Every fender or fuel-tank stamping would require a unique setup in the cutting machine. Now, using the Beckwood press, we’ve been able to define the addendum for every stamping and obtain enough repeatability to allow us move right from the press to a fixture on the waterjet machine. We stamp a few fixturing dimples in the material to locate the drawn blank in the waterjet fixture, and in about 2 min. the operator can set up the blank and start trimming out the fender. This took 10 min. out of the setup process per fender.”
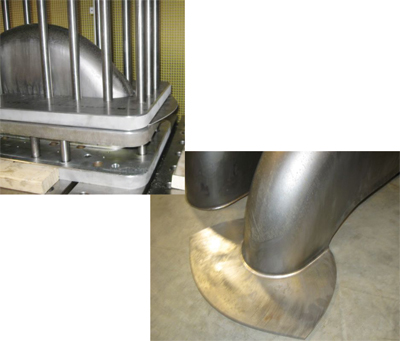 |
After bringing deep drawing inhouse, OCC worked with Beckwood engineers to fine-tune the drawing process and develop a custom draw ring to achieve wrinkle- and tear-free 14-in. draws on fender blanks, shown here. It also obtains a repeatable addendum shape that allows an operator to fixture, in just 2 min., each blank in the firm’s five-axis waterjet-cutting machine for final trimming. |
Fenders are 28-in.-OD half-donut shapes, 5.5 in. wide, with a 14-in. draw. “We use only 70 percent of the drawn blank in the actual fender,” says Quinn, whose background is in fineblanking and progressive-die stamping. He described the process used to develop the fender blank profile, and the “art-to-part” development required to eliminate the wrinkling and pinching into the upper draw ring that you might expect when attempting to develop a 14-in. draw.
“A lot of art and trial-and-error development went into the project,” he says, “as we worked together with Beckwood’s technicians to finally obtain the part quality we were after.” Among the changes made during trial and error were the blank shape and the recipe for draw-ring pressure, so that by the fourth blank stamped, Quinn wound up with a usable part, and by the 12th blank the process was fine-tuned to form wrinkle-free parts.
Custom Draw Ring
Flattens the Wrinkles
“The blank wound up being an elongated oval,” says Quinn, who started with a dog-bone-shaped blank. “Then, once we defined the optimum blank shape, one of the first process parameters we identified as critical was draw-ring clearance. As the fender would make its nearly-90 deg. turn up the side of the draw ring and around a 3⁄8-in. corner radius, the steel would start to tear. So we added another 1⁄16 in. of clearance in the deeper ends of the draw, which eliminated the pinching that was causing the tearing.
“Then,” Quinn continues, “to eliminate the wrinkling we were getting in the middle of the part—the mounting area—I added side plates to the draw ring.” The draw ring is of 1.5-in.-thick 7075 Al; Quinn added 6 in. of flat stock to each side of the ring to smooth the edges of the fender as it draws down.
“I also machined a plate to mount to the pressure pins that hold the upper die,” he adds, “to fill the gap between the edge of the part and the pins. We use the pins to support the stamping in the outward direction as well as in the drawing direction. They act just as the cushion plate and the draw ring act together to pinch the material, so now we also get the same pinching action between the male form and the upper draw ring. This prevents outward wrinkling.”
Dynamic Cushion Control, Four-Corner Active Leveling
After fine-tuning the tooling, Quinn then looked to use the multizone bed cushion (rated to 75 tons) of the press, which allows OCC to program and adjust draw-cushion pressure in as many as five different stages of the draw. At max, OCC uses 200 tons from the main ram and 66 percent of cushion capacity. Pressure is higher at the start of the draw, reduced in the middle of the draw and then increased again at the end. This dynamic cushion control throughout the stroke, in addition to programmable ram speed, “allowed us to really fine-tune the draw at its deepest point, between 12 and 14 in.,” says Quinn. The press is rated for a maximum draw of 16 in.
In addition to dynamic cushion control, another key feature of OCC’s new hydraulic press is four-corner active leveling. Beckwood application and sales engineer Darrell Harrelson explains how the feature works and what it means to OCC’s applications.
“Linear transducers mounted at each of the four corners of the press send position signals to a motion controller (from Delta Computer Systems, Vancouver, WA). The controller manages the data to control proportional valves in each of the four hydraulic cylinders to maintain bed parallelism, critical during off-center loading conditions.”
When does OCC load its press off-center? “This occurs when forming the oddly shaped gas-tank halves,” Harrelson continues. “The tear-dropped shape of the tanks generates substantially more load on one side of the press bed than the other. Without active leveling at all four corners of the press, this off-center loading would stress the guide bushings, possibly bend the pusher pins or otherwise damage the die. The diemaker would have to look at the part and locate the centerline, then shift the part in the press to even out the load on the press.”
Last but Not Least:
A Green Machine
The last press feature noted by Harrelson is its use of a variable-frequency drive, growing in industry acceptance as a to “green” the stamping process. When the press is not running—and the nature of OCC’s limited run sizes causes a lot of downtime—the drive consumes only 50 percent of its rated energy, slowing from 1800 rpm during drawing to 900 rpm during idle time.
“This speed reduction conserves energy,” says Harrelson, “and also reduces heat in the hydraulic system and reduces sound level. Generally, payback for this feature comes in less than 4 yr. in terms of energy savings.” MF
Industry-Related Terms: Bed,
Blank,
CNC (Computer Numerical Control),
Corner Radius,
Corner,
Die,
Draw Ring,
Draw,
Drawing,
Edge,
Fixture,
Form,
Forming,
Hydraulic Press,
Lead Time,
Model,
Plate,
Ram,
Run,
Stroke,
WrinklingView Glossary of Metalforming Terms
See also: Beckwood Press Company
Technologies: Stamping Presses