Do You Place a Dollar Value on Downtime?
November 1, 2016 If not, then youre likely operating at a disadvantage in an increasingly competitive market. Heres one metalformer's strategy for diminishing downtime, leveraging Industry 4.0 technology, with impressive results to show for it.
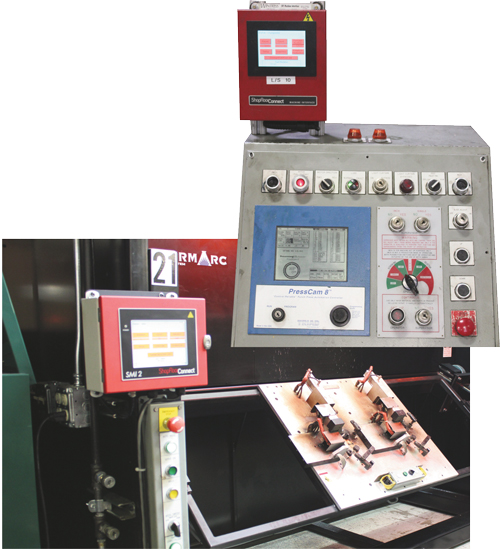 |
ODM has installed ShopFloorConnect data-collection devices on 10 of its presses (top) and on its four robotic-welding cells, providing detailed downtime-runtime analysis to help the metalformer optimize OEE. Data analysis has led to continuous-improvement projects focused on activities such as quick die change and development of ergonomic weld fixtures. |
Any number of ailments and wounds can impact metalforming-shop performance—unusually slow die changeovers, untimely and overly time-consuming press or die repairs, and unexplained and inconvenient expediting of materials are just a few. Shop management can either take a quick and easy Band-Aid approach to healing these wounds and watch them reappear, or focus on root-cause analysis and cure them forever.
At Chicagoland metalformer ODM Tool & Mfg., Inc., a focus on root-cause analysis and a more permanent approach to ensuring optimum shop performance has led to a significant boost in overall equipment effectiveness (OEE), and a corresponding drop in downtime. Several factors contribute, such as better use of predictive and preventive maintenance, and closer policing of activities—die changeovers on presses and cycle times through robotic-welding cells, for example. All of these activities have one common thread: real-time gathering of production data, and visibility of that data by management to enable quick and decisive action. It’s a terrific example of Industry 4.0 connectivity impacting the metalforming industry.
Cost Justification, Due to Downtime Evaluation
If you’re not operating as a ‘smart shop’ today, and lack plans to become one, you’re likely a ‘dumb shop,’ or on your way to becoming one. And I have no doubt that the smartest metalforming shops will likely be those that survive the next industry downturn, whenever that occurs.
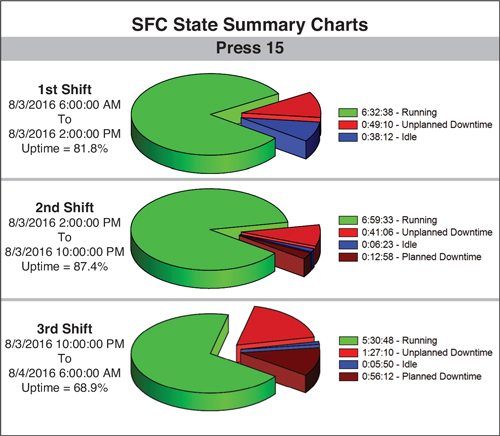
|

|
Examples of the type of data ODM managers receive from ShopFloorConnect—daily and weekly downtime-runtime summaries. |
For ODM, the quest to become smart landed on firm ground early in 2015 with an investment in Wintriss’ ShopFloorConnect technology. That followed several years of concerted and ongoing efforts to upgrade press controls on its mechanical presses to Wintriss SmartPac 2 units. When asked to explain how management justified the cost of such technology upgrades, Jay Michaelsen, ODM vice president of operations, says:
“With all of the growth we’ve experienced without adding a lot of new equipment or people, we had to become smarter at managing the assets we already had. The key to accomplishing that was putting a dollar value on downtime, and then committing to a process to ensure that we minimize downtime throughout the plant. Once we established the value of downtime and used our new controls and Industry 4.0 connectivity solution, we quickly (in less than three months) realized a full payback on our control-technology investment.”
ShopFloorConnect employs data-collection technology able to be installed at any machine in the factory, and uses electrical signals from the machines to monitor runtime and parts counts. By inhibiting a machine from operating until the operator has entered a downtime code/reason, managers gain a clear picture of exactly what’s happening at each machine. And, as noted by Michaelsen, when operators know that management is keeping a close tab on operations, the shop tends to run much more effectively. ShopFloorConnect also features an alert feature that sends e-mails or text messages when downtime exceeds what is expected for each machine activity—die changeovers or weld-fixture load/ unload, for example.
Connected Presses and Robotic-Welding Cells
Do your shopfloor managers know if the same job runs at the same hit rate every time? Do they know if a value-added assembly job runs at the same cycle time for every lot? And, even if they do know where process inconsistencies lie, do they have any data-based and supported methodology for understanding why the processes fail to run at consistently high levels of efficiency?
Unless you’ve equipped the shop with data-tracking and online analysis tools, chances are that any efforts to fine-tune efficiency are stabs in the dark without much data to support those critical decisions. And, often those attempts are made after the fact, when productivity already has suffered and the impact is felt throughout the plant.
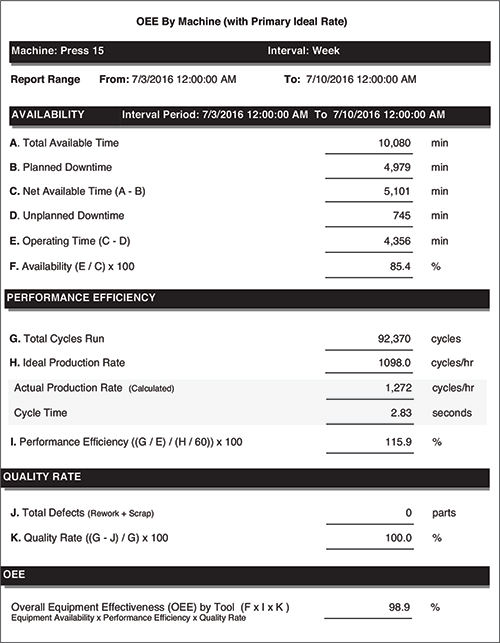 |
OEE reports, by machine, help identify continuous-improvement opportunities, to unearth hidden press time and allow ODM to bring in more work without adding new capital equipment. |
“We prefer to fine-tune our processes and react early to prevent big problems late in a run,” says ODM production manager Brandon Enright.
Enright has overseen the installation of SmartPac 2 controls on four of ODM’s 17 mechanical stamping presses (200- to 1500-ton capacity), and ShopFloorConnect on 10 presses and on its four robotic-welding cells. Compared to its older press controls, the SmartPac 2 units “provide added functionality that helps us get back up and running whenever there’s an issue with a press,” says Enright. “For example, we just don’t learn that a sensor has faulted, now we know how it faulted, which is huge in terms of identifying a root cause of the problem more quickly. Also, new tonnage-monitoring functionality allows us to develop a history of the tonnage over a tool’s lifetime, again helping identify early-on when a tool needs maintenance prior to something catastrophic happening.”