Leveled Sheet and Plate Improves Manufacturability
April 1, 2013 ...at this German manufacturer of trailers and semitrailers with payload capacities to 10,000 tons.
Processing leveled sheetmetal can provide enormous added value, as evidenced by the experience of heavy-duty trailer manufacturer Goldhofer, Memmingen, Germany. The need for leveled sheetmetal becomes obvious, say Goldhofer officials, when it comes to stamping presses, laser-cutting machines and press brakes, proven out when the firm recently installed an Arku FlatMaster 120 roller leveler.
Says Goldhofer production manager Alois Rothermel: “We now offer enormous added value when working with the leveled sheetmetal. Since purchasing the FlatMaster, we have experienced the importance of processing leveled materials through the production process. We absolutely underestimated this effect when considering the investment beforehand. We have received exceptionally positive feedback from every production department regarding the new leveler. The improvements were consistently noticeable from prefabrication through to edging, assembly and welding.”
Adds Klaus Desiderato, the firm’s head of preproduction: “Using our older vertical press to level material created a bottleneck in the production process. We were only leveling 65,000 parts from our total annual volume of 300,000 parts. Now, the FlatMaster’s efficiency allows us to level 90,000 parts per year.
“Many parts which previously were leveled using our older leveling press,” Desiderato continues, “now are leveled with the FlatMaster during preproduction. Because we level a significantly higher number of parts than originally planned, the bottleneck at the vertical leveling press has diminished noticeably and the FlatMaster now runs three shifts.”
The Figures Speak for Themselves
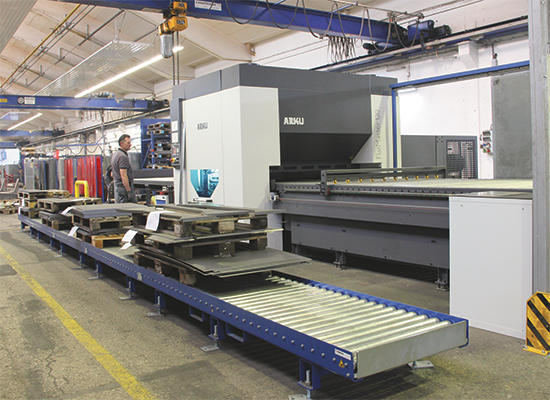 |
While Goldhofer’s old leveler required 5400 hr., or 3.2 shifts, to level 65,000 blanks, the Arku FlatMaster 120 can complete the same amount of work in only 2160 hours, or 1.3 shifts. The leveler processes materials ranging from 3 to 30 mm thick, and can handle high-strength S960 steel (140,000-PSI yield strength). |
Goldhofer’s old leveler required 5400 hr., or 3.2 shifts, to level 65,000 blanks. Now, the FlatMaster 120 can complete the same amount of work in only 2160 hours, or 1.3 shifts. As a result, the Arku machine frees up one employee for other duties. The machine also delivers further savings for assembly and welding procedures. Even when conservatively calculated, the leveler still delivers further savings of approximately 600 hr./yr. As a result, Goldhofer would realize a return on investment of 5.7 years when run for a single shift. “The machine will definitely pay off more quickly than calculated,” says Desiderato.
Although the old leveler, nearly 60 years old, no longer could handle many of the current tasks required, Rothermel still sees its well-earned retirement with both a smile and a heavy heart.
“Many years ago I purchased the machine second-hand together with our company founder, Alois Goldhofer. The machine served us well for decades.”
To upgrade its leveling capabilities, the firm first investigated three- and four-roll bending machines, typically used to shape plate into rings for furnaces or similar applications. With certain restrictions the machines also can be used for sheetmetal leveling, and given their significantly lower purchase price compared to a roller leveler, Goldhofer’s management considered the option.
Says Rothermel: “We thoroughly analyzed the actual costs and discovered a clear winner. Although more expensive to purchase, the roller leveler is significantly more efficient to operate. This is primarily due to the far greater overhead and space required when operating roll-bending machines.”
“In addition,” adds Desiderato, “when using a roll-bending machine, the chamfer at the start and the end of the sheet has to be removed using an additional vertical leveling press. And, the leveling process requires considerably more time. We would have needed at least three roll-bending machines to accomplish the same amount of work.”
Higher Strength and Thickness Capabilities
The firm’s old leveler could process only S355 high-strength low-alloy steel (50,000-PSI yield strength) to 15 mm thick. The Arku leveler processes materials ranging from 3 to 30 mm thick, and can handle the high-strength S960 steel (140,000 PSI yield strength) increasingly processed by Goldhofer. Says Desiderato: “The FlatMaster more than lives up to its name, even when working with these extremely high-strength steels. It makes them very flat.”
In addition, the ability to level smaller parts proved to be an unexpected benefit. “Previously, the smallest part we could level measured 400 by 400 mm,” adds Desiderato. “Now we can level parts half that size.”
The firm’s newfound ability to level more of its parts pays off at its welding and assembly cells. “Before, workers in those areas would have to press the parts onto the worktable using brute force,” Desiderato says. “And often, the heat generated during manual or robotic welding would release these forces and cause the entire structure to deform. That added a significant amount of rework (flame-straightening) time. “