Far Removed from the Press Shop
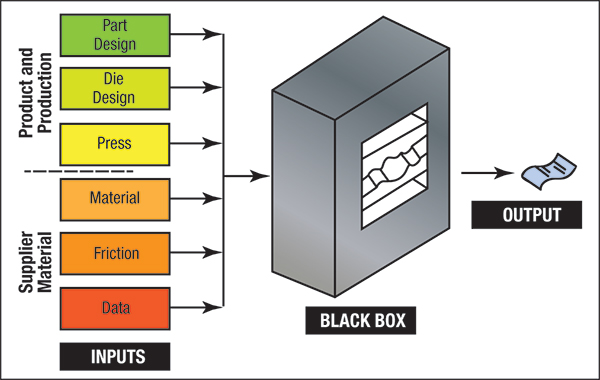 |
Fig. 1—The metalforming process can be analyzed as a system of inputs interacting within a black box to create a useful output. |
…metal suppliers, lubricant companies and troubleshooters have expertise in the other half of the knowledge base, but do not fully understand the mechanics and fine points of metalforming. Then, sheetmetal users and suppliers too often discuss only price rather than capability and compatibility required by the product.
The lack of personnel cross-trained in all six categories shown in Fig. 1 has cultivated the formability engineer. These people have sufficient knowledge of the stamping and the sheetmetal industry to treat the whole process—from part design to final stamping—as one interactive system. The formability engineer must be neutral and treat both sides equally based on process data.
How might a formability engineer assist with an actual problem? Consider the following letter from a press shop in trouble.
To: Jim, formability engineer
From: George, Average Stamping, Inc.
Subject: Problems forming a deep-drawn cup
Dear Jim:
For nine years we have successfully deep drawn cups with a hemispherical bottom. Recently we received a new design very similar in style to the old cup but with a deeper draw and more severe hemispherical bottom. The purchase orders we receive usually have a clause stating, “Steel to Make Part Number wxyz.” However, I learned that we are receiving common cold-rolled aluminum-killed draw-quality (AKDQ) steel. We were buying steel from two suppliers to ensure a continuous supply, and had to adjust the die and press when switching steels.
To my surprise, the purchase order for the new part contained a steel specification for CRS IF, 40 to 50 percent elongation, 1.6 minimum r value, 0.3 minimum n value. What does the IF do and how meaningful are the included values?
The new part has several problems (Fig. 2).
• Instead of four small ears equal in height around the open end of the cup, two longer ears now are being formed.
• Breakage occurs in the bottom dome where the end of curvature joins the straight cup wall.
• The die impact line is part of the up the cup wall and is a visual problem.
I have sent you a gridded new part so you can examine the actual problems. I did not include one of our old parts because they will be going out of service. Once you reach some conclusions we can talk about a contract for your work.
Best regards,
George, press shop manager
Dear George,
The IF designation applies to VD-IF (vacuum-degassed Interstitial-free) steel. This steel has reduced carbon content and added vanadium, columbium or other elements. Compared to AKDQ, VD-IF steel exhibits the increased stretchability (indicated by the n-value) needed for the larger hemispherical cup bottom. AKDK typically have an n-value of 0.18 to 0.23; n value for VD-IF steel ranges from 0.23 to 0.27. I do not know who specified your minimum n-value of 0.30, but to obtain n-values above 0.30 requires use of an austenitic stainless steel (3xx series).
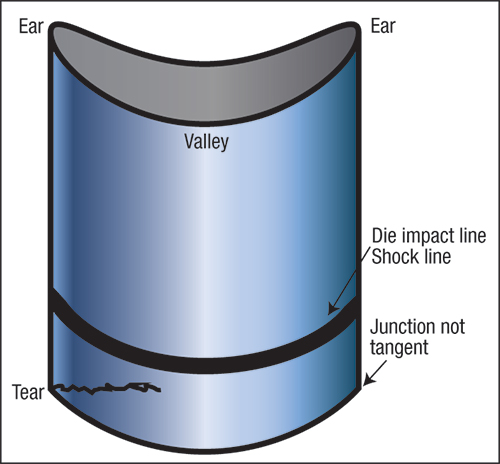 |
Fig. 2—This problematic part had two large ears instead of four small ears; a tear where the bottom hemispherical portion was not tangent to the deep-drawn cup; and a die impact line above the cup/hemispherical bottom junction. |
Buying steel from two suppliers usually leads to part variations when forming in the same die, due to differences in mechanical properties. I recommend you obtain the chemical and mechanical properties of the problematic steel, and for steel shipment that seems to perform better. This should indicate to the steel supplier the changes necessary to meet your requirements.
Normally, deep-drawn cups have four ears nearly equal in height, as produced by the die used to form the previous cup design. Two ears can be created by a special set of mean r-values, but that is quite rare. Instead, an elliptical punch or die ring typically gets the call for generating two ears. The two locations of reduced wall clearance tend to iron the sheet thickness and extrude the ears up the punch wall.
Take two blanks and draw a line marking the rolling direction. Place the first blank on the die with the line oriented front to back. Run the first blank, then place the second blank in the die with the line rotated 45 deg. from the first blank. If the ears rotate with the line, the problem is with the steel; if the ears remain oriented with the press direction, the die is the problem.
The breakage location in the dome results from a sharp change in punch radius when the hemisphere does not merge tangentially with the deep-draw cup wall. A severe strain gradient then creates a tear. The die impact or shock line first generated at this location moves up the deep-drawn cup area because the stretching of the hemisphere generates extra length of line that flows up the constant-diameter cup wall.
Sincerely,
Jim, formability engineer Technologies: Materials, Software