“We grew rapidly and significantly,” says Friedman, “but then culture shock hit us in 2004 with the launch of the GMT900 truck platform. That program included a new type of suspension system that reduced our sales volume for the platform by 65 percent, as most of the parts we were manufacturing were designed out of the vehicles.
“To fill the void, in 2004 we were awarded about $12 million in trailer-hitch business from GM,” continues Friedman, “and by May 2005 we were GM’s sole supplier of trailer hitches for pickups and SUVs.”
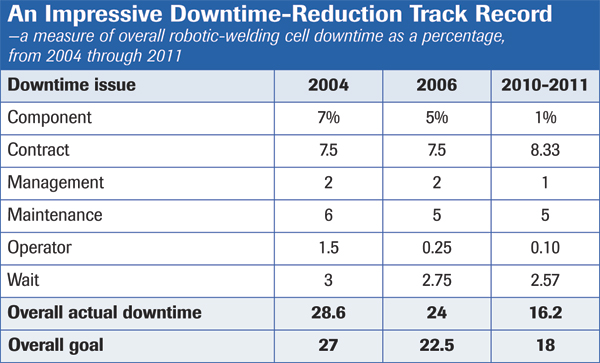 |
Northern Stamping segments, tracks and records robotic-welding cell downtime by several unique causes: component (poor-quality parts coming to the welding cells), contract (mutually agreed-to downtime, according to the union labor contract, for personal issues), management-related (for training, scheduled meetings, etc.) maintenance-related, operator-related and wait. |
Trailer-hitch work from GM, as well as takeover work from other hitch manufacturers, led to the installation of another five robotic-welding cells at the facility, including a quad cell with four robots (from Motoman) added in 2009. The quad cell originally was commissioned for welding Hummer axle crossmembers, and now is being repurposed for the next generation of GM’s heavy-duty hitches. Also in 2009, the company added its first robotic resistance-welding cell. In total, the welding plant now is home to 70 robots as well as 60 hourly workers—including three welding engineers and three welding technicians—working across two shifts.
Plugging Away at Productivity and Quality
Slowly but surely, and with impressive, consistent year-over-year results, the company has plugged away at decreasing weld-cycle times, increasing quality and optimizing weld-cell uptime. All the while, it’s shifted responsibility for quality to the operators, while providing the required training to allow this shift in responsibility to occur. The firm can track every detail of every weld cell, says Sheffield, through each cell’s human-machine interface (HMI), including production and downtime, and the causes for any hiccups.
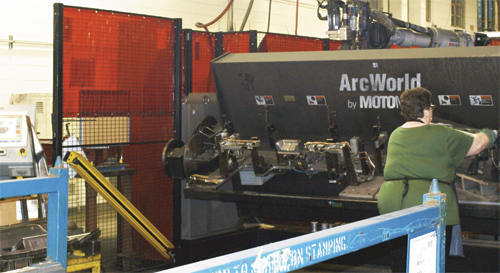 |
Northern Stamping can track every detail of every weld cell through each cell’s human-machine interface (shown here at far left), including production and downtime and the causes for any hiccups. |
“The operators’ jobs are to keep the robots moving and the cells in production,” he says. “And data collection over the company network ties everything together. Managers can see live, in real time, exactly what’s happening at every cell in the plant, and who’s responsible at any given time for meeting production goals at each cell. In addition, every assembly we produce here has an individual lot-traceability stamp on it—that’s their signature.”
Personal responsibility on the shop floor has positively impacted several measurables at the company. Most notably, weld-cell downtime throughout the facility has dropped from 28.6 percent in 2004 to 16.2 percent in 2011. Downtime is segmented, tracked and recorded by several unique causes:
• Component—out-of-tolerance parts coming to the welding cells;
• Contract—mutually agreed-to downtime, according to the union labor contract, for personal issues;
• Operator-related;
• Maintenance-related;
• Management-related—for training, scheduled meetings, etc.; and
• Awaiting component parts.
In addition, productivity has climbed significantly for some part numbers, measured as cycle-time reduction, “due to our data-collection efforts and to holding the operators to a production standard,” says Sheffield. “We also use the data to initiate process improvements.”
The Clock is Ticking, Always
Data gathering at each welding cell begins when each operator logs into their cell’s HMI each morning. Greeting each operator is a welcome screen that requires the operator to agree to this statement:
I agree that I have been trained, have read, and will comply with all standard operating procedures, operator inspection instructions and job-safety analyses for operating this cell.
Once he clicks the “yes” button, the clock begins to tick.
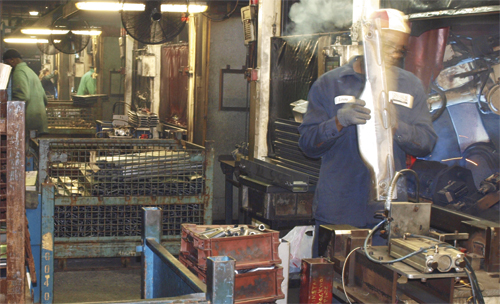 |
When an operator logs into his cell’s HMI at the beginning of each shift, he must agree to a statement reading: I agree that I have been trained, have read, and will comply with all standard operating procedures, operator inspection instructions and job-safety analyses for operating this cell. |
“They have up to 40 min. after production has started to run their first gauge check on a welded assembly,” says plant manager Jessie Meet. “Every inspection point (there may be as many as 14) is considered out of spec until the operator inspects it and turns it ‘green.’ Then and only then can an operator send a cell into full production.”
As the cells run, managers can access data collected from the plant floor and closely monitor production statistics. “These snapshots tell us the cell number, operator, part number being run, lot size, how many have already run and how many remain,” says Meet. “We can see how many assemblies have been stenciled with the operator’s identifier, and how many assemblies were rejected and why. And we can see log-in and log-out times, hours logged in and current hourly production rate compared to the agreed-upon standard.
“The key is being able to track idle hours,” Meet continues. “We can identify problems early on, learn the causes and develop solutions in a very timely manner.”
During production, the cell HMI provides alerts to the operators regarding the required inspection interval. The cell shuts down automatically and prohibits the operator from continuing to run until they perform the required gauge check. As a result of building quality into the process in this , PPM levels have dropped from a monthly high of 176 (in 2003) to a low of 3 (in 2011), where it has hovered for some time.
The last piece of data gathered at each cell, each shift, relates to safety, and has helped managers better-track recordable injuries. Before logging off at the end of their shift, operators must answer this question illuminating the HMI screen:
Did you sustain any injuries during this session of operating this cell?
A “yes” answer triggers further investigation.
Reduced Internal Scrap and Rework Rates
Operator accountability and traceability also has reduced internal scrap and rework rates. “Component parts and weldments can’t be randomly scrapped without accountability,” notes Meet, “since every part carries the operator ID. Before, raw material to finished goods was difficult if not impossible to track and control. We would struggle to identify where the material was going.”
From 2006 to 2011, scrap rate at the plant has dropped from 1.2 percent to 0.5 percent, and rework has dropped from 6 percent to 2 percent.
Tracking the causes of scrap and rework allows Sheffield and his team to identify the top scrap-producing parts and cells, and address issues in a timely manner. It also provides data to the firm’s inhouse team responsible for designing and building weld fixtures, and in some cases even has impacted the stamping-die design and build process. Northern Stamping moved weld-fixture design and build inhouse in 2007, and the investment in personnel and equipment has paid huge dividends. Meet offers examples:
”We recently took over a hitch job from a distressed supplier and when we put it into production, we were blowing out sensors in the weld fixture every other day. Our fixture department was able to quickly identify the problem and relocate the sensor to better protect it from the welding environment. Making that change via an outsourced fixture house might have taken days and impacted our production schedule.
“In another case,” Meet continues, “we were welding a clamshell stamping and our production tracking and downtime codes alerted management that welding speed was slowing and causing production levels to drop below the allowable minimum. This triggered closer inspection into the process and we noted that the weld gap in the stamping was too wide, which we attributed to stamping-die wear. Even though the parts were within tolerance, the press shop and toolroom addressed the die issues and allowed us to increase welding speed back to acceptable levels.”
Training to Fill Skill Gaps
Last but not least, the knowledge gained by Northern Stamping’s management team from its production and downtime tracking provides an up-close and personal look at any gaps between the skills and responsibilities of its employees. Filling this gap requires training, and with hard data in hand managers can tailor training to address specific problems.
“A recent example,” says Sheffield, “is in the procedures followed to change weld-gun nozzles and tips. A couple of years ago, we were noting excess downtime related to inefficient nozzle and tip changes. Operators often were manhandling the torches and moving them from their prescribed location at the end of the robotic arm. As a result, the operators would have to call in a weld tech to readjust and recalibrate the process, leading to downtime.
“Now, we provide periodic training on the proper procedure and technique for changing nozzles and tips, and what to do if they become stuck,” Sheffield continues. “Operators no longer can claim that downtime issue as equipment- and maintenance-relate. Instead, it’s now an operator-dependent downtime issue.”
Yet one more example of how personal accountability at every level pays off in the long run. MF
See also: Yaskawa America, Inc.
Technologies: Management, Pressroom Automation, Sensing/Electronics/IOT