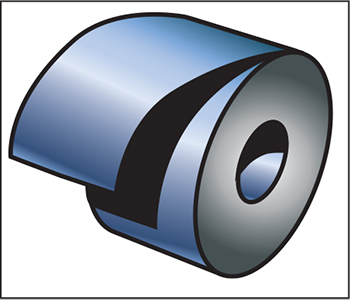 |
|
Fig. 1 | Fig. 2 |
Flatteners can satisfy the requirements for most mild-steel and some HSLA applications. The rated capacity for flattening equipment historically has been based on processing steel with yield strengths below 340 MPa (50 ksi).
Flattening AHSS grades, compared to lower-strength steels, requires larger-diameter rolls, wider roll spacing and greater horsepower. Deeper roll penetration also may be required to remove coil set from AHSS materials. The larger rolls and journals and broader center distances safeguard the flattener from potential damage caused by additional stresses.
Also, it is not reasonable to expect higher-strength materials to run through the same flattener as conventional mild steels for a given coil width and sheet thickness. For example, increasing the roll diameters and center distances on a seven-roll flattener to accommodate high-strength steels will limit the range of materials that can be effectively straightened. A straightener capable of processing 600-mm-wide coils 10-mm-thick mild steel may still successfully straighten 1.5-mm-thick material. However, a straightener sized to run the same width and thickness of higher-strength steels may only be able to straighten 2.5- to 3.0-mm-thick mild steel. This limitation is primarily due to the larger rolls and broadly spaced centers required to run AHSS materials.
Close-Center Straighteners and Levelers
Coil set occurs during coil winding, which compresses the inside surface of the material and places the outside surface in tension, causing it to stretch slightly. As a result, the inside of the sheet ends up shorter than the outside. Cross bow (Fig. 2)—when one side of the material is shorter than the other side as measured across the width of the coil—can result from the coil-slitting process.
The number of rolls in a straightening machine correlates to the number of yielding strains (bends) it can produce, which then determines the extent of possible coil correction. Close-center straighteners can have as few as nine working rolls and as many as 21. Rolls are spaced much closer together compared to flatteners, and additional supporting rollers serve as backup rolls. Close-center straighteners can induce more yielding strains than flatteners, allowing them to better-work AHSS materials and also correct cross bow.
Another coil-shape correction machine is the precision leveler, which has relatively small-diameter closely spaced rolls. Backup rollers can flex the rolls individually to allow bending of the working rolls under load. In addition to correcting surface-to-surface anomalies, levelers also can correct edge wave and center buckle.
In general, when feeding AHSS materials, straightener and leveler rollers should be smaller in diameter than those used for mild steel, to provide a smaller radius around which to bend the material. This is because AHSS must be bent more severely in order to exceed its higher yield point. To effectively yield AHSS, the straightener must be designed so that the upper rolls have adequate travel between the lower fixed rolls. This can be 50- to 60-percent greater than what is required for conventional straighteners designed for mild steels. MF
Technologies: Coil and Sheet Handling