Servo2 (Servo-Feed Line + Servo Press) Opens Windows of Opportunities
October 1, 2013 Automotive window-regulator manufacturer Hi-Lex Controls has begun to bring
metal-stamping operations inhouse, on the backs of two servo-drive presses.
Feeding its newest press: a space-saving coil-handling system that fits perfectly
into the tight confines of the plant's 5000-sq.-ft. pressroom.
The Japanese have taught us plenty about lean manufacturing and continuous improvement, and until recently I thought the term kaizen (and its definition) said all there was to say on the subject. That was until I met with Scott Sigler, when visiting the Hi-Lex Controls plant in Hudson, MI. Sigler, stamping engineer and supervisor for the automotive window-regulator manufacturer, taught this old dog a new Japanese trick in the realm of productivity and efficiency—a trick called “karakuri.”
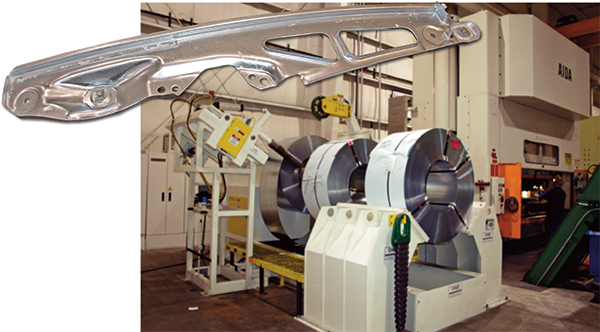 |
The CHS feed line delivers coiled galvanized steel to a 600-ton Aida servo press to stamp window-regulator rails at Hi-Lex Controls. The overall line measures a svelte 50 ft. long. |
|
In its strictest sense, karakuri refers to the use of mechanical devices to create movement. In Japanese history we learn of 18th-century puppeteers mastering the art of karakuri to entertain. Applying the karakuri principles in manufacturing, Japan-based Hi-Lex seeks opportunities to optimize movement of materials throughout its plants. Sigler shares an example:
“We run four very high-volume stamping dies on one of our presses, and the parts must be oriented in a specific to enable packaging at the end of the line. When we launched the project, operators had to manually flip the parts exiting the press before stacking them in the shipping container. Applying karakuri principles of optimizing and minimizing movement, we installed a magnet on the side of the exit conveyor. The magnet flips each part as it moves past. Eliminating this manual chore allowed us to quicken the pace of the press by 4 strokes/min.”
Also quite a study in material movement is the firm’s contortionist-like trick of fitting two coil-fed stamping-press lines into a tight 5000-sq.-ft. corner of its 240,000-sq.-ft. plant. The 2-yr.-old pressroom represents just the start of what promises to shape up as a company commitment to bringing stamping operations inhouse.
“Starting in 2008, the company committed to becoming more integrated and to bringing more processes under roof,” says Sigler. “We source millions of stampings per year from six suppliers, down from 15 suppliers just a few years ago, and our two press lines provide only about 10 percent of our needs. The plan, though, is to definitely continue to grow our inhouse stamping capabilities.”
Servo-Press Duo
The small yet productive high-bay pressroom deep within the confines of the Hi-Lex plant, and surrounded by some 20 window-regulator assembly lines, is home to two servo-drive presses—a 300-ton Komatsu installed in 2009, and a 600-ton Aida added early in 2010. The firm assembles some 48 different styles of window regulators, as well as complete door modules.
“We started small, with the 300-ton press,” says Sigler, “to stamp smaller brackets and such. And we’re completely sold on the benefits of this state-of-the-art press technology—better quality and process repeatability, higher throughput, and flexibility. We’re running about 50 dies in our pressroom now, and 40 of them run on the 300-ton press. And more than one-third of the tools feature in-die fastener insertion.”
The remaining 10 dies stamp rails—two per window regulator—and require large, complex progressive dies. A two-out tool averages 150 to 155 in. long, Sigler says, comprising as many as 18 stations. For these complex jobs the firm brought in the custom 600-ton Aida press, built with a 168-in.-long bed.
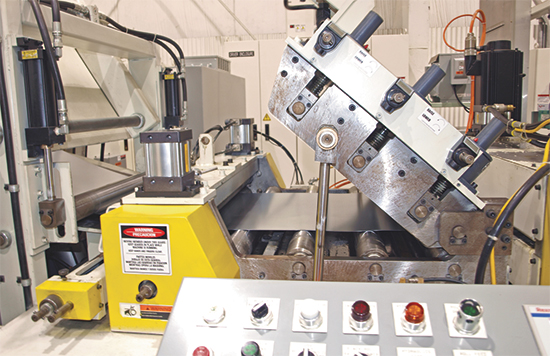 |
Switching the 600-ton press line over from stamping steel to stamping aluminum requires cleaning the rolls on the coil line’s pull-through straightener. To quicken the cleaning process, CHS developed a high-lift piloting head to ease roll cleaning. As a result, Hi-Lex can clean the feed line and get it ready for aluminum in 5 min. or less. |
Helping the pressroom squeeze the most throughput from its newest press is a new space-saving feed line, from CHS Automation, Roseville, MI.
Simplified Roll Cleaning, for the Switch from Steel to Aluminum
“One of our challenges in the pressroom is dealing with the growing popularity of aluminum window-regulator rails,” Sigler says. “Today, 70 percent of our volume is galvanized, the rest aluminum. But by mid-2014 we expect that ratio to flip. For example, one of our newest and largest programs uses aluminum rails.”
While regulator rails are not Class A cosmetic parts, surface finish is a critical parameter, to minimize noise and help ensure smooth window operation. Switching the 600-ton press line over from stamping steel to stamping aluminum requires cleaning the rolls on the coil line’s pull-through straightener. “That cleaning process can take 15 min. on a standard feeder,” Sigler says.
To avoid this unproductive downtime, Sigler worked with CHS to develop a high-lift piloting head to ease roll cleaning. “We can get the feed line cleaned and ready for aluminum in 5 min. or less,” he says.
The 20,000-lb. by 36-in.-wide CHS feed line also features a motorized coil reel and traveling load car, with 72-in. coil-OD capacity and a coil-ID expansion range of 19.5 to 24.5 in.; a free-standing peeler-threader-holddown station; and a servo-driven roll feed-straightener combination unit with 5-in.-dia. feed rolls and a feed accuracy of 0.003 in. The coil line takes direction from an Indramat controller, “which we very easily get spare parts for,” says Sigler; a Wintriss SmartPac2 Servo coordinates and directs all press-line activity.