Improving Punch Life
January 1, 2016Comments
An important requirement of any die operation is the proper alignment between all of the working components. In stamping operations, accurate alignment is necessary to maintain proper clearances between punch and die steels.
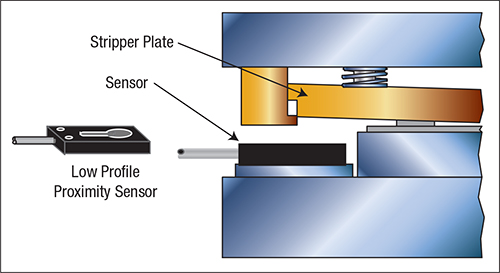
When cutting clearances are small, press and die alignment become critical. If this alignment is not maintained, the punch and die details may contact each other, damaging the cutting edges. Also, high stripping and frictional forces acting between the work materials and tooling surfaces will increase the tendency for chipping and wear.
When punches require additional chipping and wear resistance, a powder metallurgy (P/M) tool steel may be the solution. P/M tool steels have unique microstructures containing small metal carbides uniformly dispersed in the steel matrix. P/M tool-steel materials are more costly but often prove more economical due to their low wear rate.
Larger cutting clearances make press and die alignment less critical and require less cutting and stripping forces. But it is important not to the make cutting clearances too large; otherwise, excessive die roll, burrs and cracking problems may occur. Cracking results when stamping stresses exceed the tensile strength of the tooling material. Punch cracking is a greater concern with higher-strength materials due to their very high tensile strengths. The tensile strengths of some advanced high-strength materials can approach that of the tool steels working on them.