Metalforming Technology at the Core of the New F-150
April 1, 2015 While aluminum gets all of the press when it comes to Fords new F-150 pickup, there are many more firsts than meet the eye with this groundbreaking platform. Among them: a stamped 12-corner crush horn, a frame constructed of a startling 78-percent high-strength steel, and a cyclonic closed-loop aluminum scrap-segregation and recycling system.
While Ford is stamping inhouse more than 85 percent of the new F-150 by weight, it increasingly expects to rely on plenty of support from its supply chain—die designers and builders and stampers included. That according to Peter Friedman, manager of the manufacturing research department at Ford research and advanced engineering.
“Over time, as more and more aluminum makes its way into vehicles,” Friedman says, “die shops will need to develop expertise in design, engineering and feasibility analysis for working with aluminum. And, tier stampers will need to understand and adapt to the unique challenges related to aluminum—issues such as scrap segregation and closed-loop scrap control.”
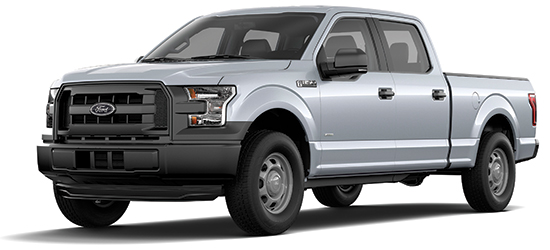 |
The aluminum-intensive 2015 Ford F-150 has been in the making for several years, including the 2009-vintage Go Fast program when Ford built four F-150 prototypes—with everything north of the frame made from aluminum. Now, Dearborn Stamping is bringing in four classes of aluminum alloys: two 5000-series alloys, differing in the amount of magnesium they contain, and two 6000-series alloys used for any exposed material. |
Those are just a few of the challenges Ford has overcome in turning over an entirely new leaf at its Dearborn, MI, stamping plant, which now has become the centerpiece of the F-150 supply chain. That facility, a premier producer throughout much of the previous century as part of Ford’s historic Rouge complex, underwent a complete overhaul that began in 2012. It’s now dedicated completely to stamping aluminum closures, body-in-white and other components for the F-150, on the backs of five new press lines, two blanking lines, two hydroforming lines and a new cut-to-length line. Supported by the Ford stamping plant in Buffalo, NY (which stamps 18 relatively small parts for the F-150, with high packing density), the Ford assembly facilities in Dearborn and in Kansas City, MO, are slated to produce 700,000 F-series trucks in 2015.
Ford is buying, says Friedman, some 1000 lb. of aluminum per truck, with a 60- to 65-percent utilization rate.
“We feel very good about that rate,” Friedman adds, “due in part to controlling trim levels, minimizing stamped blank sizes and using offal dies.”
One important note: The F-150 story is not all about aluminum. The new truck, underneath its skin, has what Ford refers to as the F-150’s strongest frame yet. Comprising 75-percent high-strength steel (20 percent is 550-MPa yield strength, and 55 percent is 340-MPa yield strength), the frame accounts for nearly 10 percent of the truck’s overall weight reduction.
Segregating, Recycling Four Alloy Classes
The aluminum-intensive F-150 is a project that’s been in the making at Ford for several years, dating back to the early 1990s when the firm assembled 20 aluminum Sables; its work with Jaguar in the late 1990s on the XJ model; and the Go Fast program in 2009 when Ford built four F-150 prototypes with “everything north of the frame made from aluminum,” says Friedman.
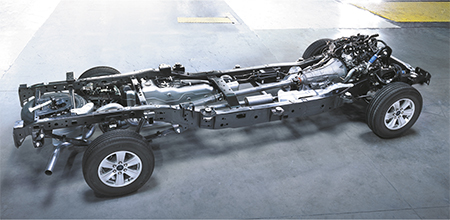 |
Any discussion of the success of the new F-150 must include its high-strength-steel frame, responsible for 60 lb. of weight reduction. There are a few ‘firsts’ with this new frame, including the use of rollformed parts and a patent-pending 12-corner stamped crush horn. |
“When we hit program-start for the 2015 F-150, we’d already experienced two levels of prototypes and were very confident in what the truck could do,” Friedman adds. “From that point on the focus shifted to manufacturing, understanding how to purchase that much aluminum as well as process it—stamp, weld, paint, etc. By 2013 the focus shifted to building the capacity and investing in the assets we needed, including new press and blanking lines and new fastening equipment—riveting, flow-drill screws, clinching and welding.”
Dearborn Stamping is bringing in four classes of aluminum alloys—two 5000-series alloys, differing in the amount of magnesium they contain; and two 6000-series alloys. “We use a low-copper 6000-series alloy for any exposed material,” Friedman says. “This is a trend throughout the industry. Compared to the once-industry-standard Type 6111 alloy, the low-copper alloys better resist filiform corrosion.”
During the extensive stamping-plant renovation, stamped-scrap handling received priority. The existing conveyor setup running to and through the plant’s basement remains in place to handle offal scrap. These relatively large pieces of scrap, say from a window cutout, serve as blanks for smaller stamped parts. However, to handle the majority of the stamped scrap in a closed-loop recycling operation, Ford commissioned an overhead cyclonic scrap-handling system.
“We’ve installed four separate scrap-conveying lines—one per alloy type—that pull scrap up from the dies and into chutes,” Friedman explains. “They convey the scrap out of the building to four awaiting trucks. Again, one truck per alloy.”
Sliver Management
Ford is stamping aluminum 0.85 to 3.8 mm thick, “much thicker than any aluminum we’ve stamped before,” says Friedman. Several parts on the F-150 have been up-gauged from their steel counterparts, including the cargo-box floor (from 0.85-mm bake-hardened steel to 1.4-mm aluminum, and the doors (from 0.9-mm steel to 1.2-mm aluminum).
While keeping his cards close to his chest, Friedman does point to a few areas of metalforming technology critical to the success of its aluminum acumen. These include sliver management in trim dies, “important as we’ve gotten into thicker aluminum sections,” he says; springback prediction and management; and investigating lubricants geared toward enhancing the formability of aluminum.
On the first front—solving the sliver issue—Ford is focused on methods for supporting scrap. “During development of our previous aluminum platforms,” Friedman says, “we learned plenty about how to support scrap to minimize slivers. It’s been a long and continuous journey, but it’s critical to minimizing die maintenance when stamping aluminum.”
In the area of die design and springback modeling and compensation, “we’ve gotten much better at developing good dies right out of the gate,” Friedman says, noting its use of AutoForm and LS Dyna.
Last but not least, Friedman heaps praise on a new stamping lubricant it’s using. “We’re no longer using conventional oil-based lubricants common to the steel industry,” he says, noting the growing need for deep-draw tight-radii forms with tightly controlled dimensions.
“We’ve switched to a hot-melt lube with a very low coefficient of friction for all of our aluminum stamping,” Friedman shares. “It performs very well under high hydrostatic loads, and greatly enhances our ability to draw aluminum.”