High Uptime, Flexibility
The resulting production line processes blanks as thick as 5 mm and as large as 6.6 by 2 m. The line operates around the clock, six days a week. With only 20 days per year planned for maintenance and servicing of the robotic press-brake line, high equipment availability is essential. Offline programming of the robots helps here, as programming is uncoupled from manufacturing so that the robots can continue feeding the press brake in production while programmers develop new programs.
“Our requirements for the robots go beyond this, however,” says Langer. “One precondition for the production of the box panels is an angular and dimensional accuracy of up to 0.1 mm relative to the entire workpiece. Further, we require a cycle time of 8.5 min. to achieve the planned annual quantity of 400,000 sq. m of plate.
“The robots also must be very flexible,” continues Langer, “due to the varying lengths and widths of the finished panels.”
The KR 500 robots can be operated independently of the other machines in the overall system. This fact can be exploited for contract work. 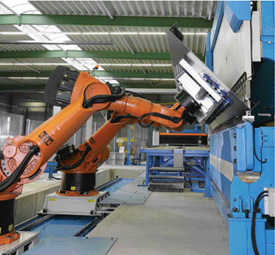 |
Each of the four edges of the blank takes a two-step bend to 90 deg. Robot motion corresponds to the downward motion of the press-brake ram—when the ram reaches its lowest position, the robots also reach the end point of their motion paths. |
Versatile Grippers
To begin production of a box panel, a gantry crane loads a coil of steel onto a coil lift truck at the head of the automated production line. This truck, running on a track, transfers steel strip weighing as much as 30 tons to an uncoiler. The strip is then processed by a straightening unit, and a laser system cuts holes, corner indentations for the folds, apertures for supply lines and other order-specific openings in the steel plate.
A roller conveyor then delivers the prepared plates to the two six-axis material-handling robots. Each plate is first positioned against a stop and then pushed into a defined position by pneumatic cylinders. Sensors monitor the process and if plate dimensions change, an operator enters the new values into the computer.
The robots generally grip all plates centrally. In the case of very wide workpieces, however, the operators can program an eccentric pickup position.
The two robots traverse a common linear unit to pick up a plate with their suction-cup grippers, mounted on end-of-arm fixtures that measure 2.6 m long by 1 m wide. The end effectors developed for this application each carry six different suction-cup modules; depending on the task, the system operator activates, via the controller, the appropriate gripper modules.
Complex, Counter-Directional Motions
It takes two robots to handle the plates, otherwise, the plates would sag. Langer, pointing to the robots as they rotate a plate in order to hold it in a defined position against the backgauges of the press brake, says, “Just take a look at these complex, counter-directional motions. They clearly show that cooperating robots were the only possible solution for this application.”
Each of the four edges of the blank takes a two-step bend to 90 deg. Robot motion corresponds to the downward motion of the press-brake ram—when the ram reaches its lowest position, the robots also reach the end point of their motion paths. After each bend, the robots set the plate down on a turntable, which rotates the plate through 90 or 180 deg. The setdown and pickup position on the turntable is programmed.
Upon completion of the bending process, the robots set the steel box panel down on a support, where a roller conveyor transports it for welding. MF
Information for this article supplied by Kuka Robotics Corp., Clinton Township, MI; 866/873-5852; www.kukarobotics.com.
See also: KUKA Robotics Corp.
Technologies: Pressroom Automation