PLC Progress Simplifies Debugging
Tom Sipple, material handling technology leader at robot and robotic system supplier Motoman Inc., West Carrolton, OH, also notes the advantages delivered by the newer state-of-the-art PLCs employed by automation-system providers. These PLCs, he says, combine the safety and cell control logic in one rack.
“In the past,” Sipple says, “automation systems had a safety PLC to handle gate interlocks, light curtains and other safeguarding devices, and the data from that PLC would be routed to the cell-control PLC to notify the operator of the system status. Today, we combine all of this logic into one PLC. This vastly improves debugging time.”
One technology enhancement credited with improving the flexibility of press-automation systems is dubbed by robotics suppliers “payload identification.” Payload ID allows the robot programmer to input to the material-handling robot how heavy the payload is —the weight of the end-of-arm tooling plus the weight of the blank or part.
“In the past, a 100-kg-capacity robot als performed like a 100-kg robot,” says Peter Stephan, program manager —stamping for Fanuc Robotics America, Inc., Rochester Hills, MI. “With payload ID, the robots can be programmed for each specific job at hand, with its motors set accordingly for the required torque and momentum based on actual loading conditions. The result is optimized motion profiles and, ultimately, increased throughput.”
The Right Robot for the Job
Stephan also points out that in the early days of integrating robots with stamping presses (“robotic automation made big inroads into pressrooms in the early to mid-1990s,” he says) all of those initial installations had system integrators placing material-handling gripper tooling onto the ends of robots designed primarily for spot welding. While spot-welding robots are tuned to perform a series of short start and stop moves and thus require high acceleration and deceleration capabilities, press-tending robots must perform with a completely different type of motion profile. Robot vendors in recent years have worked hard to develop product lines to accomplish this—they now offer application-specific robots with motors and software tuned specifically for pressroom service.
“Material handling, including press tending, requires longer moves, where the robot has to be at top speed for a longer period of time compared to spot welding,” Stephan notes. Echoing Stephan’s comments, Sipple adds that “today’s high-speed high-duty material-handling robots, when combined with load-sensing technology, can yield a 15- to 20-percent increase in productivity compared to the robots installed in the ’90s. Many customers—from the OEM level down through Tier Two suppliers in the automotive and appliance industries—are actively replacing original press-tending systems with the new generation of robots designed specifically for high-duty-cycle use. ”
Sipple also points out the advantages to metalformers of using coordinated motion among multiple robots, working together to feed large or otherwise clumsy blanks. Coordinated motion—the ability of a controller to precisely track the movement of multiple robots in a cell—long has been used in robotic-welding applications, “and is growing in acceptance for material-handling applications, such as press tending,” Sipple says. He notes a trend toward automating the stamping of automotive frame rails—large, heavy parts—where a pair of robots relying on coordinated-motion controls each grab one end of the rail blank and load and unload a press.
Vision Overcomes Sloppy Stacking
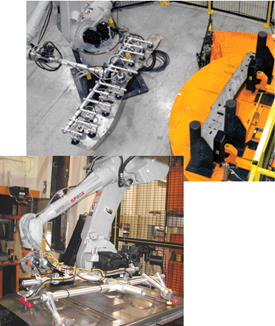 |
180-deg. rotating fixture table to feed a press. At left: A five-axis Motoman robot tends to a press at an appliance manufacturer. |
Also driving the growth of press-tending automation sales is the growing acceptance of vision systems on press lines, at the entry end as well as the exit end. “The use of vision coupled with robotics is becoming very popular,” says Stephan. “A vision system coupled directly to the robot controller allows the orientation of the blank or part to be determined as the robot carries it from the stack to the first die station.”
Vision systems allow stampers to overcome the biggest hurdle to successful use of automation at the front end of a press line—stack sloppiness. Without vision, it’s critical that blanks be neatly packaged for delivery to the press line, and that bands and covers are easily removed. This process typically has been the limiting factor to stamping shops successfully integrating automation. Now, for those applications where blanks are not so neatly stacked, the stamper can position one or more cameras between the destacker or press-tending robot and the first die operation. “Then we make sure that as the robot moves the blank toward the press, some portion of the blank passes within the field of view of the camera.”
Stephan describes one recent vision-system retrofit project at a Tier One stamper that yielded a 25-percent increase in throughput. “Previously, they needed to station an operator near the press to manipulate misloaded blanks, which had been fed with a robot since 1996,” says Stephan. “Operators often had to jostle the blanks down into the die using a handtool. Now the vision system processes the slight adjustments in blank orientation as it moves toward the die so that every blank sits quickly and properly in the die. They have since increased production by 100 strokes/hr.”
An alternative to a vision system in this application would have been a blank-alignment system, which, Stephan says, is fine for some applications where part runs are relatively long. But in this particular case, where the Tier One supplier must produce a wide variety of parts on one tandem line, the additional time needed to reset the alignment system with every die change proved an unattractive option. “Once we teach the vision system to identify the blank and its proper orientation,” he says, “it becomes part of the overall production routine, so there’s no added setup time.”
Motoman’s Sipple also notes increased interest in end-of-line automation, where the use of vision systems has a history of success. “We’ve found that for racking of parts as they leave the press, as long as the racks stay in the same facility and, therefore, typically do not get damaged, we can robotically rack parts at the end of press lines without the use of vision. But, plants that ship their racks outside of the facility need to qualify the returned racks using a mechanical checking method or a vision system to ensure they can still be automatically loaded.”
Early ROI
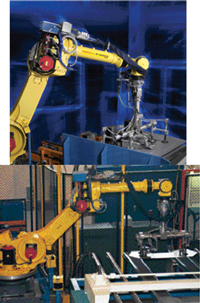 |
Neat blank stacks allow these Fanuc robots to cleanly destack blanks and load them into the first die station of a press. Where stacks are not so neat, stampers employ vision systems to view the blank as it is carriers by the robot and signal any necessary adjustments in blank orientation to ensure that the blank sits quickly and properly in the die. |
Besides high-volume applications, where sheer numbers often make for relatively quick return-on-investment periods of 12 to 24 months, other common applications allowing stampers to easily justify automation are surface-finish-critical jobs, such as stainless-steel parts and others common in the appliance industry. AP&T’s Mattson describes his firm’s new modular blank feeder and destacker as perfect for this type of work, since it employs a pneumatic gripper, rather than a conveyor, to transfer blanks through a lubrication station and then center the blanks after lubrication. “There’s no surface contact,” he says, “and production capacity is increased by 50 percent.”
The ability to run more quickly, as well as tackle finish-critical applications, has some European metalforming companies investing in press automation in order to win back some of the contract work that had gone offshore to low-cost countries a few years ago, says Mattson. “We’re seeing an increase in automation of new lines as well as retrofits to existing press lines,” he notes. “Customers are automating to increase capacity rather than adding new building space and new presses, and at the same time reducing labor input. Our typical retrofit application yields a 30-percent increase in throughput.”
“Provided that metal stampers have reliable presses and well-maintained feed lines and other auxiliary equipment, the benefits of press automation can readily be realized,” says Sipple. “But if a line is not dependable, the stamper that employs automation will make a few parts really quickly, and then have to stop the line to fix something. But of all of the robotic applications we work on, in terms of benefits and return on investment, press tending offers one of the highest rates of return.
“Make sure that your company has established a culture that allows the benefits of automation to be fully realized including neat blank stacks, preventive maintenance and operator training,” concludes Sipple. MF
Industry-Related Terms: Blank,
Case,
Center,
Die,
Fixture,
Lines,
Model,
NC,
Run,
Surface,
Torque,
TransferView Glossary of Metalforming Terms
See also: AP&T North America Inc., Yaskawa America, Inc., FANUC America, Inc.
Technologies: Pressroom Automation