“Whether aiming to increase throughput, reduce setup times or enhance product quality,” Diaz says, “this presentation offers actionable insights tailored to boost manufacturing capabilities.”
Next on the agenda is a presentation from Larson Tool & Stamping Co. describing how it has optimized its use of servo presses for deep drawing 17-7 PH precipitation-hardened stainless steel.
“This presentation is a case study that explores the advantages of utilizing servo press technology for deep drawing components from 17-7 PH,” shares presenter Manny Resendes, engineering/toolroom manager at Larson. “Attendees will gain real-world insight into the precise control and programmable motion profiles offered by servo presses, which enhance process flexibility, reduce quality burden and improve overall run quality at high volumes.”
Rounding out the day-one agenda, and staying on the servo press theme, is Bob Gunst, president of Jacar Systems, with his presentation, Servo Press and In-Die Transfer Technology.
“Servo presses and in-die transfer are new and exciting technologies emerging in the sheet metal-stamping industry,” says Gunst. “In this session attendees will learn how to combine these two technologies to optimize project outcomes. Participants also will see examples of different servo applications using in-die transfer tools, learn valuable press-stroke and transfer-motion tips and tricks, and take away several case-study illustrations.”
GE Appliances’ Digital Supply Chain
The morning of Wednesday, January 29, welcomes to the stage the second keynoter: John Panozzo, senior advanced engineer, GE Appliances (GEA). He’ll describe the firm’s new zero-distance formability/feasibility process. Explains Panozzo:
“GEA has undergone sweeping internal transformation since 2016, driven by a ‘zero-distance’ strategy: zero distance between what the company makes and what its customers want; between ideas and innovation; and between where products are developed and made. Toward that end, GEA has transformed its business model toward a seamless and digital supply chain—internally and externally.”
Morning sessions wrap up with venerable presenter and knowledge expert Jim Finnerty for a talk on die protection. Describing his presentation, 50 Tips for Better Die Protection, Finnerty notes:
“There is a lot more to die protection than installing a few sensors into the die and programming the control. There are press and ancillary-equipment considerations, environmental issues, and even personnel concerns that must be addressed to ensure success. It was thought that many of these factors had to be ‘caught, not taught.’ That’s about to change.”
Finnerty’s presentation will provide useful insights into the intricacies of all areas of die protection and help metal formers deal with important yet difficult-to-foresee application challenges that might arise during implementation and in day-to-day operations.
Spotlight on Workforce Development
Launching into the afternoon sessions is MetalForming magazine columnist Art Hedrick—author of the Science of Forming column—who turns attendee attention to workforce development. Regarding training the next generation of stamping workforce, Hedrick says:
“It’s no secret that there has been a loss of very talented individuals working in the sheet metal stamping industry. Unfortunately trying to replace years and years of experience is difficult. For this reason, we need to quickly expedite the training and education of the newer younger workforce.
“Far too often, poor or incorrect decisions are made regarding the troubleshooting or maintenance methods utilized to keep or solve die or part failures,” Hedrick continues. “These decisions are often made because of a few reasons including: ‘That’s the way we were taught to do it,’ or ‘Because it worked last time,’ or ‘That’s how we have always done it here.’ Many of the decisions made are the result of tribal knowledge rather than a clear understating of the physics supporting the decision. This session will provide attendees with solutions for turning ‘greenhorns’ into seasoned veterans in the shortest time possible.”
Last but not least, PMA director of technical training Dean Phillips will detail a stamping-optimization process he dubs “SAUCE,” an acronym that stands for safety, automation, utilization, comparison and education.
“This process, designed to deliver concrete executable ideas to improve production in the press shop,” Phillips explains, “will deliver instant results in any plant, regardless of size or stamping operation. These tangible, proven concepts will bring your team ideas on how to fully optimize your facility’s operation. This presentation is valuable to leaders, die setters, tool and die personnel, operators, and engineers.”
Please make plans now to join PMA and MetalForming in Nashville. Learn more and register to attend. MF
View Glossary of Metalforming Terms
See also: Wintriss Controls Group LLC, Nidec Press & Automation, Precision Metalforming Association, Dieology LLC, Wipfli LLP
Technologies: Management
Comments
Must be logged in to post a comment. Sign in or Create an Account
There are no comments posted.Driving Profitability with Strategy, Data and People, Laurie...
Tuesday, July 8, 2025
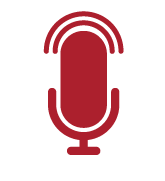