These are:
- Properties of each chemical;
- Physical, health and environmental hazards;
- Safety precautions for handling, storing and transporting the chemical.
The 16 sections of an SDS:
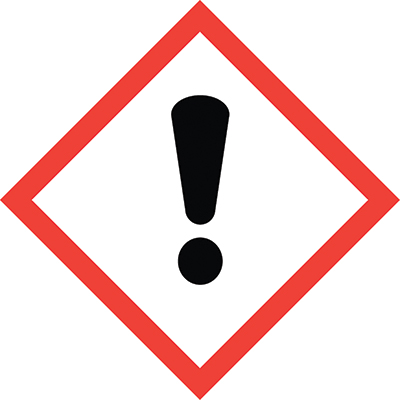 |
An exclamation point indicates lubricants and other chemicals that include irritants (skin and eye), skin sensitizers, acute toxicity agents (harmful), narcotic effects, respiratory-tract irritants, or are hazardous to the ozone layer. |
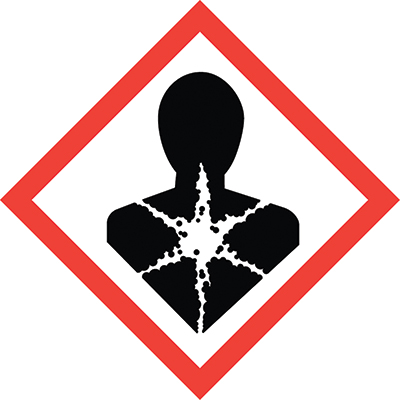 |
The exploding-heart pictogram on packaging indicates health hazards such as chemicals that may be carcinogenic, cause mutagenicity and/or reproductive toxicity, are respiratory sensitizers, or cause target organ toxicity and/or aspiration toxicity. |
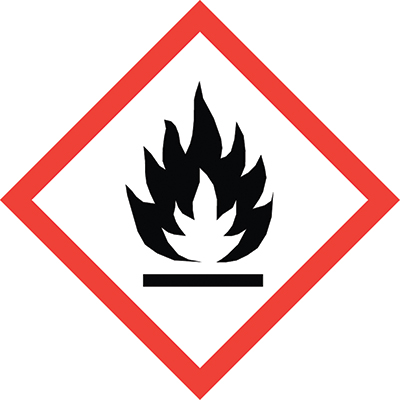
|
Chemicals that are flammable, self-heating or self-reactive, or organic peroxides, are identified with this flame pictogram. |
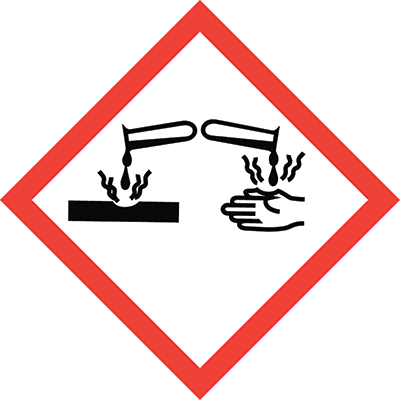
|
The corrosion pictogram identifies chemicals that may cause skin corrosion or burns, eye damage, or are corrosive to metals. |
1) Chemical identification—Essential information on the supplier/manufacturer
2) Hazard identification—Any hazards the chemical presents and appropriate warning information
3)Composition/information on ingredients—Information on the substances, mixtures and chemicals used
4) First-aid measures—Care to be administered to those exposed to the chemical
5) Firefighting measures—Handling a fire with the chemical
6) Accidental release measures—Response to spills, leaks or release
7) Handling and storage—Guidelines on safe handling practices and storage
8) Exposure control/personal protection—Minimizing worker exposure and limits
9) Physical and chemical properties—Important key properties of the material
10) Stability and reactivity—Reactivity hazards of the chemical, if any
11) Toxicological information—Health-effects information
12) Ecological information—How to evaluate environmental impact if released
13) Disposal considerations—Guidance on proper disposal, recycling and reclamation of the chemical or its container
14) Transport information—Classification for shipping and transport of hazardous chemicals
15) Regulatory information—Safety, health and environmental regulations not indicated elsewhere on the SDS
16) Other information—Date of preparation or revision and other useful information.
Targeted: Hazard Identification (via Pictograms)
While all sections of the SDS are important to understand, the one that is new for the GHS SDS format is Section 2—Hazard Identification. The use of the previously required Hazardous Materials Identification System (HMIS) has been replaced by GHS hazard classification, signal words, and pictograms.
The GHS does not require the use of HMIS ratings, which ranked chemical from 0 (safe) to 4 (most hazardous). That system conflicted with other ranking systems used internationally, where a 4 rating represented a safe chemical and a 0 rating indicated a chemical as hazardous. While some chemical manufacturers still include this information in their SDS, it can be confusing to use both systems.
OSHA now requires an understanding of the GHS hazard-classification system by all personnel in contact with workplace chemicals. Manufacturers and suppliers should educate users so that they understand the new GHS system. The nine pictograms OSHA has adopted, which find use worldwide, aim to improve worker knowledge, safety and health. Note—most metalformers will use only four of these pictograms:
- Exclamation point—Irritants (skin and eye), skin sensitizers, acute toxicity agents (harmful), have narcotic effects, respiratory-tract irritants, or are hazardous to the ozone layer.
- Exploding heart—Health hazards, such as chemicals that may be carcinogenic, cause mutagenicity and/or reproductive toxicity, are respiratory sensitizers, or cause target organ toxicity and/or aspiration toxicity.
- Flame—Chemicals that are flammable, self-heating or self- reactive, or organic peroxides.
- Corrosion pictograms —Chemicals that may cause skin corrosion or burns, eye damage, or are corrosive to metals.
Signal Words, Too
Along with the pictograms, warning labels will include an accompanying signal word—“Warning” for less severe hazards, or “Danger” for the more severe hazards. The intent is to alert the user to potential hazards listed on the label, and the severity of the hazard.
Metalforming-plant personnel, by reviewing the pictograms and signal words accompanying their lubricant packages, then can review the appropriate hazard and precautionary statements, which detail the nature of the chemical’s hazards. “May cause an allergic skin reaction” is a frequently used example.
A detailed understanding of all four parts of a chemical’s SDS is key to ensuring worker safety and proper use of the chemical. For a more detailed explanation, review the chemical’s full SDS. A good source for additional information is the online OHSA Briefs: www.osha.gov/Publications/ OSHA3514.html.
Changes in Lubricant Composition
Through the years, lubricant suppliers have continued to innovate, using newly developed additives for a variety of purposes, including to enhance worker safety. Among the thousands of additives available to lubricant manufacturers, many are safe to use while others may require warning labels on the lubricant packaging. If some of the chemicals in your plant have such warning labels, find out why. Also be sure to understand usage restraints, methods or means of overexposure, and how to minimize these risks with proper use and controls. Consult with your lubricant supplier as to the warnings or dangers related to their products—there may be alternative products that are safer to use while still performing the needed functions.
There are many “tried and true” lubricants that have been used for many years. And, additive technology has evolved in recent years, as have health and safety standards and classification systems. With the pace of innovation and change within the lubricant industry, if you have been performing operations or tasks the same way for the last several years, chances are there are better ways.
Years ago, petroleum-based soluble oils were the norm in stamping plants. While performance in the tooling was excellent, some negative downstream effects resulted. For example, oily parts often were sent to welding operations, which created smoke and poor weld quality. And, increased cleaning costs associated with soluble oils, as well as part quality, could increase post-processing costs.
With the introduction of modern synthetic forming lubricants, parts can move directly from stamping to welding, creating better weld quality, minimal to no smoke and a safer environment for operators. Additionally, with synthetic technology, parts are easier to clean and do not require as much heat or chemicals to process, reducing overall operation costs.
Solvent-Based vs. Green Lubricants
Solvent-based lubricants are used to produce clean, dry parts after stamping. The typical lubricant carrier is a petroleum distillate, such as mineral spirits, naphtha or similar petroleum derivatives. A variety of lubricity additives are blended with the carrier to develop the lubricant. The hazard and health warnings placed on these lubricants can be a bit scary, especially when labeled with an exclamation-point pictogram (skin and eye irritant), a health-hazard pictogram (for aspiration and inhalation hazards) or a flammable-liquid pictogram (for flash point and fire hazards). While many of the warnings and hazards are for overexposure, stampers should consider the alternatives available that may suit their needs and be safer for workers and the environment. For example, green-fluid technology offers a variety of advantages over existing products in this category. These lubricants offer safe, environmentally responsible solutions that often can replace solvent-based lubricants.
For this new lubricant-labeling system to be effective, all U.S. employers and employees using chemicals in the workplace must become familiar with and understand its pictograms and signal words. Read the hazard and precautionary statements of all of the chemicals used in your facilities. Additionally, employers and employees no longer should accept dangerous chemical products from their suppliers. There are safer alternatives available.
All chemical suppliers should strive to use the safest ingredients possible when developing their products for the metalforming industry. In a perfect world, all chemical suppliers would have the goal of creating safer products that require zero pictograms. The metalforming industry deserves this effort. MF
See also: Tower Metalworking Fluids
Technologies: Lubrication, Safety