Fabricators can use cylinder gases such as nitrogen or nitrogen-hydrogen (95 N2 – 5 H2) with some single-gas torch systems in an effort to improve the cut-surface quality of nonferrous metals. However, the required total flow rate for a 125-A single-gas plasma torch, as much as 550 ft.3/hr., increases gas costs because a cylinder with a 330-ft.3 capacity empties in 36 min.
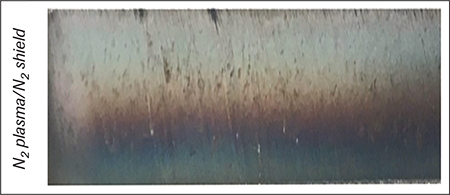
|
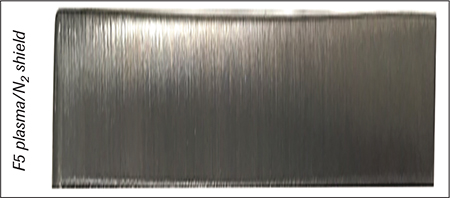
|
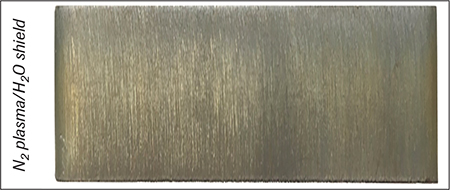
|
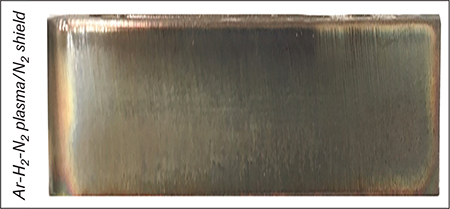
|
Fig. 4-7—Images show representative results of cutting stainless steel from the gas combinations listed. |
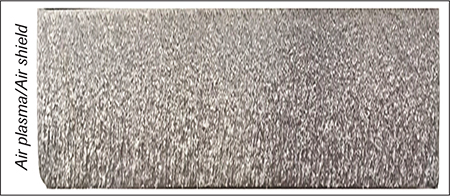
|
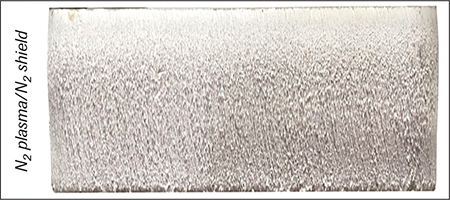
|
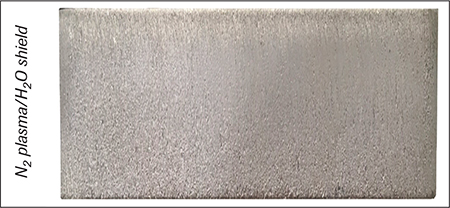
|
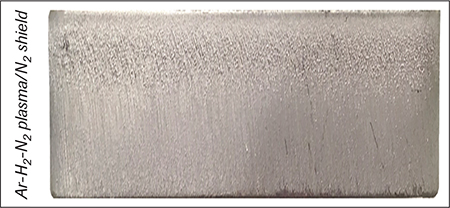
|
Fig. 8-11—Images show representative results of cutting aluminum from the gas combinations listed. |
Plasma systems configured with single-gas torches offer significantly shorter consumable life and much higher operating cost than plasma systems configured with liquid-cooled, dual-gas torches. Air-plasma systems do not include long-life technology, which ramps amperage and gas flow up and down at the start and stop of every cut, ensuring consistent cutting performance over the life of the consumables. Without such technology, cut quality changes dramatically over the life of a consumable set.
Dual-Gas Systems
Today’s automated precision plasma cutting systems are configured with liquid-cooled, dual-gas torches; computer-controlled, switch-mode power supplies; and sophisticated automatic gas-delivery systems. Cut charts embedded into CNC controls automatically adjust cutting parameters and select the required gases based on the material type and thickness selected. Also, most systems include technology that adjusts amperage and gas flow at the start and stop of every cut. This technology significantly extends consumable life and ensures consistent cutting performance over the life of consumable.
The type of workpiece material and its thickness, and the cut-face weldability required determine recommended gas combinations. To deliver premium cutting performance, manufacturers of automated plasma systems make large investments in developing consumable sets designed to operate at exact amperages using specific gas combinations.
Businesses seeking contract plate-cutting opportunities will find that the vast majority of competing contract shops operate plasma-cutting machines configured with precision high-definition plasma systems. Shops pursuing contract plasma cutting also will be competing with the laser- and waterjet-cutting processes. Today’s contract cutting firms offering plasma cutting must consistently deliver accurately cut parts on time, at competitive prices, with minimal bevel, little or no dross, and weldable cut edges.
Gas Combinations for Mild Steel
All manufacturers design their automated precision plasma-cutting systems to use oxygen as the plasma gas for cutting steel. Oxygen plasma produces the best cut quality, least amount of dross, fastest cutting speed, most weldable edge and most forgiving parameter settings. At 30 and 50 A, most precision automated plasma-cutting systems use oxygen plasma and oxygen shield. Shop compressed air is used as the shield gas above 50 A.
Plasma, laser and oxyfuel cutting processes use oxygen when cutting steel, and they leave a thin film of iron oxide on the cut surface. This thin film can be removed easily with an abrasive treatment. However, if not removed, paint applied to the cut surface may flake off (Fig. 2-3).
Gas Combinations for Stainless Steel
For general-purpose cutting, most manufacturers of automated precision plasma systems suggest cutting stainless from thin-gauge to 1.5-in. thick, using either shop compressed air or nitrogen plasma, with either nitrogen or shop compressed air as the shield gas. The cut should be free of top and bottom dross, have a relatively smooth cut surface and minimal bevel. Weld metal applied directly to the cut face requires surface grinding.
If weld metal will be applied directly to the cut surfaces from thin gauge to 0.5-in. thick, consider gases such as F5 (95 N2 – 5 H2) plasma and N2 shield to produce weldable cuts. Some plasma systems include a gas-delivery system with the ability to blend argon, hydrogen and nitrogen for customized plasma-gas mixtures based on thickness and cutting amperage. For plates from 0.5 to 1.5 in., Ar-H2-N2 blended plasma-gas mixtures with N2 shield produce premium results—smooth, squared edges, often with a golden color. A few manufacturers offer the ability to use nitrogen plasma and tap water as the shield. The N2/water process produces a very square and weldable edge at a low cost for thin-gauge to 1.5-in.-thick plate.
Note that gas combinations such as F5 plasma/N2 shield and Ar-H2-N2 plasma/N2 shield require a narrow window of parameters (speed and voltage) to produce premium results. Some adjustment to cutting speed and voltage may be required to optimize cuts (Fig. 4-7).
Gas Combinations for Aluminum
For general-purpose cutting, most manufacturers of automated precision-plasma-cutting systems suggest cutting aluminum from thin-gauge to 1.5-in. thick, using either shop compressed air or nitrogen plasma, with nitrogen or shop compressed air as the shield gas. The cut should be free of top and bottom dross, and have a relatively smooth cut surface with minimal bevel. However, the cut face will be heavily oxidized, rough and grainy. Grinding will be required if weld metal is applied directly to the cut face surface.
Blends of argon, hydrogen, and nitrogen plasma and nitrogen shield that deliver premium results should be considered if weld metal will be applied directly to the cut surfaces of aluminum from 0.25- to 1.5-in. thick. Edges cut with these combinations are quite smooth, very square and weldable. A few manufacturers also offer the ability to use nitrogen plasma and tap water as the shield. The N2/water process produces a very square and weldable edge at a low cost, from thin-gauge to 1.0-in.-thick plate (Fig. 8-11). MF
Industry-Related Terms: Abrasive,
CNC (Computer Numerical Control),
Color,
Edge,
Gauge,
Surface,
Thickness,
Weldability,
Grinding,
LASER,
Nitriding,
Plate,
Stainless SteelView Glossary of Metalforming Terms Technologies: Cutting