Want to run faster? That’s where gantry setups shine. “These simple two-axis gantry motion systems can allow a transfer press to top out at 30 strokes/min. or more,” Stirrett says, noting that instead of a vision system to orient the blanks coming from the stack, “we either ensure that the blank stack is set up as required on the handling system, or use vision and other dedicated equipment to identify and adjust each blank to present it to the transfer tooling. These setups include a physical mechanism able to stop the blank as it feeds on a conveyor and crowd it into position using a series of independently adjustable pins.”
Gantry setups, often custom developed for the application, are T-style (with blanks moving from stacks perpendicular to the feed direction, then turning 90 deg. to feed into the press) or inline. They use an overhead pick-and-place mechanism to move blanks from one or two stacks onto a shuttle, an infeed conveyor, or idle nest system for delivery to the press. One feed head serving one blank stack can feed at stroke rates in the mid-20s, Stirrett says, and faster by adding a second feed head.
When do metal formers opt for vision-guided robotics to feed blanks vs gantry systems? “Robots often are commodities, especially for larger OEM and Tier One stampers,” Stirrett says, “and come in at a lower cost than a custom-engineered gantry setup. And, the cost of vision systems has dropped as well, becoming very cost competitive. There even are cases where we propose the use of vision systems with gantry systems.
“When we know an application will include a destacker,” Stirrett continues, “we look at the geometry around the press—do we have enough room for robotics, because these setups can take up considerably more floor space than a gantry system. We also look at what the customer is most familiar with—if a company has a lot of experience with robotics, such as the OEMs, we tend to stick with that approach. But we also look at speed, and again this is where a custom-engineered gantry setup shines; we can dial these up, based, of course, on press capacity. If the press can only run a job at 16 strokes/min., robotics will suffice, and a gantry will be overkill.”
Blank Feeding 2.0
Asked to comment on what’s new regarding destacking and blank-feed technology, Stirrett turns to the 2.0 version of destackers: the use of servo drives. With an eye to the retrofit market, Stirrett sees huge opportunities for metal formers to implement servo technology and upgrade existing equipment, for a fraction of the cost of all-new destacking and blank-feeding systems.
“A stamper might have a 20-yr.-old blank-feed line where the actuators have become shaky over time, having developed mechanical slop,” he says. “There’s often no need to replace the entire system, just those components becoming problematic, which can cause the feed system to more or less throw the blanks into the die rather than gently and accurately place them. This can cause the stamper to reduce run rate, in some cases to less than 10 strokes/min., to ensure precise part positioning. Replacing the pneumatic and mechanical elements with servo actuators allows stampers to return their press lines to speeds closer to 20 to 25 strokes/min.”
Speed and productivity gains also come from feeding a press line from two blank stacks rather than one, using two destacking heads. While lines fed with one head typically top out at stroke rates in the mid 20s, Stirrett says, two heads and two blank stacks can push production to as high as 30-plus strokes/min.
“With two stacks and two heads,” he explains, “the heads deplete one stack in a precisely programmed motion profile to maximize feed rate without causing interference or, potentially, a collision. When they empty one stack, the heads then can begin feeding from the second blank stack while the empty stack is refilled, so that the press never stops. With only one blank stack, the press must stop and wait for a new blank stack to replace the empty one.”
Double Blanks Need a Home
A key component of every blank-feed setup is a place to drop a double blank, should one be detected. “When using an inline blank-feed system, we typically design the pick-and-place device long enough so that it can retract backward if needed, as well as forward,” Stirrett explains, “so that it can deposit the rejected blank into a reject station. Or we can deposit the extra blank into a station located between the blank stacks and the idle nest.
“When using a pass-through noncontact sensor to detect double blanks,” he continues, “we’re usually moving blanks on a conveyor. Here, to deposit the extra blank we either can reverse-index to drop the extra blank, or the conveyor will stop and an operator manually removes the blank. And, we always recommend that stampers equip their blank-pickup station on the transfer rails with a gripper that can detect double blanks.”
What About Tailor-Welded Blanks?
Finally, how can stampers handle stacks of tailor-welded blanks that inevitably become tilted, sometimes by a great deal?
“In these cases, we divide the pallet into four separately controlled quadrants,” Stirrett explains, “and use servo-driven height adjustments in each quadrant to level the stack. This ensures that the top of the stack remains flat for the feeder mechanism. And, we can program the servos at different locations in the stack, necessary because as the stack diminishes there’s less tilt, and the servos ensure that the overall stack height levels out.”
These systems are in place to guarantee that double blanks are not fed into the transfer process.
“These can be challenging applications,” Stirret concludes. “Another option is to add dimples or other features to the blanks to keep the stack level as it grows. While this approach avoids the added cost of a servo-controlled adjustable blank-stack lift system, it will reduce the number of blanks that will fit onto the stack.” MF
View Glossary of Metalforming Terms
See also: Linear Transfer Automation Inc.
Technologies: Coil and Sheet Handling
Comments
Must be logged in to post a comment. Sign in or Create an Account
There are no comments posted.Amada Press Systems Debuts Feeder Line on One Controller at ...
November 1, 2024
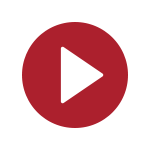
Feed-Release Timing—What Every Press Technician Should Know
Peter Ulintz September 20, 2024