3D Metal Printing of Automotive Stamping Dies
May 1, 2016Comments
Studying wire-arc additive manufacturing of draw dies for three automotive parts reveals how additive manufacturing may play a role in the metalforming arena.
In a project for the Advanced Research Projects Agency—Energy (ARPA-E), conducted during the first nine months of 2015, Ricardo, Inc. partnered with United Technologies Research Center (UTRC) to develop a detailed cost model for 10 key automotive components (chassis, powertrain, controls, etc.). The project, titled Reducing Automotive CAPEX Entry Barriers through Design, Manufacturing and Materials, analyzed the investment barriers for lower-volume production. Amongst various findings were opportunities to use 3D printing to reduce the necessary investment in tooling.
No Secret: Tooling Can be an Investment Barrier
![]() |
Leveraging its manufacturing expertise and newly developed manufacturing cost model, the Ricardo team studied capital costs associated with the conventional manufacturing of 10 subassemblies from the Toyota Corolla. |
Passenger vehicles and commercial trucks incorporate several metal components in the body-in-white, closures and other areas of the vehicle, often requiring enormous capital investment in tooling. The cost of a die set can vary from a few thousand to more than $1 million, depending on die size, part complexity, and required die durability and life. Due to these limitations, major automotive manufacturers produce very similar, if not virtually identical, vehicles at very large volumes. This practice limits potential customization and acts as a barrier to entry for new companies or for new production techniques.
Companies trying to customize their products or bring new technology to market typically lack sufficient opportunities to achieve economies of scale. Low-volume demand for aftermarket parts also suffers from the same limitations. These stakeholders can benefit from alternative methods to affordably manufacture vehicles at initially lower volumes, and reduce the time required to provide new products to consumers.
To study these challenges, Ricardo developed a manufacturing-cost model and database that enables users to estimate production costs and required investments for a large variety of components at different production volumes. The cost model determines bottom-up costs for forming of individual parts, as well as their assembly into components. It can analyze key business drivers such as tooling investment, equipment cost, process time, materials, scrap, automation, labor, supply-chain impact and factory overhead.
![]() |
To develop a cost-effective and rapid process to print dies, the Ricardo-UTRC team opted to use preforms—starting plates or extrusions—and then use the WAAM process to 3D-print all of the necessary features onto the preforms. |
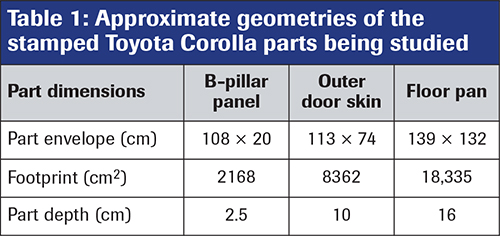
Leveraging its expertise and the manufacturing-cost model, Ricardo studied the costs associated with the conventional manufacture of 10 subassemblies for the Toyota Corolla, representative of a traditional high-volume passenger vehicle. The cost analysis shows that, for all of the analyzed components, production costs start to become prohibitive below an annual volume of 50,000 units. The root cause is the relatively large capital investment needed for dies, fixtures and other tooling. For this reason, manufacturers must try to achieve economies of scale by sharing platforms for different vehicle models, and using common components.