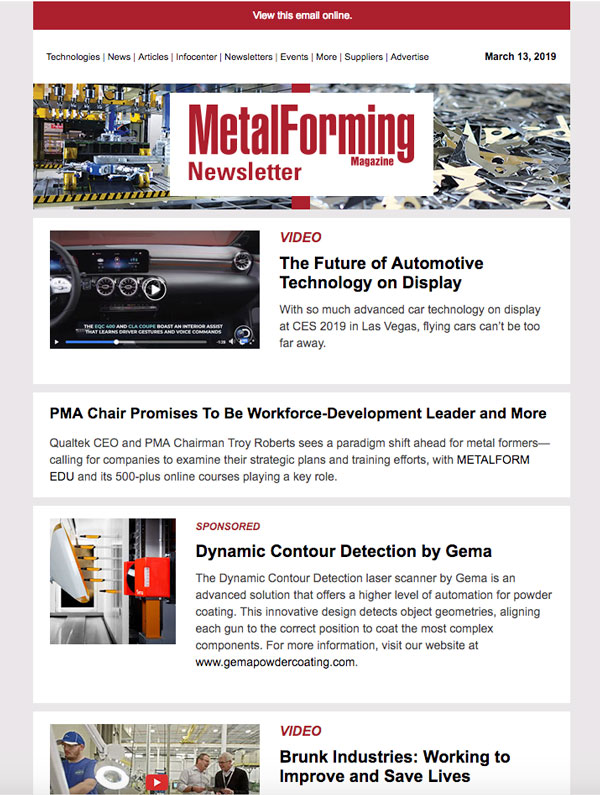
MetalForming
Twice-monthly newsletter, with more than 20,000 subscribers, provides industry decision makers with timely news, announcements and links to videos, podcasts and more.
Subscribe belowView Archives
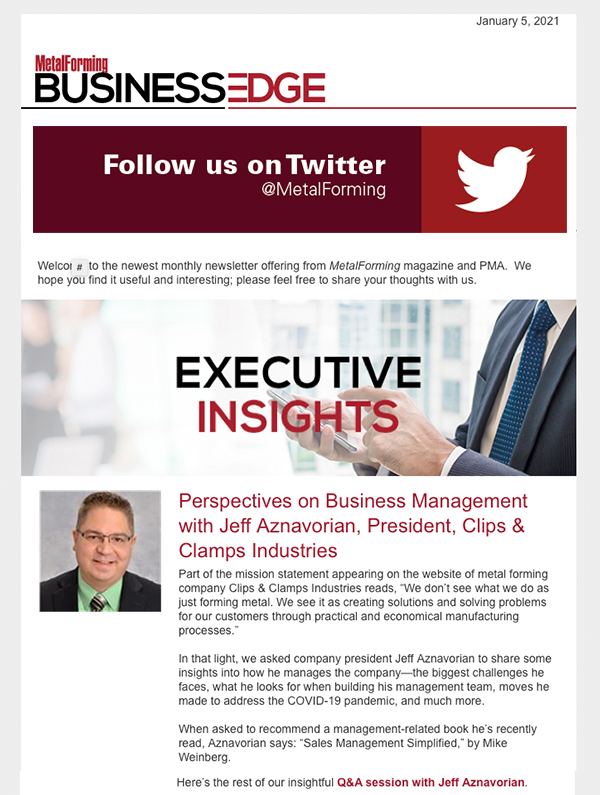
Business Edge
This monthly management-focused e-newsletter provides C-suite executives working in metal forming and fabricating companies with the inside information they need to do their jobs better—to give them an edge on the competition. Included in every issue:
- Executive Insights—Q&A sessions with metal forming company executives.
- Love Letters to Manufacturers—Manufacturing...
Subscribe below
View Archives
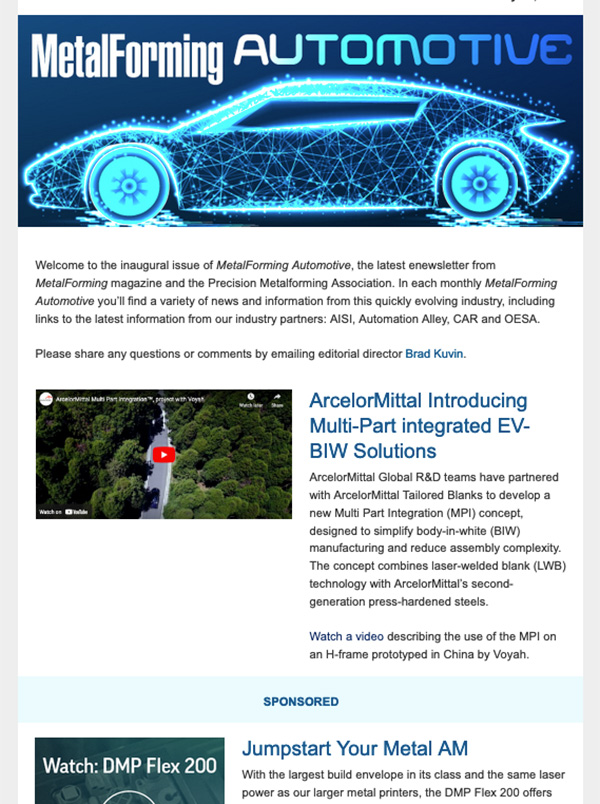
MetalForming Automotive
This monthly newsletter, with more than 20,000 subscribers, provides metal forming and fabricating managers, engineers, and others, working in the automotive-industry, with timely news, announcements, technology-related developments, and links to videos, podcasts and more.
Subscribe belowView Archives
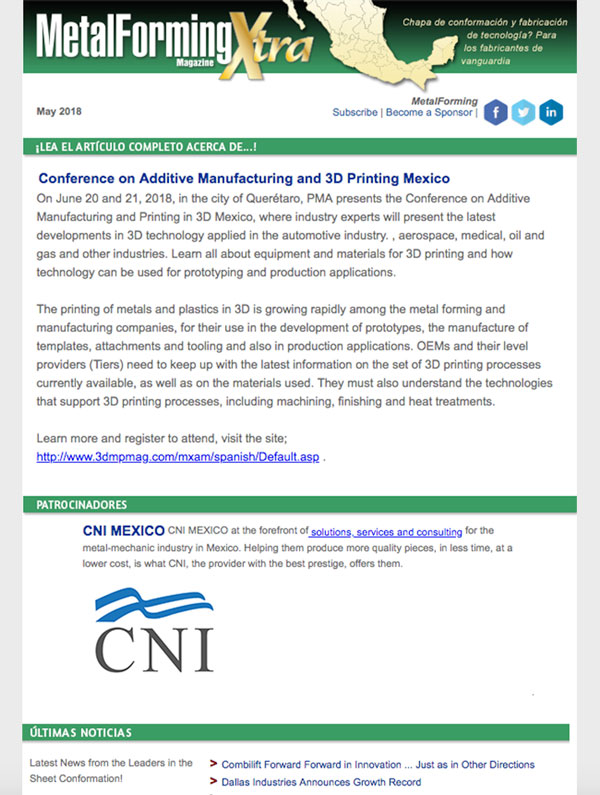
MetalForming Espanol
This monthly Spanish-language newsletter, with 13,000+ subscribers, reaches engineers and managers in the metal forming industry throughout Mexico.
Subscribe belowView Archives