Opt for Integrated Welding Systems
October 1, 2014 High-quality results and optimum productivity are important in every welding application. What many companies may not consider, however, is that the weakest part of a welding system is actually what determines its performance.
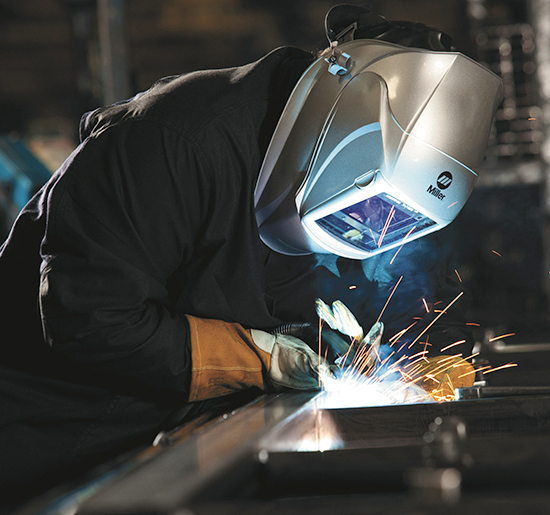 |
Fabricators will benefit from selecting welding systems in which all the components have been engineered to work together. Having components—power supply, welding gun, etc.—that complement one another and work optimally together can help improve arc performance and overall welding productivity, while reducing quality issues and optimizing uptime. |
High-quality results and optimum productivity are important in every welding application. What many companies may not consider, however, is that the weakest part of a welding system is actually what determines its performance. If the welding gun, feeder or power source is performing poorly, for example, the resulting welds also will likely be poor.
For that reason, it is important to have a welding system in which all of the components are engineered to work together. Having components that complement one another can help improve arc performance and overall productivity, while also reducing quality issues and minimizing downtime.
Such welding systems are available for many specific applications, including aluminum welding and pipe welding, to name just a couple. This article discusses the advantages of investing in a welding system (compared to creating one from random components), and the benefits such systems offer for welding operators.
The Importance of Welding Systems
For many applications, welding systems can offer significant performance benefits. Designed systems offer compatible amperage and duty cycles, two of the most important considerations for achieving good weld quality and optimizing productivity. These systems also will be scaled properly to each other to ensure that their features provide the greatest advantages, including preventing potential problems such as poor arc performance or wire-feeding issues. Both of these results can occur when piecing together equipment that is not specifically designed for compatibility.
For example, when using a smart wire feeder that allows multiple parameter settings, communication signals must travel back and forth between the feeder and the welding power source to ensure that all of those wire-feeder features and functions work as designed. Having a system designed with components that work together can provide synergic control benefits for which the system is intended. That may not be possible when using a wire feeder that has not been matched to a given power source.
Similarly, if a welding operator uses a set of welding cables that are too small or otherwise undersized to work with a certain system or application, the cables may overheat or cause a voltage drop. This can greatly affect arc performance, especially during pulsed gas-metal-arc welding (GMAW).
Using an engineered welding system also can make regular service and maintenance easier from a troubleshooting standpoint. Technicians will better know what problems to look for and will be able to pinpoint issues more quickly with a performance-matched system compared to components that are not matched.
Welding Systems Available to Meet Various Needs
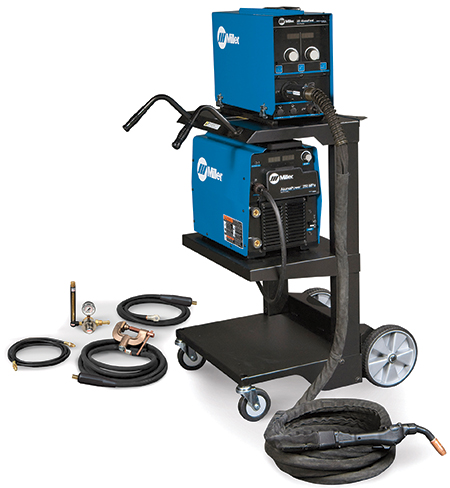 |
Manufacturers offer welding systems designed for specific applications, such as pipe welding or robotic welding, or for use with certain base materials such as aluminum (shown here). Among the biggest benefits offered by using a matched welding system: ease of setup. |
When selecting a welding system, there are many different types suited for various applications and needs. A full welding system typically includes a power source, wire feeder (for a flux-cored or GMAW process) and a gun for GMAW or a torch for gas-tungsten-arc welding. In some cases, the filler metal also may be included or recommended to improve performance for a given application.
The components of a welding system typically are matched together based on the manufacturer’s knowledge of how the features will mesh and how they can help minimize known welding-operator challenges in the industry. Oftentimes, manufacturers design systems around a specific outcome, such as improving productivity, reducing downtime, completing welds faster or reducing burnthrough on certain workpiece materials. More specifically, a welding system can provide specific procedures for welding aluminum without burnthrough or distortion, or provide procedures for welding the root pass in a pipe joint.
Setup Simplified, Relationships Symbiotic
Among the biggest benefits of a matched welding system is ease of setup. Welding operators often can be up and running within minutes when using a system designed to be “plug and play,” when compared to taking hours or days to make unmatched components work together. Once running, welding systems are designed, in many cases, to offer synergic one-knob control using a simplified interface design.
When the welding-system components are specifically matched to work together, arc performance also can be maximized through advanced processes or features. These performance benefits can be especially important during robotic welding. Features and functions can be lost in these applications—often with significant financial consequences—if, for example, the wire feeder and the power source are not communicating properly with the robot control. Robotic-welding systems also are built to incorporate certain safety standards that can make them a safer option than robotic systems that are put together piecemeal.
To ensure all of the pieces of a robotic-welding system work optimally together, be sure to work with a reputable systems integrator who fully understands the system components.