New Capabilities for a Used Press
Press-feed lines and electronic sensoring demand much in the way of press controls, and the right press controller can provide a big assist in ensuring high productivity and consistent tool performance. That is why Inland Tool Company is careful in its press-control selection, according to Gary Mason, the company’s executive vice president and chief operating officer.
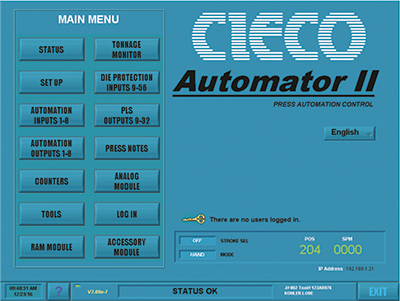
|
This screenshot summarizes the capabilities delivered by a controller installed on an 800-ton mechanical straightside press used to produce automotive parts in progressive dies from high-strength steel. Inland Tool Company notes the controller’s ease of use as a major advantage.
|
After bringing in a used 800-ton mechanical straightside press, the company set about with reconstruction—the press arrived in pieces—and reasoned that this was the perfect opportunity to modernize its control system. “We had one other Cieco press controller in the plant at the time,” Mason recalls. “It worked well for years and years, so we decided to try Cieco’s Automator II controller on the rebuild. It had all of the primary things that we needed, such as die protection; programmable limit switches; tonnage monitoring; job storage; and a menu-driven large-screen menu-driven color HMI that made it easy to understand and navigate. It also offers a variety of screens for job setup and troubleshooting.”
The choice made, Inland Tool Company added the press controller in 2014. Today, the standalone press, with a servo-driven coil-feed line, produces automotive parts in progressive dies from primarily 5-, 6- and 8-mm-thick high-strength steel. While the feed line does have separate controls, it has been configured to interact with the Automator II.
As Mason mentioned, the press controller brings a host of features to the table for Inland Tool Company. Besides the aforementioned 15-in. color touchscreen interface, the resolver-based Automator II delivers eight automation inputs (expandable to 56) and eight outputs (expandable to 32), with more than 145 I/Os available and is field-expandable, according to Cieco officials, meaning that options can be added easily after installation via a card insertion that automatically updates functions on the HMI. Also, HMI screens are field-editable, meaning that application-specific instructions can be added as needed.

|
The press controller’s status screen provides a snapshot of press performance, ideal for quick and easy monitoring. |
A unique feature, according to Cieco officials: All controls and options are contained in the controller’s rack system, eliminating the need for excessive interconnections in addition to reducing installation time, easing troubleshooting and increasing reliability.The controller also provides onscreen diagnostics and status reports as well as the ability to accept as many as 200 security-password users. And, with individual programmability, each function can be enabled or disabled for each user. Other features: a Production Efficiency Chart that provides per-minute 24-hr. graphical view of production; editable help buttons for each screen; the ability to load PDF manuals, schematics, drawings and setup instructions for each die directly into the controller screen; and one-touch backup and restore of settings, jobs and PDFs to the controller memory or a USB stick.
Intuitive Screens Lauded
Mason sees the press controller as very helpful in tackling the just-in-time and volume demands inherent in auto-part production.
“And, overall we are very happy with the controller’s performance,” he says, pointing out that he sees great value in its ease of use. “The operator interface is very intuitive, well-labeled and easily navigable. These features make it relatively easy to train new operators. The controller offers all of the functions we were looking for, especially die protection, and when we need to perform a function or set something, the screens make it easy to find out where to go and what to do. The ability to easily learn it, and use it, is one of its strongest features.”
Mason also points out that Inland Tool Company effectively uses Cieco’s Ears I wireless production monitoring and tracking system to track productivity of the company’s larger stamping presses. With the system, production status can be viewed at each machine and in real time from any PC in the plant. MF
See also: CIECO, Inc.
Technologies: Coil and Sheet Handling, Pressroom Automation, Stamping Presses