Earlier this year, the company unveiled its next-generation Sapphire laser powder-bed fusion (LPBF) AM machine, with the ability to print metal to 1 meter high, and Knust-Godwin, a producer of precision tools and components, as the first customer. The Katy, TX, manufacturer is expected to take delivery of the printer by year’s end, using it initially to produce an oilfield-drilling part currently manufactured by more than five subtractive processes. This Sapphire printer includes a 315-mm-dia. build plate, dual 1-kW lasers, in-situ optical calibration and many of the same characteristics of the existing Sapphire machine. Velo3D officials expect commercial availability of the machine, compatible with nickel-based alloys, late in 2020.
On top of that, Velo3D revealed a $20-million order for its metal-AM printers from an existing aerospace customer, the largest for the company since its commercial launch in September 2018.
“This significant order validates that Velo3D’s SupportFree process is production-ready,” says Benny Buller, company founder and CEO.
|
The Australian Army recently deployed a Spee3d WarpSpee3d 3D metal printer during a field exercise, reportedly the first such field deployment of a metal-AM machine anywhere in the world. The large-format printer uses a patented cold-spray technology capable of printing metal parts in weights to 40 kg at speeds to 100 g/min. |
Additive Industries also announced new funding, a $15.34-million investment that the company plans to use for expansion of its product portfolio, acceleration of its technological roadmap and strengthening of working capital. This coincided with the naming of Mark Vaes, Additive Industries’ chief technology officer, as CEO, succeeding Daan Kersten, who officially left the company in June. Company offerings include the MetalFab1, designed to automate the manual steps of conventional LPBF printers to boost productivity. The machine can be configured to include several modules for extending productivity or automate post-processing.
Configurations include as many as 4 AM cores with one to 4 lasers, and heat treatment, product-removal, storage and exchange modules.
And, buoyed by a February 2020 $1.5-million investment in a trial of Spee3d metal-AM technology to test the feasibility of deploying 3D metal printers both on base and in the field, the Australian Army in June deployed a Spee3d WarpSpee3d 3D machine during a field exercise. This represents the first such military field deployment of a metal-AM machine anywhere in the world, according to Spee3d officials. The large-format printer uses a patented cold-spray technology capable of printing metal parts weighing to 40 kg at speeds to 100 g/min. During the three-day exercise, it was maneuvered to various bush locations and terrains, and unloaded and operational within 30 min., followed by production of various parts.
“The first field deployment of WarpSpee3d was an important milestone for us,” says Byron Kennedy, Spee3d chief executive officer. “While our equipment was designed initially for industrial use, this trial proved that it is robust and can endure harsh conditions and rough handling very well.”
Machine Portfolios Widen
Last year’s formnext show featured several new metal-AM machines from new and existing players, with other platforms introduced in the months since.
Examples of recent arrivals include the AMCM M 4K-1 (single-laser) and AMCM M 4K-4 (four-laser) industrial direct metal laser sintering (DMLS) platforms, produced by AMCM GmbH, an EOS Group company, at a new production facility in Starnberg, Germany. Built on the EOS M 400 platform, the AMCM M 4K is designed to produce, from a range of materials, large parts via its build volume of 450 by 450 by 1000 mm. Company officials see rocket-manufacturing organizations as early adopters of these machines.
Features include increased robustness of the frame design, a new filter system and optional soft recoating. Out of the box, the AMCM M 4K can produce from materials including aluminum (AlSi10Mg), nickel (Inconel 718), and copper (CuCr1Zr) alloys.
These machines can employ various Yb fiber-laser arrays, including 1 by 1000 W, 4 by 400 W and 4 by 1000 W, with scan speeds reaching 7 m/sec. M 4K machines, compatible with legacy EOS M 400-series process-parameter sets, offer a powder-handling option for manual or semi-automatic operation, and open software for process optimization with high power laser.
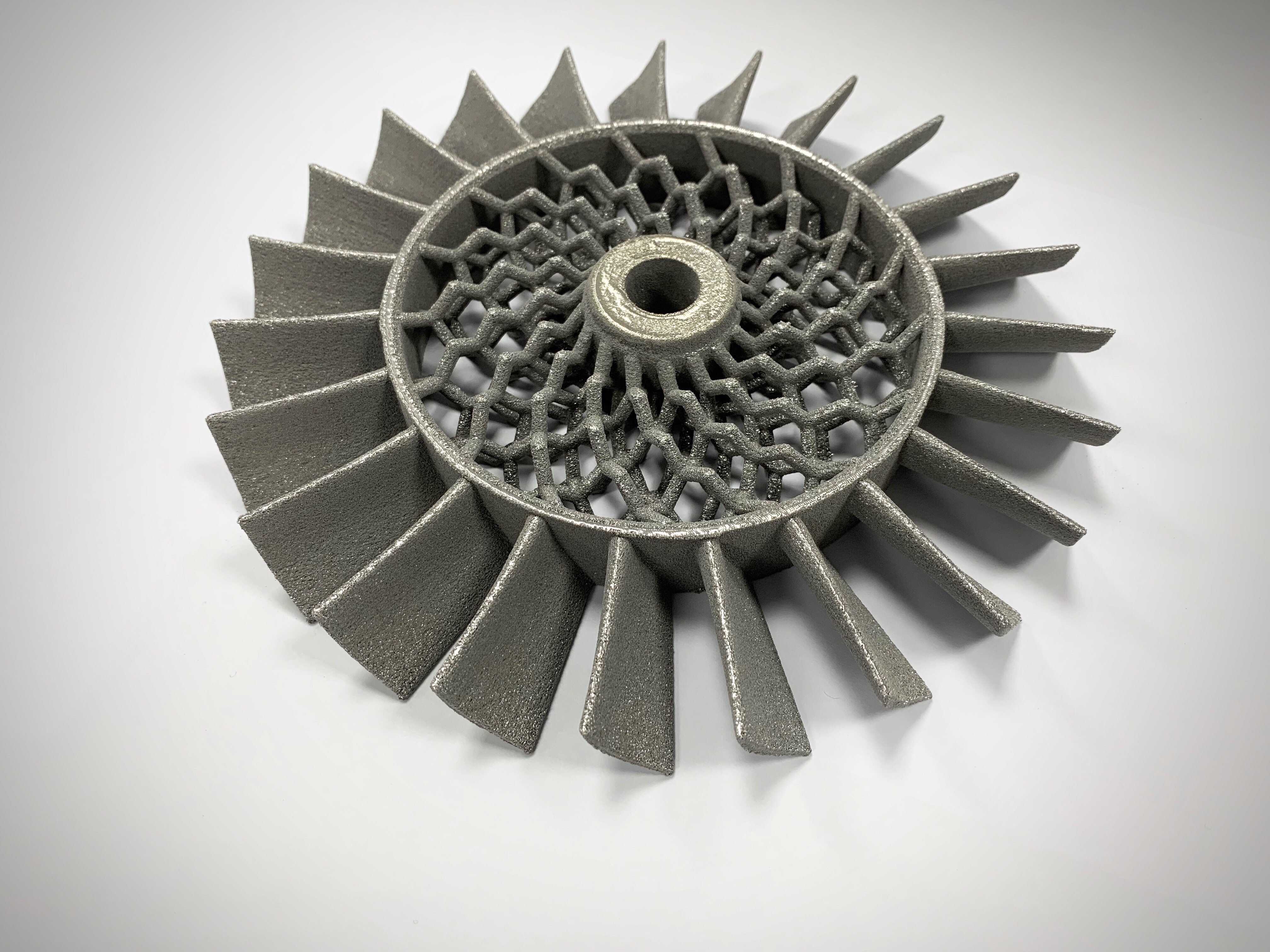
|
Wayland Additive claims to have developed an entirely new PBF process for metal AM that minimizes existing speed and precision limitations associated with laser and EB PBF, respectively. NeuBeam, touted as a third PBF technology even though it employs an EB, reportedly neutralizes the charge accumulation generated by the beam. |
Launcher is one organization cited by AMCM as an early adopter of the M 4K, using the DMLS process to produce its copper-alloy E-2 combustion chamber, reportedly the world’s largest 3D-printed liquid rocket engine.
"The AMCM M 4K solved for both our desire to 3D print a tall combustion chamber in a single piece, and produce it in a copper material,” says Max Haot, Launcher CEO. “Printing in a single piece reduces cost and enables the highest-performance regenerative cooling design.”
Later this year, Launcher will be testing the E-2 at NASA Stennis (MS) as part of an Air Force project.
As part of a collaboration involving plans to install 50 Farsoon metal-AM machines at Falcontech’s Super AM Factory near Shanghai, China, Falcontech and Farsoon (operating as Farsoon Technologies Americas in North America) jointly have developed a customized large-format metal-AM system for aerospace parts, as well as for processing development of Falcontech powdered materials.
Farsoon metal LPBF systems installed or slated for install at Falcontech include FS421M, FS301M and FS271M models as well as the aforementioned large-format system, which provides a build envelope of 620 by 620 by 1100 mm. The new machines at Falcontech enable printing of thin-wall structures—as thin as 0.5 mm—along with dimensional accuracy to ±0.5 mm/800 mm and build surface roughness of Ra 6.3 microns.
Primarily a producer of 3D-printed parts for aerospace, Falcontech bought the first Farsoon machine 2 yr. ago, and also runs metal LPBF systems from several suppliers. To enhance its capacity for series production, Falcontech has undertaken this initiative and plans to incorporate 20 Farsoon systems by end of 2020.
Farsoon touts the “Open for Industry” philosophy of its machines, which it credits for Falcontech’s ability to operate with a high degree of flexibility in parameter setting and material development. This contributes to a total of 20 material-processing parameters for aerospace applications, including multiple types and grades of titanium alloys, aluminum alloys and nickel-based superalloys.
In another collaboration, Renishaw has engaged TraceAM to deploy an end-to-end quality-management tool directly integrated into the Renishaw InfiniAM API ecosystem for AM (see the article on TraceAM beginning on page 25 of this issue). The tool is designed to enable Renishaw to offer its customers, through InfiniAM, a suite of process-monitoring and production-planning tools that provide an efficient and scalable way to track, warehouse, measure and analyze information about each printed part.
With companies advancing their 3D printing capabilities and create parts beyond prototypes, many struggle to create an intuitive, sustainable approach to track the full lifecycle of each part, offer TraceAM officials. TraceAM, they note, was created to provide a quality-management and documentation system for key AM production and technical data. By integrating the tools of Renishaw’s InfiniAM API, Renishaw users now can incorporate real-time machine data into the Trace platform via 24 different sensors already built into the Renishaw metal-AM machines.
The data from these sensors are recorded alongside design, material, post-processing and inspection data for each part. This reportedly enables the ability to document and analyze critical quality-control data, further strengthening users’ ability to meet the safety and compliance requirements set by FAA, FDA and others.
TraceAM now is commercially available, and the Renishaw API integration will be demonstrated through a series of online webinars and tutorials.
Optomec Inc. has debuted integrated robotic automation for its Huffman line of production metal additive-repair machines. The package combines Optomec’s Huffman production laser cladders with a Fanuc LRMate 200, a compact, six-axis industrial robot with the approximate size and reach of a human arm.
This robotic integration automates the loading and unloading of parts into the chuck of the laser cladder, allowing the system to operate at rapid cycle times by working from trays and racks that contain a dozen or more components. Though the automation is especially suited for high-volume repair of turbine blades and vanes, it can be applied to a number of industrial applications such as the repair of sealing surfaces of diesel-engine components, or the addition of hardfacing materials to industrial valve parts.
For laser cladding, Optomec machines employ directed-energy deposition (DED), which enables highly repeatable repairs of high-value components, and delivers superior metallurgy at a lower cost as compared to hand gas-tungsten-arc-welded repairs, according to company officials.
“Before automated laser cladding, the workflow for turbine-blade repair was long and complicated,” says Todd Lorich, Optomec engineering manager for the Huffman line. “Optomec optimized the flow by combining vision systems, software and laser cladding into one hardened, production-grade process step. Now, adding robotic part handling inside of the machine completes the automation for the process, freeing the operator to add more value elsewhere in the workflow.”
Optomec’s DED laser cladding machines are certified for aviation repair in 15 countries, according to company officials, who note that the Huffman line has remanufactured more than 10 million turbine components in the last 15 years.
On the hybrid side, Prima Power Laserdyne has rolled out its Laserdyne 811 five-axis fiber laser-processing (welding, drilling and cutting) system that also includes a DED AM unit. It offers a work envelope of 1100 by 800 by 600 mm in a compact footprint. The company’s BeamDirector technology enables 90-rpm rotational speed and control repeatability of 15 arcsecs. In addition, the BeamDirector supports laser processing from 90 deg. to the part surface, to 10 deg. off of the surface all along the axis of travel. The machine’s S94P controller supports seven axes of simultaneous motion and additional axes as required by automation. This enables integration with a variety of automation solutions for workpiece handling, loading and unloading.
The Prima Additive DED manufacturing system provides real-time, precise control over powder deposition, laser power and shield-gas delivery, enabling powder to be fused into a variety of custom parts or to rebuild metal surfaces, which then are machined to required dimensions and specifications.
Process Advancements
Process development shapes the AM-machine world, with news from organizations touting new ways to add material in builds.
One example: Selective LED-based melting (SLEDM)―the targeted melting of metal powder using high-power light-emitting diodes (LEDs)― the name of new metal-AM technology developed by a team led by Franz Haas, head of the Institute of Production Engineering at the Graz University of Technology, in Austria. Unlike selective laser melting (SLM) or electron beam melting (EBM), SLEDM uses a high-power LED beam to melt the metal powder.
For the AM process, LEDs were specially adapted by Austrian lighting company PreWorks GmbH, and equipped with a complex lens system that enables simple adjustment of the beam diameter from 0.05 to 20 mm during the melting process. The process reportedly can dramatically reduce production time compared to other metal-AM processes. Initially, it will be used to produce bioresorbable metal implants, including screws made of magnesium alloys and used for bone fractures. Other applications under review include the production of bipolar plates for fuel cells.
Also, a U.K. company claims to have developed an entirely new PBF process for metal AM that minimizes existing speed and precision limitations associated with laser and electron beam (EB) PBF, respectively. Wayland Additive’s NeuBeam, touted as a third PBF technology even though it employs an EB, reportedly neutralizes the charge accumulation generated by that beam.
“This offers greater flexibility than LPBF while overcoming the stability issues of (traditional) EB PBF,” says Will Richardson, co-founder and CEO of Wayland Additive. “This means that the NeuBeam process enables metallurgical requirements to be tailored to application requirements rather than to maintain the print process within the narrow bounds permitted by the process. These process capabilities, along with the greatly improved ease of process development, also open up the use of a much wider range of metal materials.”
Despite a couple of commonalities between EBM and NeuBeam, namely that both are PBF processes employing an EB as the heat source to melt the metal powder, the two are fundamentally different, according to Richardson.
“Unlike the traditional EB PBF process, the charging issues that make EBM so unstable have been fully neutralized with NeuBeam using core physics principles developed in the demanding semiconductor industry,” he says. “Moreover, NeuBeam is a hot-part rather than a hot-bed process. This efficiently creates parts that are free of residual stresses because the high temperatures are only applied to the part and not the bed, ensuring free-flowing powder post-build (no sinter cake) and stress-free parts with reduced energy consumption.”
The NeuBeam process reportedly overcomes many EB limitations for manufacturing large, complex metal components, namely no residual thermal stresses, no gas crossflow and a much-simplified powder-removal process. NeuBeam also offers built-in, real-time in-process monitoring, allowing for rapid material development or tuning of microstructures by adapting the solidification during manufacture. With NeuBeam, according to Wayland Additive officials, the process temperature is not constrained by sintering the powder bed, allowing the process temperature to be optimized to the material microstructure and/or the application.
Machine Builders Focused on Materials
“It is all about the material,” offered Phil Schultz, 3D Systems executive vice president of operations, explaining the company’s focus on heavy investment in materials during 3D Systems’ July 2020 virtual tradeshow. “Ultimately, the printers are a vehicle to process the material, and, ultimately, the physical characteristics of what you get in the part are manifest in the material. We introduced a host of materials at the beginning of this year, including many production-grade materials, and continue to evolve that space.
“The systems that process those materials must evolve with them,” he continued. “The ability to handle and process a variety of alloys and their different characteristics really defines and enables certain applications.”
The importance of material, so well put by Schultz, reflects action across the machine-provider spectrum. For example, ExOne recently reported qualification of 15 new materials for printing on the company’s 3D printers. Among the additions: M2 tool steel, Inconel 625, tungsten carbide-cobalt and silicon carbide.
In all, ExOne metal binder jetting systems now 3D print 10 single-alloy metals, six ceramics and five composites, according to company officials. Additionally, 21 powdered materials have been qualified for 3D printing in controlled R&D environments, including aluminum and Inconel 718.
EOS also has expanded its metal material portfolio, adding products for its M 290, M 300-4 and M 400-4 AM systems. EOS ToolSteel 1.2709, validated for M 290 systems, is an ultra-high strength and hardness maraging steel, with typical applications include plastic injection molds, extrusion tools, hot pressing tools and diecasting tools for aluminum and zinc alloys. And, three new products for AlSi10Mg, and Ti64 grades 5 and 23, reportedly offer build rates to 50-percent faster, thus increasing productivity of M 290 machines. Also, EOS NickelAlloy IN718 and EOS MaragingSteel MS1, now are available for the EOS M 300-4. The company also announced that the materials portfolio of the EOS M 400-4 has been extended to include EOS titanium Ti64 Grade 5 and EOS titanium Ti64 Grade 23. Typical applications range from aerospace and automotive components to other industrial applications requiring a combination of low weight with high strength.
AM-Machine Case Histories
As machine, material, part-optimization and process-control capabilities advance, so, too, do applications. Here are a few.
SLM Solutions Partners for Metal-AM Faceshield Injection Molds

|
Here is half of a metal-AM plastic-injection mold produced by SLM Solutions as part of its Additive Alliance Against Corona initiative. The molds are employed by Magnet to produce faceshields for frontline healthcare workers.
|
As part of its Additive Alliance Against Corona initiative, SLM Solutions has, via metal AM, produced plastic injection tooling molds used in making faceshield headbands for the Manufacturing & Advocacy Growth Network (Magnet), a manufacturing-consulting firm in Ohio. SLM Solutions 3D printed the molds in its Wixom, MI, facility, using Type 316 stainless steel. The build was completed in two halves, each taking four days to print and one day for heat treatment.
Magnet, providing hands-on support with business consulting, new-product design, operations excellence and workforce innovation to Northeast Ohio small and midsized manufacturers, sought to acquire injection mold tools to assist in the manufacturing of the faceshields for frontline healthcare workers. The faceshield project grew out of Magnet’s participation in the Ohio Manufacturing Alliance to Fight COVID-19.
Magnet wanted to employ AM to bypass conventional supply-chain complications, according to Dave Pierson, Magnet senior design engineer.
"I chose SLM Solutions because of its quad-laser system," he says. "We needed the parts as soon as possible, and the speed and throughput of the quad-laser machine was a critical aspect of the decision to work together."
At the time, SLM Solutions had just launched the Additive Alliance Against Corona initiative to combat COVID-19 and was eager to help. Jill Christner, president of SLM Solutions Americas, decided to halt normal day-to-day activities in Wixom to give Magnet’s project top priority.
"Responding quickly to Magnet’s project was important for SLM Solutions," Christner says. "It’s an honor to be a small part of the solution to protect the health and safety of those who serve, as well as to utilize the value of our additive technology to quickly produce new products and designs―reducing the lead time of traditionally casted methods."
Once received, the SLM print required some finish machining and polishing, but then quickly was mounted to the machine base to allow further manufacturing at Magnet, according to Pierson.
"SLM exceeded my expectations on their quality and delivery,” he says. “The SLM AM mold now is producing faceshields used by medical professionals across the state of Ohio."
More Efficient Copper Tool Cooler Dramatically Reduces Milling-Machine Downtime
Prototypenzentrum (PTZ) GmbH, Dresden, Germany, needed a new solution for producing a metal tool cooler. Despite a wealth of experience creating metal and plastic prototypes for a range of industries and partners for more than 20 years, this project challenged PTZ. The tool cooler, originally produced from machined aluminum, is tasked with engaging and disengaging a cutting tool in the shank of an endmill through thermal expansion and contraction. The more conductive the cooler, the faster the machine tool can be reconfigured. The machined-aluminum version, though simple to produce, could not achieve PTZ’s desired cycle times due to inadequate thermal performance.
Initially, the PTZ team, well-versed in various AM processes, tried using SLM technology to produce a higher-performing design from AlSi10Mg alloy. Better performance resulted from the inclusion of complex internal cooling channels, but the new design didn't hold up to the cooling medium, and the process proved expensive and difficult to implement.
Ultimately, PTZ discovered that an ideal component could be produced using Markforged Copper in a Markforged Metal X AM system. This new design features conformal cooling channels, making the tool cooler (pictured) extremely efficient, according to PTZ officials, and withstands the cooling medium while providing 38-percent-faster cooling than previous designs. And, by eliminating roughly 40 tool changes/day across two CNC machines, the tool cooler can save 111 hr./yr. in downtime. Given the average hourly machine rate, implementation of this component can save PTZ nearly $7000 annually in machine time alone.
Given the success of the new tool cooler, PTZ plans to use Markforged Copper to develop electrotechnical parts for automotive devices.
Hybrid Process Improved by Using Referencing to Orient Preform with AM Build
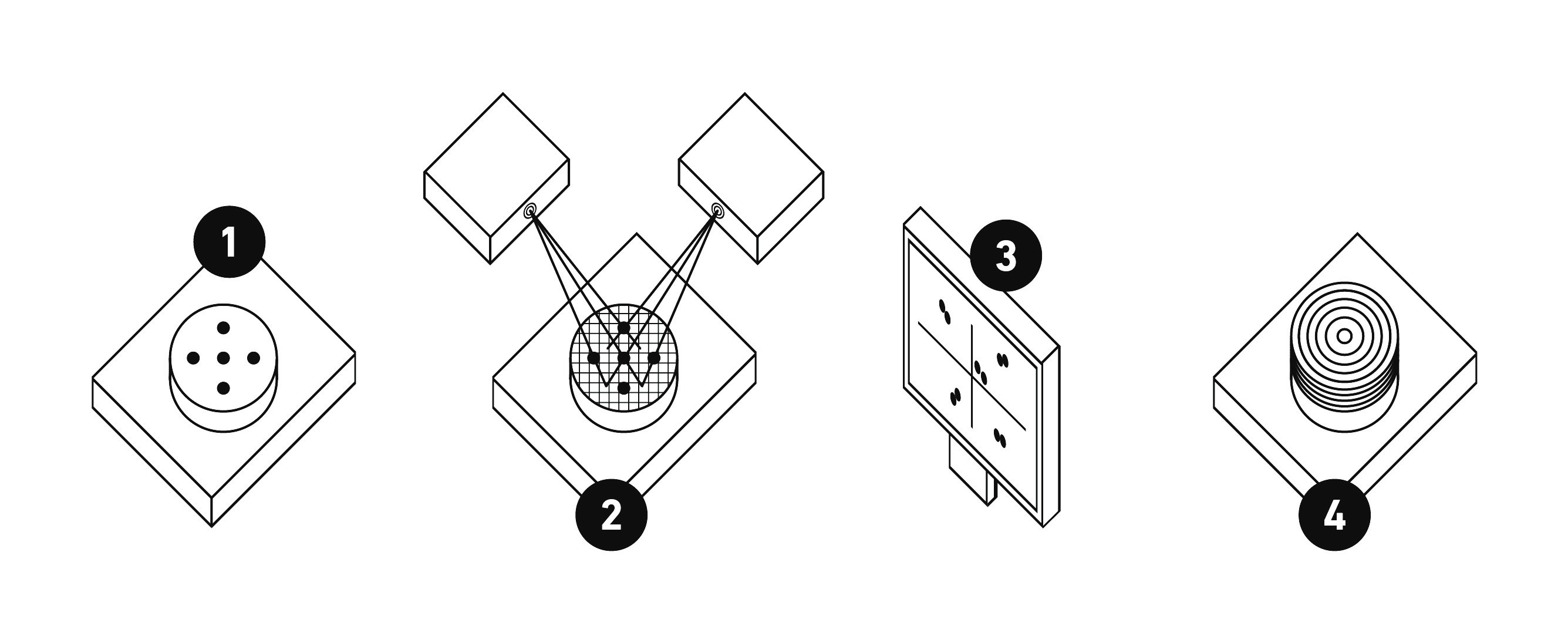
|
This schematic of a hybrid approach using referencing shows 1. a preform with pre-machined holes on the build plate; 2. laser scanning of the preform and holes with light-reflection detection; 3. automatic x, y and θ orientation correction; and 4. the optimized building of the geometry.
|
Parts with features demanding large quantities of material, as well as parts necessitating excessive AM build supports, are good candidates for hybrid manufacturing. Manufacturers can efficiently and economically produce such parts by pre-machining a preform and then using AM in areas where the technology proves most beneficial. In addition, printing directly on a section of the final part geometry eliminates the costly cutting operation to remove the part from the build plate.
Consider injection molds, which include high volumes of material. Fully building these parts layer by layer in an AM machine take dozens of hours and requires redesigning, cooling channels and feed systems that would be difficult to remove in subtractive operations.
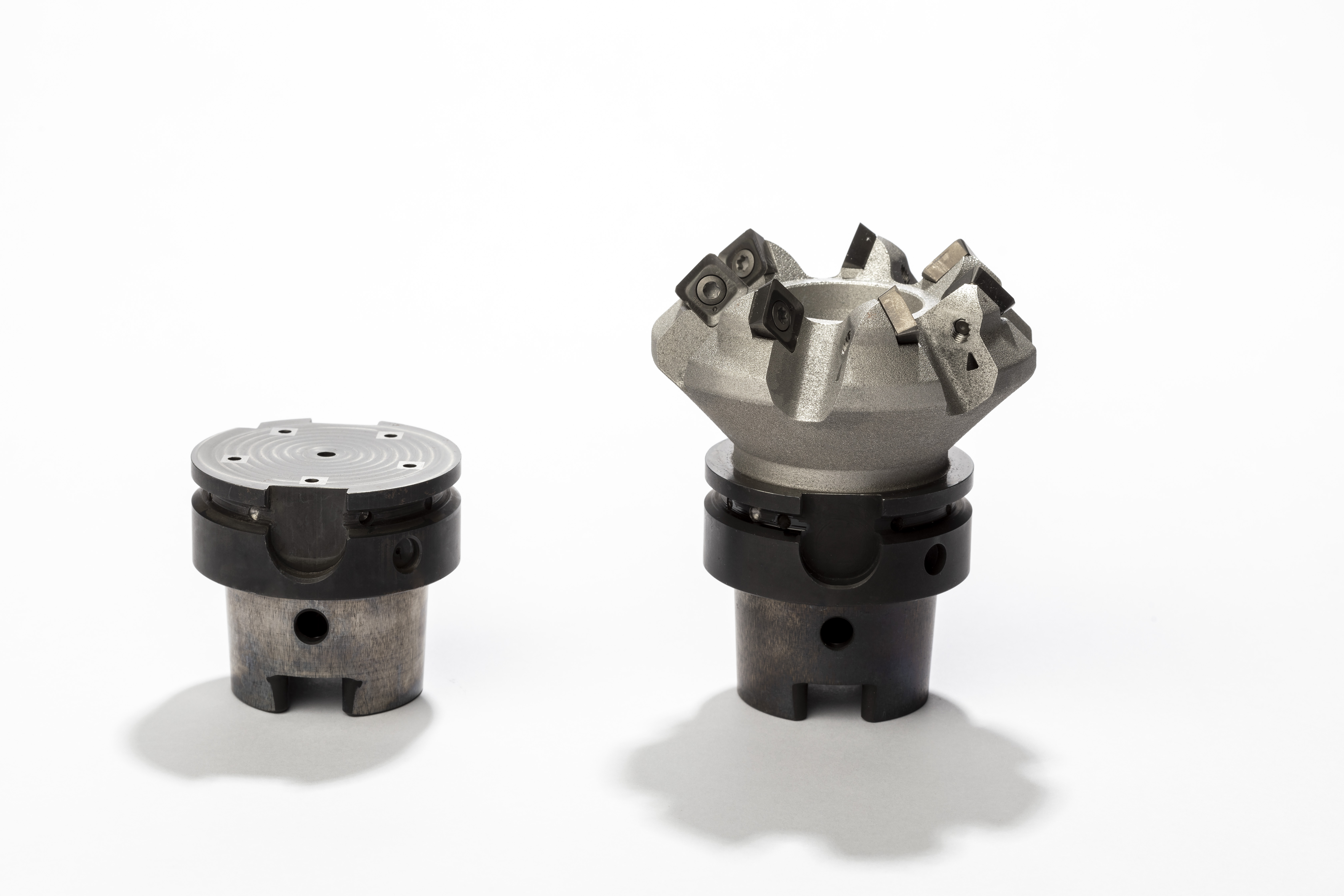 |
A machined tool holder (left), and with the metal-AM cutting head attached (right), shows how a hybrid process using referencing software can produce components. |
This type of hybrid process must start with the preform fixed on the build platform before it is referenced, to align the preform and the intended printed section. Referencing can be especially challenging because, unlike in CNC machining, no physical link exists in AM between the optics and the preform. Instead, manufacturers generally must rely on visual alignment or external CMMs to confirm positioning accuracy. Both techniques are time-consuming and, in the case of simple visual alignment, prone to operator error. With variance in excess of 100 µm, these techniques also cannot provide the accuracy required for most final applications.
To solve the referencing challenge, GF Machining Solutions and 3D Systems have developed a software solution that leverages the melt-pool monitoring hardware available on GF Machining Solutions’ and 3D Systems’ DMP series of metal-AM machines. In machines such as the DMP Flex 350, DMP Monitoring in-process monitoring software acquires melt-pool data during the printing process in order to detect potential defects such as pores, or lack of fusion.
The DMP Calibration Tool function leverages light-sensing melt-pool monitoring hardware for another purpose: scanning preforms to identify pre-machined locating holes in the part’s surface. Naturally, a part surface and hole offer much greater contrast than the reflectivity differences used to optimize highly precise metal-AM processes, allowing for an extremely reliable method for establishing the part’s precise location, according to GF Machining Solutions officials.
With user-defined threshold values, this referencing process reportedly offers exceptional repeatability and accuracy without risk of human error. Furthermore, the use of the laser can reference multiple parts on the same build plate in a single operation, further accelerating high-volume applications. And, the level of precision results in higher final-part quality.
This method of subtractive-first hybrid manufacturing employing the referencing software has many obvious benefits for producing mold-and-die inserts and machined tool holders with AM tool heads, for example, but also proves useful for part production in such industries as medical and aerospace. Shops can cut preforms prior to building complex part features via 3D metal printing. Applications include aerospace components and medical devices that feature complex internal structures, as well as the creation of functional surfaces for products such as implants, which benefit from geometric precision inherent in AM for building metal forms that promote improved integration with existing skeletal and vascular structures.
Most beneficial for this process: a turnkey system in which every piece of the equipment and software package has been calibrated for seamless hybrid workflows, according to officials from both companies. One example in the GF Machining Solutions Additive Manufacturing ecosystem: the 3DXpert all-in-one software for AM part design, optimized for DMP-series machines and compatible with GF Machining Solutions’ Mikron Mill machines used to simplify post-processing operations.
EBM AM, Combined with AI, Delivers Advancement in Knee Reconstruction
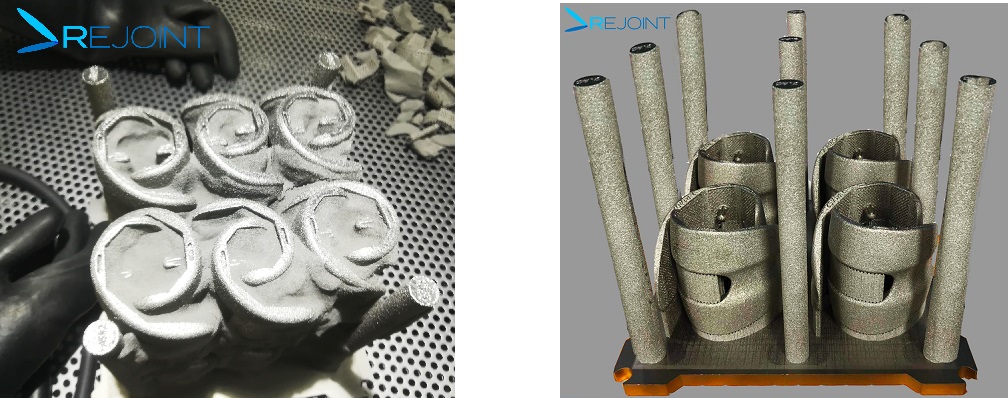
|
Italian company Rejoint has selected a GE Additive Arcam EBM Q10plus system to manufacture cobalt-chrome knee prostheses, and is expected to obtain FDA 510(k) clearance in the first half of 2021, enabling access to the lucrative U.S. market. |
Rejoint, in Bologna, Italy, founded in 2015 by a team with many years of experience in the orthopedic sector, recently entered the knee arthroplasty market, keying on AM and artificial intelligence (AI) as integral to its growth strategy.
“When it came to additive manufacturing, we initially were undecided about the most suitable solution for personalized cobalt-chrome prosthetics and were evaluating DMLM and EBM processes,” explains Gian Guido Riva, Rejoint CEO. “Both modalities offer a good level of resolution and quality, but we ultimately opted for the GE Additive Arcam EBM Q10plus system. At the moment, ours is still the only solution for AM knee prostheses in cobalt-chrome to be certified and introduced to the market.”
To produce the AM prosthesis, Rejoint begins by 3D modelling a patient’s CT scan. Sophisticated AI algorithms then analyze the images to identify the most suitable size for each specific case, comparing the unique anatomy of a patient on several thousand prosthetic dimensions, each with as many dimensional variables in specific areas of the implant.
The surgeon then is offered the optimal configuration, for positioning both the prosthetic components and for simulating the operation. This analysis forms the basis for the production of the prosthesis and for patient-specific tools for the planning of the intervention.
For orthopedic implants, the build area of the Arcam EBM Q10plus, 200 by 200 by 180 mm, is designed to allow for optimal stacking of the most common implant types, with the build chamber interior enabling simple powder handling and rapid turnaround times, according to GE Additive officials. The Q10plus, they note, is particularly ideal for production of high-volume, press-fit implants with advanced trabecular structures as derived from CT scans of individual patients.
The machine, with 3-kW EB power, includes Arcam EBM xQam technology for precision autocalibration, and a software platform and electronics for to provide efficient and accurate beam control. It also features Arcam EBM LayerQam, a camera-based monitoring system for inline part-quality verification, and a powder-recovery system.
Rejoint also gathers data from the actual operation, and after via examinations and patient wearables, to strengthen its algorithms. This is important, notes Riva, as despite the sale of so many surgical pieces, little information is available on what happens to these pieces post-sale.
This innovative approach, now part of Rejoint’s high value-added offering, enables identification of correlations that trace the whole process, from the interactive preoperative planning right through to the rehabilitation phase.
“By 2022, we will have the complete data of thousands of cases available,” Riva explains. “This will provide us with an unparalleled wealth of application information, in terms of completeness, in the sector. Despite the sale of millions of pieces, there is little or no information on what happens post-sale.”
The company currently is in the process of obtaining U.S. Food & Drug Administration, FDA 510(k) clearance--expected in the first half of 2021. Certification means access to the U.S. market, which accounts for 62 percent of the world market for orthopedic devices and more than 70 percent of the value of the global market for knee implants, according to an orthopedic-industry annual report.
GE Additive is working with Rejoint to reduce powder-based production costs, focusing on the reduction of cycle times and the optimization of parameters, including through the development of remote production-control stations. 3DMP
Industry-Related Terms: Alloys,
Bed,
Case,
CNC (Computer Numerical Control),
Core,
Hardware,
LASER,
Layer,
Lead Time,
Plate,
Polishing,
Silicon Carbide,
Spectrum,
Stainless Steel,
SurfaceView Glossary of Metalforming Terms
See also: Renishaw Inc., 3D Systems, Optomec Inc., EOS of North America, Inc., Desktop Metal
Technologies: