Springback, Die Life and Other Challenges
The application of these high-strength grades initially created significant manufacturing challenges. Metalformers were faced with the difficulty of forming components within the steels’ restricted forming envelopes while maintaining part dimensional tolerances challenged by springback. Other challenges revolved around die life, since the strength of the steels being stamped approached that of the die steels. This resulted in die wear and fatigue under the required forming load. Over time, die technology evolved to address these challenges, allowing the use of Dual-Ten 590 to mature to where it is now a regularly used material at many automotive-stamping facilities. Likewise, Dual-Ten 780 and 980 are rapidly progressing down the same path.
Meanwhile, some of the challenges faced when forming these new grades were not anticipated and rarely experienced with conventional mild and high-strength steels. As demand grew for applications of Dual-Ten 780 and 980, stampers began to experience some previously uncommon stamping failures, such as cracking of sheared edges during stretching and shear fracture at tight bend radii. These failures—associated with areas in the stamping that undergo a significant amount of localized deformation—have been termed “local formability” failures. While traditional necking and splitting of stampings has been understood and predicted for several decades using analytical tools available for simulation and for use in the field, no such tools exist for these new failure modes.
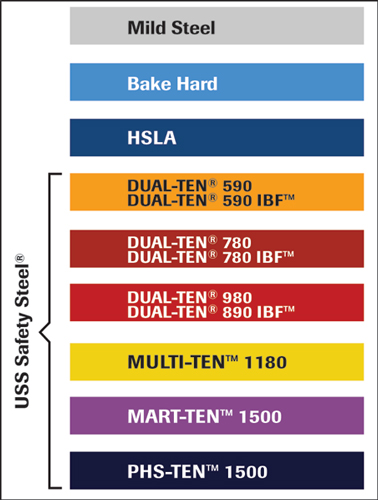 |
The USS Safety Steel family of steels, which includes the popular Dual-Ten 590 and 980 grades, “represent 10 percent of the flat-rolled steel in a typical vehicle,” says Mike Juddo, United States Steel’s director of product technology, “or 160 lb. per vehicle, with some vehicles reaching well in excess of 300 lb. Looking to the future, our customers expect to increase the use of these high-strength grades to 40 percent, or 590 lb. on a typical vehicle.” |
“At United States Steel’s Automotive Center (in Troy, MI), we are working to develop technology to predict local formability failure such as shear fracture and edge cracking,” says Dr. Ming Shi, United States Steel’s manager of advanced applications technology, “and to identify more robust manufacturing techniques to prevent these failure modes. We are making progress in the lab, as well as through partnerships with universities and our customers.”
As an example, a common failure experienced in production has been at the sheared edge of a stamped blank. An extensive study conducted at the United States Steel Automotive Center found that significant improvements can be achieved with the shear die configuration by optimizing the shear die clearance, cutting angles and shearing speed. When implemented correctly, a blanking die that employs these techniques can provide a 25-percent improvement in edge-fracture strain compared to conventional blanking-die designs.
IBF Steels
United States Steel also is taking a product-development approach to addressing local formability issues, evidenced by the recent development and commercialization of IBF (Improved Bending and Flanging) steel grades. Through microstructure optimization, these grades provide a 50- to 100-percent improvement in local formability properties compared to traditional Dual-Ten 780 and 980 grades. In a recent stamping study conducted by the Auto/Steel Partnership to evaluate several 980-MPa tensile-strength steels on a part prone to local formability failure, an IBF 980 grade provided superior performance and was able to meet the forming requirements. IBF grades have been a game changer, enabling the use of 780- and 980-MPa steels in critical applications that would not otherwise be possible with traditional dual-phase grades.
“With the application of 980-MPa grades already being deployed in current products, our customers are demanding even higher strength as they prepare to meet the fuel-economy requirements of the new CAFE laws implemented for 2012-2016,” says Bart DePompolo, technical marketing manager at the United States Steel Automotive Center. “In response, we are developing coated and uncoated products at 1180-MPa tensile strengths, already targeted at 2014 production-vehicle platforms.”
Added Capacity for Multiphase Steels
In December 2010, United States Steel and Kobe Steel announced the construction of a new state-of-the-art continuous annealing line at their Pro-Tec Coating Company joint venture in Leipsic, OH. The new line, expected to reach full production by the end of 2013, will have the capacity to produce 500,000 tons annually of Dual-Ten, Trip-Ten and Multi-Ten steels at strength levels to 1200 MPa, as well as tempered Mart-Ten steels to 1500 MPa.
Looking to the future, the full capability of this facility will be leveraged to produce the next generation of high-strength steels to provide grades at strength levels of 800 to 1500 MPa, with formability attributes that will exceed the current range of products, and martensitic steels with strength levels to 2000 MPa. This next generation of USS Safety Steel products will be targeted at providing automotive customers with increased design flexibility in achieving the advanced lightweight designs of the future.
To demonstrate how these new grades can help the automotive industry meet future objectives, an engineering design study recently was conducted to investigate the mass-reduction potential of applying USS Safety Steels family of steels to a current production vehicle. The study demonstrated the potential for a 20-percent mass reduction of the body structure when more than 90 percent of the body structure was comprised of USS Safety Steel with an average strength of 750 MPa. This mass reduction was accomplished while maintaining the predicted high level of crash-safety performance, ride and handling attributes, and durability of the baseline vehicle without increasing the estimated manufacturing cost of the body structure.
The study includes hardware builds and full-scale testing to validate manufacturing and performance of critical structural systems. As an added benefit, studies show that vehicles designed to be produced with these lightweight steels are advantaged, from a vehicle’s lifecycle carbon-emissions standpoint, compared to those vehicles that potentially employ competing materials with carbon intensities that can be six to 20 times higher than steel. (Lifecycle analysis considers carbon intensity of materials used in the vehicle, as well as that associated with its build, road life and eventual recycling).
Next-Gen Steels to Realize True Design Optimization
Vehicle makers’ desires for higher-strength steels, and the recent advanced steels developed to support those needs, have helped enable mass reduction relative to the grades they replaced, while providing the required performance in crash safety, ride, handling and durability. However, while these new grades provide sufficient formability to allow them to be manufactured into the geometries needed for automotive designs, they still often require significant design concessions that compromise the full structural optimization and utility of the design.
The next generation of high-strength and more formable steels are anticipated, to help resolve this conflict in realizing true design optimization. The added formability will enable designers to fully optimize the shape of components and take full advantage of the strength of these steels. This will allow a leap forward in design efficiency and mass reduction while achieving structural performance targets. MF
Industry-Related Terms: Bending,
Center,
Die Clearance,
Die,
Ductility,
Edge,
Forming,
Hardware,
Shearing,
Blank,
BlankingView Glossary of Metalforming Terms
See also: United States Steel
Technologies: Materials