Pay attention: The solar-thermal energy market--which converts the suns energy into hot fluids or steam--is set to take off. North American metalworkers already are benefiting, fabricating frames, collector panels and absorber fins.
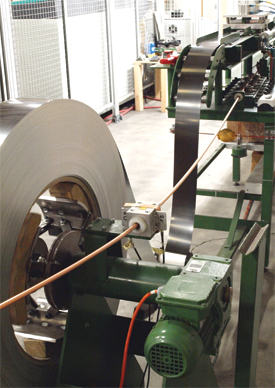 |
To manufacture absorber fins for flat-plate solar-thermal collectors, Alanod-Westlake Metals’ laser-welding line joins coated 0.5-mm-thick aluminum, slit to 120-mm wide, to 10-mm-dia. copper tube. Strip and tube feed from coils simultaneously through the 60-ft.-long production line that runs continuously at 7.5 m/min.
|
Likewise, Scottsdale, AZ-based OEM Stirling Energy Systems contracts with Tower Automotive to fabricate metal support structures and stamp aluminum substrate to which it attaches mirror facets. Again, heat collects at the mirror surface, and then is reflected into a power-conversion unit that converts the heat to drive a generator.
Summing up this expanding market, Hames adds that, “during just the last two years, this industry has installed more than 40 million lb. of extruded-aluminum frames for solar applications, and we’re only at the tip of the iceberg.”
Solar-Thermal on a Smaller Scale
Solar-thermal systems on a much smaller scale, for water heating in homes and businesses, including community swimming pools, also have gained a foothold. And in my hometown of Cleveland, OH, one metal-service center has carved a substantial niche in the market, processing specialized sheetmetal and then laser-welding the material to fabricate collector fins.
German-based Alanod-Solar has begun to manufacture its Miro-Fin absorbers at a metal-processing facility it purchased late in 2007—Alanod-Westlake Metal Industries, in North Ridgeville, OH, just a few miles west of Cleveland. Alanod, which takes a different approach to collecting solar energy by offering systems that absorb rather than reflect the sun’s rays, made its name in the lighting industry by marketing reflective-aluminum fixtures for the energy-efficient T5 lamps that have taken over the market. And, likewise, for several years Alanod-Westlake Metals has enjoyed—and continues to do so—tremendous success turning the specially coated coils of aluminum into blanks for light-fixture OEMs all over the United States.
Now Alanod-Westlake Metals is accompanying its parent company on a venture to expand the solar-thermal industry in North America, hoping to mirror the success it’s had in Europe with its absorptive solar collectors.
“The company recognized starting in 2000-2001 that its retrofit lighting products had probably a 10- to 15-yr. run in the market, as large companies changed over their lighting fixtures to become more energy efficient,” says Alanod-Westlake Metals vice president Frank Lee. “When they learned that the PVD coating process they use to apply the reflective material to aluminum also could be used to apply an absorptive coating to aluminum as well as copper substrate, it quickly made a move into the solar-thermal industry. Its solar-energy presence in Europe has grown tremendously since then, and now Alanod looks to do the same here.”
Alanod-Westlake Metals historically has specialized in processing light-gauge prepainted steel and coated aluminum—blanking and slitting primarily, with a bit of stamping and fabricating thrown in. Nearly all of its work is surface critical.
“We got into that work in the late ’70s and through the ’90s primarily for the appliance industry,” says Lee. “In the mid-’90s Alanod began contracting us to blank its coated reflective material for lighting OEMs, and in 1999 asked us to install a slitter specifically to support its lighting customers. By 2007 we were slitting more than 1 million lb. of the material per month, accounting for 60 percent of our overall throughput. Finally, in November 2007, Alanod acquired 75 percent of the company.”
Solar-Fin Production Line the First in North America
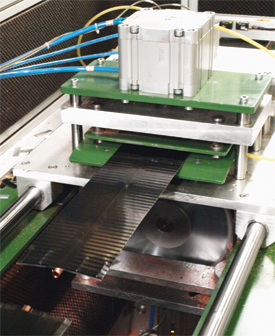 |
A flying cutoff die cuts welded fins to length. Note the gentle corrugation pattern to the strip to add rigidity. A protective film on the top of the strip maintains the critical surface integrity during processing. |
When the parent company sought an entry point to the North American market for its solar-thermal collector materials, called mirotherm (coated aluminum sheet) and sunselect (coatedcopper sheet), its Ohio entity was the obvious choice. Fabricating the coated sheet into absorber fins (called Miro-Fins), which then are marketed to flat-plate collector manufacturers, requires laser welding the sheet to copper tube. Once the collectors are installed—on top of your house, for example—absorbed solar energy heats water or some other type of liquid flowing through the copper tube.
When the parent company sought an entry point to the North American market for its solar-thermal collector materials, called mirotherm (coated aluminum sheet) and sunselect (coatedcopper sheet), its Ohio entity was the obvious choice.To enable mass production of the laser-welded fins, Alanod Solar worked with Swiss company SunLaser Consulting GmbH to develop an automated laser-welding line that in 2008 was declared by the European solar industry as “the new industrial standard.”
Since 2006, SunLaser, working with system integrator MiniTec Schweiz AG, has delivered 13 of its turnkey laser-welding systems worldwide. In March, it installed one of the lines at Alanod-Westlake Metals.
“We dedicated and kicked off production of our new high-capacity laser-welding line on March 9,” says Lee, “with great fanfare and expectations. The line runs twelve 10-hr. shifts/month, processing the fins at 7.5 m/min. and accounts for about 15 percent of our overall sales. The hope is that, as it has done in Europe, SunLaser will eventually install its laser-welding production lines in several facilities throughout North America. That would allow us then to focus on providing slit mirotherm and sunselect coils to numerous collector-production facilities,” says Lee.
The market potential is definitely there, as the solar-thermal industry grows and collector manufacturers become more automated and productive. “Most U.S. collector manufacturers assemble the units manually,” says Lee, “at a rate of 20 to 25/day. Automated lines in Europe produce as many as 30 collectors/hr.”