Defining Acceptable Burr Height
August 1, 2013Comments
The maximum acceptable burr height for a metal stamping is equal to 10 percent of sheetmetal thickness.
The above statement would be true if all stampings were produced from low-carbon steel less than 0.050 in. thick, using typical punch-to-die cutting clearances. However, this, like so many other metalforming “rules of thumb,” has been repeated by so many for so long that we’ve come to accept it as absolute fact without regard for its origin. The 10-percent burr-height rule can be found in publications as early as the nineteenth century, including J.L Lewis’ Dies and Die Making, published in 1897.
Why is the 10-percent burr-height rule of thumb often unreasonable or inappropriate? As burr heights begin to approach 0.003 in., they start to become noticeable. In some instances, burr heights greater than 0.005 in. can become dangerous, potentially cutting or otherwise harming assembly workers. Also, die-cut edges subjected to high tensile stresses—such as those seen in stretch flanging—can be very sensitive to edge quality and burr height. The quality of the cut edge, including burr height, can be the difference between producing a good part or not.
Note: Here’s one more example, also from J.L. Lewis’ book, of how the old metalforming rules of thumb may no longer be applicable. Lewis writes: “In the re-punching of brass and copper, the use of buttermilk as a lubricant will give better results than any oil or soap water that we have yet found.”
Today, a wide variety of material compositions, mechanical properties and thicknesses are routinely produced in metal-stamping dies, a far cry from the limited metallurgy and slab-rolling capabilities from the 19th century. As a result, one must discard many of the archaic rules of thumb and apply an engineering approach.
An engineering approach to establishing burr-height limits would recognize that cutting and punching impart shear stresses in the workpiece material, and that these stresses relate directly to the material’s ultimate tensile strength. Materials with high yield-to-tensile strength ratios (Inconel, for example) require tight punch-to-die cutting clearances, typically 5 to 8 percent of material thickness per side. These highly formable materials want to deform or extrude the hole feature rather than shear or cut, making burr-height control difficult to manage.
Materials with low yield-to-tensile strength ratios (many high-strength steels, for example) require greater punch-to-die clearance to provide the mechanical leverage required to break the slug cleanly with a minimum burr. In these instances, stampers apply engineering clearances—punch-to-die cutting clearances beyond the traditional 5 to 8 percent of material thickness per side. Engineering clearances result from extensive research conducted during the last 50 years.
Engineering clearances as great as 40 to 50 percent per side may be applied to very thin materials, depending on hole size and material type. Recent research with advanced high-strength steels (Konieczny and Henderson, 2007) indicate that as much as a 21-percent per-side clearance may be required for some materials. Lewis and his peers were unaware of such clearances.
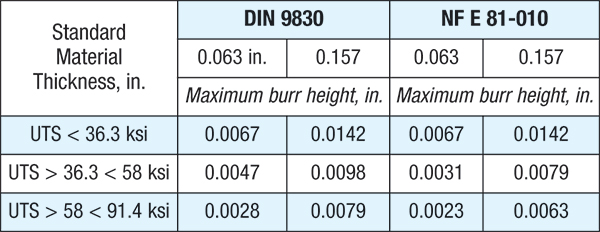
I am familiar with two standards that recommend and specify engineered clearances: DIN 9830 (a German standard) and NF E81-010 (a French standard). Both classify acceptable burr heights relative to workpiece material thickness and tensile strength. The accompanying table provides maximum burr-height specifications from each standard for a precision punched hole in 0.063-in.- and 0.157-in.-thick material. Note that the maximum burr allowance for 0.063-in. material with a tensile strength less than 36.3 ksi is 0.0067 in., following the 10-percent rule of thumb. However, as material tensile strength increases to 90 ksi, the maximum allowable burr is 0.0023 to 0.0028 in.
When material thickness increases to 0.157 in., allowable burr height for the 36-ksi and 90-ksi materials is 0.142 in., and 0.0063 to 0.0079 in., respectively. In this case, both scenarios are less than the 10-percent rule of thumb.
So, the next time someone asks about the maximum burr-height allowance for a particular stamping, take an engineering approach to answering. It is, after all, the 21st century. MFView Glossary of Metalforming Terms
Technologies: Management
Comments
Must be logged in to post a comment. Sign in or Create an Account
There are no comments posted.EWI President/CEO Dr. Cialone Retiring
Monday, June 30, 2025

Tariffs are Not a Strategy: A Call for Action by U.S. Manufa...
Laurie Harbour Tuesday, May 27, 2025

Protecting Your Manufacturing Business Amidst Tariff Changes...
Mike Devereux Friday, May 2, 2025