An Even, Thin Lube Layer, Top and Bottom
“The biggest benefit from the roller coater, compared to our spray systems on the other presses,” says Essenburg, “is the ability to apply lubricant evenly on the bottom as well as the top of the material. With the spray systems, to ensure consistent coverage across the entire sheet often requires overspraying. And, even then, we’re not always able to adequately coat the outer edges of the tooling with lube, where the stock may be dry and cause premature tool wear.”
Since bringing in the new 700-ton servo press, in mid-2019, Grant has moved eight dies over from the 800-ton conventional mechanical press, “to allow us to reduce lubricant consumption and tool wear,” Essenburg says, “and also to run faster, taking advantage of the servo press’s pendulum motion profile.”
Compared to running tools on the conventional press equipped with spray-lubrication systems, Grant has experienced, on average, a 35-percent reduction in lubricant consumption, as well as a 30-percent increase in the number of hits between tool-maintenance cycles.
“Those two factors, in addition to less cleanup around the press since there’s no overspray,” adds Grant, “easily justified the investment in the roller coater. In fact, we’re evaluating investing in a second Unist system, for the 800-ton Nidec Minster press.
“We’re also beta testing for Unist its new SmartFlow controller,” continues Grant, “and later this year will also start testing its Advanced Fluid Tracking (AFT) software to track lubricant consumption by the job.”
New Controller and Software
The roller coater continuous stock-lubrication system installed on Grant Industries’ new servo press features rollers—on the top and bottom of the stock—through which lubricant flows from the inside out. A dispenser tube inside each of each roller has small holes placed along its length through which fluid is injected, under precise control. Lubricant transfers to the stock on its way to the press via polyester-felt or polyurethane-foam roller covers. With the internally fed roller design, the roller coater may only need to inject lubricant into the rollers once every eight to 10 press strokes, just to keep the roller covers saturated in order to adequately coat the coil stock, compared to a spray system that may need to apply lube with every press stroke. |
The Unist SmartFlow controller that directs the roller coater alerts users, by monitoring sensor data, to issues before they become expensive problems, such as low fluid supply runs, out-of-tolerance fluid pressure, or if flow to one of the applicators becomes interrupted. The fluid-supply tank includes low- and high-level sensors, with a float switch to allow for automatic filling through the plant’s central lube system and two mixing tanks—one tank for a water-based “house lube,” and a second auxiliary tank to allow mixing of custom lubricants to customer specs. It can send error messages directly to the press-control HMI and enable the press operator to make any necessary adjustments to the lube system at the press control.
“The AFT software, an Industry 4.0/Internet of Things add-on,” explains Essenburg, “will make it easier for us to capture live data from the Uni-Roller system, so that we can develop a history of lube consumption for each job. We’ll be able to export the data any number of ways and share it across the plant.”
Speaking of jobs for the new press line, Essenburg describes one die that runs particularly well on the new servo press, thanks in large part to the roller coater. “The roller coater has far exceeded our expectations and has allowed us to bid on jobs we would have had to pass on before,” he says.
For example, one of the more aggressive draw-form tools that processes 0.088-in.-thick high-strength steel (50-ksi yield strength) performs a significant amount of drawing and forming. “It generates a lot of heat,” Essenburg shares, “especially since the job runs nearly twice as fast on the servo press as it would on the conventional press. And, the roller coater performs exceptionally well, precisely and with great repeatability coating the top and bottom of the 17.6-in.-wide coil stock.”
Synchronization
A key to successfully leveraging the speed capability of the servo press is synchronization between the press, feed line and lubrication system. “As the press cycles open with each stroke,” explains Essenburg, “the material feeds, and while the material feeds, the roller-coater control knows exactly how much lubricant to deliver to the rollers, based on process variables saved to the job recipe—feed length (which varies from 3 to 20 in.), press speed and material width. And it all happens under the direction of the press control.
“In addition, we can customize the location and thickness of the lubricant, based on the specific requirements of the die,” Essenburg continues. “For example, if the die will perform a drawing operation in the center area of the die, we can program the roller coater to apply more lube in that area, and then lay down a thinner coating of lube on the outer areas of the strip.
“This,” he adds, “is a game-changer for deep-draw work, to help minimize lube consumption while improving die life.” MF
View Glossary of Metalforming Terms
See also: Unist, Inc.
Technologies: Lubrication
Comments
Must be logged in to post a comment. Sign in or Create an Account
There are no comments posted.Mexico Stamping Technology Webinar Series 2025: Day 2
Thursday, April 3, 2025
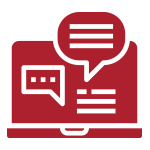
OEM Realizes 60% Reduction in Stamping-Lube Use
Brad Kuvin Thursday, February 6, 2025