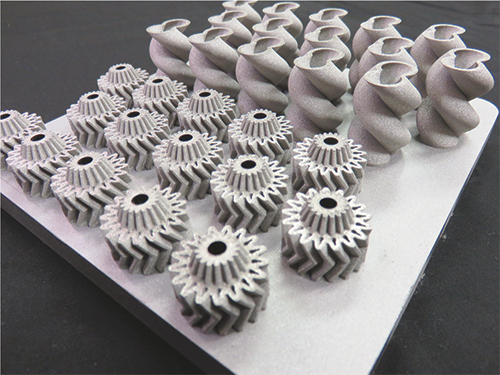 |
Metal AM parts with otherwise impossible or expensive-to-produce geometries.
|
Markley’s team sees many projects that present plenty of advantages to be gained through metal AM, but where clients will not pull the trigger on full-scale production. “Many companies are sitting on the sidelines waiting for someone to hand them the answers, rather than going out and seeking them,” Markley says.
The root cause has nothing to do with metal-AM capabilities or the quality of the output. Instead, it boils down to a lack of understanding due to the scarcity of good information, compounded by corporate processes and attitudes—many are simply risk-averse, Markley believes.
From Markley’s perspective, while most companies have avoided taking the leap into metal AM, he acknowledges that some not only use metal AM already, but also fully leverage it. He cites Caterpillar and GE as examples, noting that, “We are doing advanced projects, and while we can’t share details, these projects fundamentally will change manufacturing and design as it is currently known.”
 |
Topology-optimized aerospace brackets designed with Altair’s solidThinking Inspire. |
To Markley, the successes realized by those companies leveraging metal-AM technology can be attributed to a strong drive to benefit from the technology in ways not previously possible. He sees in these companies a willingness to invest in learning and research; an openness to breaking from tradition; and an acceptance of the reality that with change comes some amount of risk. He also notes that having the requisite human and financial resources helps to move things forward.
With the minority far exceeding the majority, “We are not at critical mass yet...even in aerospace,” says Markley. With critical mass will come a sense that metal AM is an alternative that must be strongly considered, rather than an option that may be ignored. “Those who are thinking about it but do nothing,” he stresses, “don’t realize that they are already years, if not decades, behind.”
Risk Aversion Cultivated by Culture
Markley observes that one of the biggest reasons for pushback stems from fear of, and retribution for, failure. In an environment where failure puts individuals and department heads in jeopardy, either real or perceived, manufacturers often have little leeway to try something new or to try to achieve different goals. Risk must be managed, but it cannot be allowed to stymie ingenuity.
In place of this risk aversion, Markley hopes that the attitude among manufacturers shifts to consider unsuccessful attempts at metal AM as learning experiences. “You have to start somewhere,” he says. “You can’t sit on the sidelines waiting for the answers to come to you. Dip a toe in the water and discover the answers for yourself.”
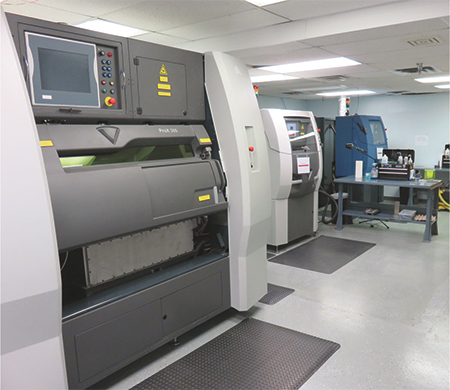 |
3rd Dimension Industrial 3D Printing’s lab, home to 3D Systems’ ProX metal printers. |
To be clear, metal AM is not inherently risky. Rather, it is the scarcity of clear, concise and factual information and data that creates unknowns. In turn, it is the unknowns that create uncertainty, which fuels the sense of risk.
When it comes to production applications, Markley does not think that this is a metal-AM issue. Instead, it is a systemic problem created by the desire to drive out all risk. Describing his previous work experience at a large automotive company, Markley says, “If we were manufacturing something as simple as a spring, there could be a 20-page Excel spreadsheet dictating requirements. The processes these larger companies use make it difficult to take design risk, regardless of the potential benefits.”
A Treacherous Information Gap
“We see a lot a lot of misinformation out there,” Markley says, describing the knowledge gap plaguing the adoption of metal AM. “We often come across confused consumers and must dispel a lot of untruths.” Untruths, combined with uncertainties related to metal AM, fuel risk adversity.
As an example of existing information challenges, Markley points to design for metal AM and dispels the myth that complexity is free. This, he says, can misguide potential users, or overwhelm them with the promise of endless possibilities. In addition, he cites a widespread lack of appreciation for the need to design for metal, leading to unsuitable designs or those that fail to leverage the advantages of metal AM.
“I use this example often,” Markley explains. “If you design a part to be milled and then decide instead to turn it on a lathe, it won’t work. Same with additive—the client needs to understand the capabilities of the AM processes and design around them.”
Finally, Markley laments the lack of hard data to guide design decisions. “If we don't have design allowables, you can't design around them,” he says. “We tell everyone that you can’t rely on a material spec sheet from an OEM.” Too many AM-process variables, he explains, controlled by operators, can influence a part’s mechanical properties, including build parameters and the procedures used for powder handling and heattreatment.
Markley, knowing that this information challenge creates an undesirable hurdle, also believes that manufacturers can overcome this hurdle by seeking guidance early in the process; being open to a trial-and-error approach; and accepting that 100-percent testing may be required for production applications.
Complexity May Come with a Cost
While metal AM excels at reproducing designs often not possible nor practical with subtractive methods, it does come with design rules that dictate time, cost and quality. Complexity is not entirely free, and Markley cites two examples: supported features and block-level callouts.
About 3rd Dimension Industrial 3D Printing 
| Bob Markley, owner of 3rd Dimension Industrial 3D Printing “If
you design a part to be milled and then decide instead to turn it on a
lathe, it won’t work. Same with additive—the client needs to understand
the capabilities of the AM processes and design around them.” |
| 3rd Dimension Industrial 3D Printing was founded in 2013 with the goal of mastering the craft of additive manufacturing and producing only the highest-quality parts. The company offers a range of services including metal and plastic 3D printing, machining, consulting and design for additive guidance. Its skilled engineering team’s experience centers around racing, so it understands that time and precision are of the utmost importance to its customers. This expertise enables the company to rapidly move parts from prototyping to manufacturing.
|
Laser-melting AM processes require support structures, unlike the plastic-AM processes that use powder beds. “If a metal part hasn’t been designed for the process, support structures can add 60 percent or more to the part volume,” says Markley. This added volume increases build time needed and since the supports must be cut away, it increases the time neededfor secondary operations. Of course, time is money, so unnecessary supports add cost.
“Another thing we also see are block-level surface-finish callouts,” Markley continues. “Often, these callouts have been there forever and no longer are questioned. If we have to hit 63 Ra over an entire surface, for example, that will take significantly more post-processing than if we only had to achieve that where the need really lies. It adds unnecessary time and cost and, depending on the geometry, may not be possible.”
When it comes to designing for metal AM, Markley states, “I would advise getting service bureaus, such as ours, involved at the earliest point possible. Most of us are willing to do a quick design review, at a minimum. If you have a design team working on a project for hundreds of hours and then throw it over the wall and it doesn't work, you’ll become soured on additive. We want to help you get it right, and leverage what AM can do.”
Myth: Standalone and a Replacement
Another misperception cited by Markley: metal AM is a standalone process or a replacement for machining. Instead, metal-AM complements the machining processes. “We see a lot of very tight-tolerance work that needs secondary machining,” he says. “So we will print near-net parts, and turn to precision machining to achieve the tolerances and deliver desired surface finishes.”
To take control of secondary machining operations and to minimize costs, 3rd Dimension Industrial 3D Printing has brought machining inhouse. This also lets the company accept projects that it would otherwise turn away.
“Machining and metal AM are not mutually exclusive,” says Markley. “If we can complete a part on a mill or a lathe, we won’t try to force it to be an additive project, and we quote a lot of projects that simply shouldn't be done with additive. Having both competencies inhouse allows us to best-meet the clients’ needs rather than force them into a process.
“We started as additive-only,” he adds, “but in the last year our growth has been on the traditional subtractive side.”
Commentary
This discussion provides facts and commentary that shop managers can use to support their decision to continue to develop their expertise in machining, molding and casting. But, that takeaway is shortsighted and not Bob Markley’s intention. Instead, I recommend that open-minded shop executives consider his perspective as they engage with those in the metal-AM industry.
My takeaway: Candidates for metal AM should enter into the conversation with eyes wide open, so that they’ll be best-prepared to acquire the needed knowledge and experience to make metal AM work for their company. Having proper expectations sets the stage for education, understanding and trial-and-error experiences. Those that assume that metal AM is a magic wand or “easy button” are much more likely to turn away in frustration or disappointment at the first sign of a challenge.
Many AM successes are tied to necessity rather than innovation. If you wait until the need arises to learn all that is possible, and all that must be considered, you put yourself in position of having to hit a homerun in your first at-bat in your first game.
Do not let fear of failure and risk aversion paralyze efforts to implement change. Combat them with knowledge and experience. Get off of the sidelines and prepare for a future in which the impact of metal-AM technology continues to grow. 3DMP
Have a difference of opinion or insights that you would like to share? Contact Editorial Director Brad Kuvin (bkuvin@3dmpmag.com), to schedule an interview.
See also: 3D Systems
Technologies: