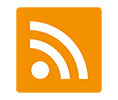
What are Stamping Presses?
Stamping Presses are machines that provide force to tooling in order to form material into flat, shallow or deeper-drawn parts via progressive, transfer, line or other types of dies. Ideal for volume production, stamping presses are available in various orientations and force-production methods depending upon the applications. Types of presses, indicating these force-production methods, include mechanical, hydraulic and servo, with all exhibiting unique features and capabilities related to speed, acceleration/deceleration and dwell capability.
What is Servomechanical?
Servomechanical presses use servo motors to help direct ram movement, enabling fine control of ram position and speed throughout the press stroke.