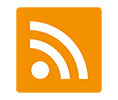
What is Software?
Software for metal forming and fabricating processes includes programs to design and build tooling and parts; simulate processes; and track processes, product development and production, and productivity of equipment and personnel. It also can tie all of these into systems for effective control of organization-wide manufacturing, inventory and business functions.
What is Die Design & Simulation?
Die design and simulation software help to effectively design parts and tooling and identify and remedy issues prior to actuall tool build, thus saving users time and money relatred to trail-and-error design and build approaches.