
Material Properties for Virtual Metalforming
May 1, 2010Comments
Virtual forming (computerized die tryout, computerized metalforming, etc.) is revolutionizing the sheetmetal industry. The advantages these programs offer are numerous, including time and cost reductions for die design/tryout and improved stamping quality.
Many years ago, a popular slogan was applied to manufacturing products, cuisine and personal lives: GIGO or Garbage In Garbage Out. The implications were well understood and most people reacted accordingly. Then computers became popular and the meaning of GIGO changed to Garbage In Gospel Out. Since computers cannot lie, the output was taken to be the truth. Unfortunately, virtual forming has become a major victim of GIGO. This month’s column explores some GIGO problems associated with material-property inputs.
Drop-down menus are a common method for telling the computer which metal and grade should be used for the analysis. Click on AKDQ (aluminum-killed draw-quality) or the more current FS (forming steel) or DS (drawing steel) and a set of typical properties are sent to the program. In contrast, many dies actually create stampings from alloys with a formability property range from -3σ to +3σ of the typical value. Forcing the computer to use only the typical property rarely provides a meaningful analysis.
For example, one key material parameter needed for virtual forming is the work-hardening exponent or n-value. For AKDQ steel, this n-value can range from 0.18 to 0.23, yet a change of 0.01 can shift a stamping between make and break. For an accurate forming analysis, the n-value of the intended production material must be entered—not a typical value. An important advantage of virtual forming for die tryout is running the analysis with four different n-values. These values are the -3σ, typical, +3σ, and production to gain an insight of how n-value influences the final stamping. Changing the n-value requires only a simple keyboard entry. With hard tooling, one must find or order four coils of material with the desired properties and run statistical evaluations of all four coils.
![]() |
Graph of instantaneous values of n for three 50-ksi (350-MPA) higher strength steels. Courtesy of WorldAutoSteel AHSS Application Guidelines |
Selecting one high-strength low-alloy (HSLA) steel from the drop-down menu also enters a single n-value. This assumes that the n-value is relatively constant over the full range of deformation. The n-value is calculated between the strain values of 10 percent and uniform elongation/maximum load. (This steel is shown as the dashed line in the graph with an approximate n-value of 0.15 within the indicated measurement strain range.)
In contrast, two relatively new advanced high strength steels (AHSS) have n-values that change with strain. One now must compute instantaneous values of n that show the n-value for different amounts of strain. The first AHSS is dual phase (DP) steel (solid line in the graph). Note the early increase in n-value to a value of 0.2. This higher n-value at low strains is effective in resisting the formation of localized strain gradients. However, this increased n-value is exhausted before reaching 10 percent strain. This means traditional tensile samples of the HSLA and DP steels will have approximately the same n-values and the computer will not recognize the stretchability improvement of the DP steel. The results of a computerized die tryout will suffer a GIGO error. However, the solution is quite simple. The computer analysis program must be capable of accepting the true stress-true strain curve, which captures any change in n-value over the entire range of deformation
The forming limit curve or maximum allowable stretch (strain) also depends on the n-value. Here an n-value at a large deformation or plateau strain is required. The two curves shown in the graph have the same high n-value. This means the forming limit curves for these HSLA and DP steel coils will be identical. This was confirmed by experimental determination of the actual forming limit curves.
The second AHSS is the transformation induced plasticity (TRIP) steel, beginning to gain applications in the automotive industry. If the initial higher n-value of DP steel is so beneficial, why not create steel that keeps regenerating the higher n-value over a wide range of deformation? The TRIP steel (dotted line in the graph) is designed to accomplish this major improvement. Now the n-value not only changes with strain, but has an increased value as traditionally measured between 10 percent strain and uniform elongation. Even here, the measured value is an average n-value between the two measurement points and still provides no information about the changing n-values outside that range. Again, the true stress-true strain curve would capture the variable nature of the n-value for use by the computational program.
Unfortunately, the TRIP steel has another problem. The properties of the as-received TRIP steel are not the properties experienced by the stamping during the forming operation. The increase in the instantaneous n-value is a function not only of initial steel composition and processing, but also the strain path, strain history, forming speed, temperature and other production factors. Therefore, the instantaneous n-value and the forming limit diagram depend on the actual deformation, which changes not only from part design to part design but also with location within the part. Thus, capturing the actual property levels active during deformation is a problem still unsolved, which makes output of TRIP steel analyses questionable.
Most aluminum alloys have a comparable problem. Their n-values are not constant but decrease with increased deformation. Therefore, n-value data often are presented as 0.35 (0.22), where the first value is the initial n-value and the second number in parentheses is the average value over a wide range of strain. Other metal alloys have their own set of property idiosyncrasies. One must understand the input to the computer program to assess the validity of the output.
The correct properties for virtual forming and other analyses depend on the accuracy desired for the final stamping. Springback prediction requires much more accuracy of input properties than does designing a stamping to hold water. The need for accurate properties extends to troubleshooting and press-shop areas other than virtual forming. Therefore, discussion of accurate properties continues next month. Topics include blanked-edge damage, local elongation, strain-rate hardening and friction. MF
Technologies: Quality Control
Comments
Must be logged in to post a comment. Sign in or Create an Account
There are no comments posted.Brinell, Rockwell and Vickers Hardness Testing: Use and Misu...
Daniel Schaeffler Friday, April 1, 2022

Troubleshooting Sheet Metal Forming Problems, Part 2: The St...
Daniel Schaeffler Friday, February 26, 2021
Cobot Setup Offers Pick-and-Place for Material and Product S...
Wednesday, April 29, 2020
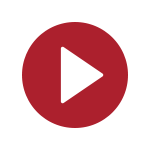