Is Your Die-Change Process All That?
March 1, 2018 Or is it time for some revisions?
If your pressroom is cluttered, poorly laid out, or lacks a good die-transport system, then achieving quick die changes (QDC) is going to be, at the very least, difficult. MetalForming spoke with Lee Ellard, national sales manager for Stamtec, Inc., Manchester, TN, to learn the most common pressroom mistakes and what to do about them in order to achieve QDC.
Staging and Layout
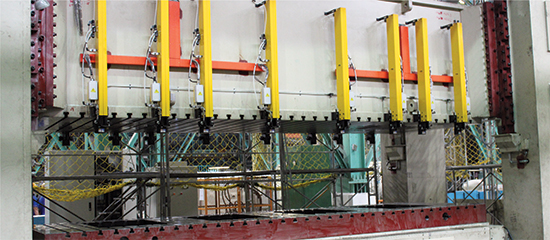
|
Shown are eight (yellow) traveling clamps. Each clamp is attached to a drive chain for extending the die clamp into and out of the die area, making it safer and easier for a die-setter to set the clamp in its clamping location. |
“The most common inefficiency would be poor staging and layout,” says Ellard. “All pressrooms must have a staging area for dies, tools and coils for when it’s time to make a die change.” Ellard recommends locating staging areas close to the presses, and prestaging items in those areas well in advance of the last hit of the current die or coil. While it may not be possible to rearrange your shop extensively, Ellard says at the very least “make it as clean and uncluttered as possible so that moving around during a job is safe and efficient. That includes making sure that parts, scrap bins, unloaders, etc., are out of the way. Do this immediately after the last hit on the current die so as not to impede the rest of the process. “You don’t want to have a room full of stuff that you’re tripping over.”
Storage/Retrieval/Transport
When not in a press or the staging area, Ellard recommends storing dies and coils near the press area in a way that provides easy retrieval of the dies by a transport vehicle. As for what is a good transport vehicle, Ellard says that depends on the operation. “It can be as simple as having a dedicated and always-available forklift,” he explains. “Many plants have forklifts for multiple purposes. The problem with these scenarios is that the forklift may be in use moving a scrap bin or something else when needed for die changing. An even better solution is to spend the $50,000 on a dedicated die cart that rolls right up to the press with the die on it. This requires the cart, as well as die rollers and die lifters. Whether a die cart or forklift, the key is just to have something readily and easily available as needed.”