Using today’s valves and PLCs, cycle times can be improved with simpler and easier-to-troubleshoot circuits. Variable-displacement piston pumps allow flow and pressure to be controlled directly at the pump, simplifying the hydraulic circuit and optimizing horsepower to improve the circuit’s efficiency. And, as efficiency improves the press will experience less wear to the oil and hydraulic components, reducing the maintenance burden.
To reduce cycle times and improve part quality, a press rebuild can include installing servo-quality proportional valves and high-performance PLCs to offer faster response times and improved positional accuracies. Advanced control packages can take existing equipment and dramatically broaden their capabilities, opening new opportunities for manufacturers.
Using touchscreen press controls, all press-setup points—including those for top stop, slowdown and reversal—easily can be changed. This eliminates the need for time-consuming manual adjustments, and such a closed-loop system adjusts itself to match process parameters. A control’s safeguards even can reject incorrect settings, preventing costly accidents. In addition, ram position is tracked by a linear transducer, which rarely needs calibrating. The control can be integrated with a precision digital control system, which enables actual position accuracies of ±0.001 in. and reversal at ±1 percent of specified tonnage.
Repeatability has improved dramatically thanks to the use of new PLCs and valves. Metal formers can store multiple programs or recipes in the controllers, which can be accessed as needed—a big advantage compared to manually entering program parameters each time a new job runs. This automatic process can eliminate the need for a setup operator, requiring only the press operator to call up the program already loaded with values that have been checked by performing qualifying runoffs. Depending on PLC memory capacity, hundreds of recipes can be stored, enabling the press operator to change programs in just seconds and ensuring that parts are produced precisely and repeatedly every time they run. Modern PLCs also are flexible enough to allow the use of multiple programming languages to best suit the current requirement.
Barcodes in the Pressroom
Quality control further improves with the use of barcode readers. Metal formers use barcode readers to scan the tool and the work order to automatically upload new parameters for that part. Scans also can validate the press and die against the work order to ensure the use of the proper press for the job. Process data such as position, temperature and time can be logged for every part produced, and an employee’s badge can be scanned to check for permission to operate the press.
New PLCs enable process automation by controlling multiple presses within a line, or by integrating a press with auxiliary equipment. This automation provides consistent control over all press operations. Typical applications include adding roll feeders for advancing sheet metal, rotary-index tables or robotic material handling built into a press line.
Motors and VFDs
Motors are much more efficient today, offering a reduced rotational mass and higher-quality copper with improved winding technology. Pumps also are more efficient, as improved seals and stronger hoses and couplings have virtually eliminated leaks and greatly minimized maintenance. Even hydraulic fluids exhibit increased effectiveness due to new additives, promoting improved pump performance. Also, state-of-the-art pumps and motors operate more quietly than do their aging counterparts, and they use off-the-shelf replacement parts.
Another development: the use of soft motor starters or variable-frequency drives (VFDs). These devices allow the motor to ramp up to full speed, decreasing the inrush current. A hydraulic press with a VFD will start the motor when the press is ready to perform work, and then shut the motor off when platen movement is not required, including during press idle times. This technology can run the motor at slower speeds when the press sits idle, to allow for accumulators to be charged and the oil to be cooled or filtered.
Finally, new options for increased press safety might include adding light-curtain circuits, presence-sensing devices, gates and barriers. Solid-state relays for anti-tiedowns on press buttons is another consideration.
Pressing for Change
Metal formers ready for a hydraulic-press upgrade should evaluate their goals in relationship to their costs. Among the considerations to evaluate in determining whether a retrofit or entire rebuild will prove most beneficial:
Retrofits/Upgrades
- Upgrade to the current ANSI B11.2-2013 standards for safety.
- Build in speed control for handling hard-to-form materials and to increase cycle rates.
- Add closed-loop pressure and distance control.
- Improve accuracy and repeatability.
- Integrate automation components (robotics, feeders, etc).
- Add the ease-of-use and accuracy of touchscreen controls with recipe storage.
Rebuilds
Rebuild services replace hydraulic, mechanical and electrical components. If some of the following components are needed, it may be time for a rebuild.
- Replace old, complex piping/valve systems with a single manifold system.
- Replace or rebuild pumps and motors.
- Replace leaky hydraulic pipe-thread technology with oil ring seals (ORS and SAE).
- Rewire electrical systems.
- Rebuild cylinders.
- Replace worn-out platen guides/ slides.
- Strip down and repaint surfaces.
- Replace ram gland rings and seals. MF
Article provided by Greenerd Press & Machine Co. Inc., Nashua, NH; www.greenerd.com
View Glossary of Metalforming Terms
See also: Greenerd Press & Machine Co.
Technologies: Stamping Presses
Comments
Must be logged in to post a comment. Sign in or Create an Account
There are no comments posted.H-Frame Hydraulic Presses Feature Table-Raising Capability
Monday, December 18, 2023
Simwon America Corp. Ramps Up Hot Stamping in Austin, TX
Monday, November 13, 2023
During FABTECH 2023, MetalForming Magazine Catches ...
Monday, October 23, 2023
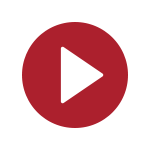