Localizing Via 2D Vision
When using mobile manipulators, a docking station’s position and orientation must be verified every time using some form of localization to ensure repeatable robot motion. When a mobile robot docks at a station, repeatability can vary by several centimeters. And, any small dip or bump on a floor—in fact, essentially no floor is perfectly level—can change significantly the position of the cobot’s end-of-arm-tool.
2D Vision can solve these issues within seconds, accomplished by adding a vision target (a camera-calibration grid) to each station and teaching all of the target positions. When the mobile manipulator arrives at a station, a 2D camera takes several images of the target and calculates its position and orientation relative to the robot. This establishes the target’s position, with all subsequent robot motion at the station remaining just as accurate as when first taught.
Various Means of Communicating With Cell
A CNC machine can communicate with a mobile manipulator in many ways. The demonstration described above attempted to mimic a human operator as much as possible, with vision employed for communication between the CNC and the rest of the cell.
As demonstrated, when the machine completes a cycle, it opens the door and uses the stack light to indicate that service is required. The mobile manipulator arrives at the machine and checks the light to confirm the service requirement. After completing tasks at the machine, the robot presses the cycle start button and checks the stack light a final time to verify that the machine is running before the manipulator leaves the station.
Another application might employ networked communication, potentially yielding a more efficient solution. In this case, the CNC machine can signal when a cycle is almost completed, with a mobile manipulator dispatched early so that it arrives just as the machine cycle completes.
Designed for Safety and Simple Navigation
The demonstrated mobile manipulator possesses numerous safety-rated features. The cobot itself is power- and force-limited, and the manipulator also employs laser scanners mounted on two corners, offering 360-deg. coverage. For low-risk tasks, the cobot provides safe operation without the need for safety scanners. To utilize higher speeds or perform riskier tasks, safety scanners can be used to prevent the arm from moving in proximity of human operators. The key here is flexibility—power- and force-limiting features of the cobot can be augmented by the area scanners to achieve a safe system in a way that makes sense for each unique application.
As for navigation, the Otto 100 AMR offers several advantages in transporting a mobile cobot/manipulator, including:
- Flexibility to respond to unexpected obstacles by automatically rerouting around obstructions
- Large wheels that allow the AMR to travel over rough or bumpy factory floors
- Straightforward route-map setup as only a single manual drive around the site sets the AMR’s map, with the map then populated with stations, chargers and other points of interest.
Otto’s robust Fleet Manager software enables everything from programming simple waypoints to defining complex factories integrated into building infrastructure. Changing machine location or workflow is as simple as adjusting destinations on the map—the AMR handles everything in between.
Ways to Maximize ROI
Before investing in a mobile-manipulator system, it’s important to work with a reliable automation supplier that will conduct a thorough review of an operation to ensure efficient use of the automation. In our described demonstration, a mobile cobot performs different tasks at each station. An alternative and possibly more cost-effective approach might involve using fixed robots at each station to perform process tasks and using the mobile manipulator only to move parts between stations and fixtures. This keeps the mobile manipulator moving as much as possible, allowing it to service more stations versus using it to perform tasks at each station.
Mobile machine tending pays off in consistency and flexibility. The mobile manipulator performs machine loading with robotic precision, and part throughput doesn’t change from shift to shift. Robots don’t attend meetings and they don’t mind working three shifts. Thinking long-term, a mobile solution also proves most flexible. A rail-mounted robot initially may be faster, but changes are expensive and require significant rework. A mobile solution easily accommodates layout changes, expansions and even complete workflow overhauls.
Imagine implementing a system such as the one highlighted in this article to tend CNC machines; then, at some point, operations require the addition of an inspection station. A mobile solution enables quick implementation—programming the robot at the new inspection station and simply adding a destination to the map. Alternatively, a strictly manual operation undergoing process changes might require additional manpower and scheduling—with the labor shortage, adding manpower is no easy task. And, had a linear rail been installed previously, an expansion may not even be possible—where to find the additional floorspace?
Another way to look at ROI: employee satisfaction and retention. By automating the strenuous and repetitive tasks of loading and unloading CNC machines, manufacturers can reduce the risk of injuries to employees, making their jobs much safer. When employees can focus on higher-value tasks, they become more satisfied with their workplace, thereby decreasing turnover and limiting the need to hire manual laborers.
Of course, when it comes to machine tending, checks and balances must be reviewed before implementing any new equipment or processes. Thinking long-term, a mobile manipulator proves a very flexible solution that can help manufacturers meet customer deadlines, maximize productivity and help overcome labor challenges. MF
View Glossary of Metalforming Terms
See also: FANUC America, Inc.
Technologies: Pressroom Automation
Comments
Must be logged in to post a comment. Sign in or Create an Account
There are no comments posted.Rockwell Issues State of Smart Manufacturing Report: Automot...
June 13, 2023
MetalForming LIVE On the Shop Floor 2024: Part 1 Re...
Wednesday, April 24, 2024
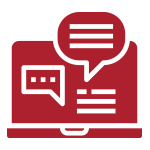