3DMP—Please explain how digitization and the use of sensors and “smart manufacturing” help support automation in the metal-AM industry.
Kara—This is an interesting and exciting topic—much has happened in this area. We see a significant increase in the development of automation driven by the escalation in the use of sensors. AM-machine builders are adopting this technology very quickly. It’s driven primarily by two factors—the need to improve product quality (and track and trace build results), and the desire to increase machine utilization.
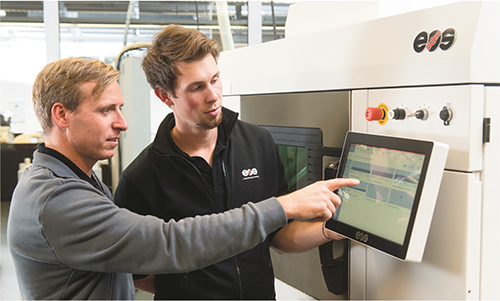 |
“The key areas of training that we see as the focus in 2017 and beyond,” says Kara, “are understanding design complexity, part consolidation and lighweighting; how to design for post-processing; and optimization of process parameters.” |
For example, with the aim of minimizing machine downtime, AM-machine controls now can send SMS text messages to operators. Such a message might, for example, alert the operator that a build is nearly complete, and that he should prepare to open the process chamber, remove the part and prepare the machine for the next build. The goal is to minimize changeover time.
This technology will become much more prevalent in the coming months, as platform solutions become available. This will result in the simultaneous management of software applications, sensors, data analytics and process flow.
3DMP—How is the industry, and specifically EOS, preparing to educate engineers and others on metal-AM technology, in light of all of this ongoing innovation and rapid increase in use?
Kara—Companies using metal AM now are realizing that merely hiring recent engineering graduates, who have studied AM in college, is not sufficient. They must train their current, experienced engineers in metal-AM technology, from design for AM to post-processing techniques. And then, these trained engineers must be capable of going back to their companies and imparting what they have learned to the rest of their team.
The key areas of training that we see as the focus in 2017 and beyond are understanding design complexity, part consolidation and lighweighting; how to design for post-processing; and optimization of process parameters. One of the goals also must be to move engineers away from the machines and let machine operators take over day-to-day tasks of machine setup and machine tending. This will happen as we educate engineers on process development and evaluation—steering them away from using the machines for physical trial-and-error tasks and instead performing what I call an “intellectual trial and error process.”
At EOS, we have for the last two years developed a training partnership with two European universities—the University of Wolverhampton, in West Midlands, UK, and Germany’s SRH Hochschule Berlin—to help us develop a comprehensive program combining hands-on training and classroom instruction. We’ve already begun to use the program to train our own employees, and will offer the program to customers later this year. Metal-AM training at Wolverhampton addresses design, process optimization and material qualification; training at SRH focuses on driving innovation throughout the company culture.
So, with this training engineers not only learn 3D metal printing from start to finish, but they also learn how to move this innovative technology into their companies. They come away with an understanding of how to communicate with engineers at their companies and preach the benefits of AM. They learn how to calculate ROI, and we provide case studies on how to run innovative workshops within their companies, and how to pull together interdisciplinary teams—people from quality, production, supply chain, R&D, etc.—and drive innovation. 3DMP
See also: EOS of North America, Inc.
Technologies: