Servo-Based Tapping Units
Just as servo technology has found its way into presses, feeds and transfer systems, it also has found its way into in-die tapping units. Servo technology adds a level of control not available with mechanical units. The question, though, is whether the extra level of control with servo-based units warrants the higher cost and technical expertise required.
Servo tapping units offer several advantages over mechanical. The use of servo motors in place of mechanical cam drivers enables the use of servo tapping units with any press stroke length, and in a variety of presses, provided that they include an encoder to feed information back to the control panel.
Servo tapping units also allow for a larger tapping window when compared to mechanical units. With mechanical units, the tap indexes forward as the press ram moves toward the bottom of the stroke, and reverses the tap as the ram moves from bottom dead center (BDC) stroke back up to top dead center (TDC). Servo units, on the other hand, allow for tapping forward at any time in the stroke, even as the press reverses back to TDC. This allows for a larger tapping window, which translates into higher production speeds in strokes/min., since the tap can retract from the strip at a faster rate than the controlled rpm while tapping occurs. With a mechanical tapping unit, the tap does not retract and allow the strip to feed until a specified number of tapping turns have been completed; with a servo tapping unit, strip feed occurs after a set amount of time, regardless of the number of tap turns.
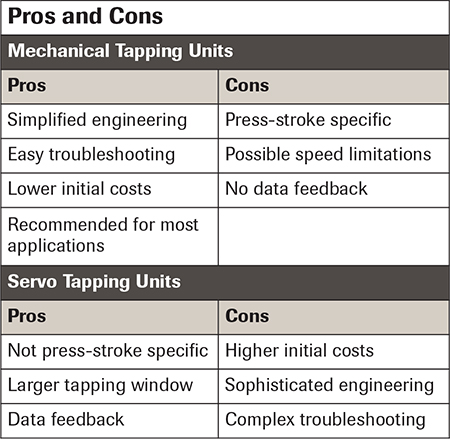
Finally, servo control allows the capture of processing data, which can support preventive-maintenance and product-quality programs. For example, the stamper can prescribe torque parameters and direct the press to shut down should torque vary outside those parameters. If torque climbs above the recommended setting, the tap likely has dulled and needs replacing. Conversely, too little torque could indicate a broken tap.
The decision to use mechanical or servo tapping units is specific to each application. In most applications, either option would be a good choice. Ultimately, a company needs to access its requirements, assess its engineering/support capabilities and justify its investment when choosing the tapping method best-suited to its plant and project requirements. MF
View Glossary of Metalforming Terms
See also: Hutchison Tool Sales Co.
Technologies: In-Die Operations
Comments
Must be logged in to post a comment. Sign in or Create an Account
There are no comments posted.Servo-Driven In-Die-Tapping Technology
Wednesday, August 4, 2021
In-Die Tapping
Wednesday, October 2, 2019

Tools for Tapping
Wednesday, October 2, 2019