“The CMMs allow our operators to quickly verify their own work,” says Pinho. “Each inspector is trained to operate the CMM software programming that is installed on all of our CMMs.”
In addition, laser-programming software allows personnel to download CAD data and manipulate it into a 2D CAD model used to create laser-cut-developed blanks for the company’s stamping department.
“This gives us the capability to turn CAD-data concepts into a physical part in days instead of weeks,” Pinho explains. “And with full CAD capability in the measuring software, our laser-cutting machines and CMMs are an integral part of the manufacturing process, permitting generation of inspection and laser-cutting programs prior to manufacturing. With this setup, operators perform complete hands-free inspection from the PC, using the CMM software to determine the feature type under measurement and allow for rapid part inspection without the traditional tedious need to instruct the software as to what to inspect next.”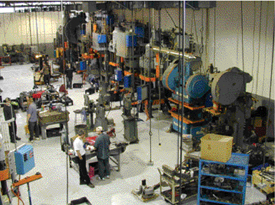 |
More than 40 mechanical and hydraulic presses are used for prototype, small and medium-sized production runs at Duggan. |
From Prototypes to ‘Prodotypes’
In some cases, prototype production may evolve into short-run work due to delays in stamping tools, broken tooling, a part design change or other reasons. The ability to perform short-run production is a natural outgrowth for a prototyper such as Duggan, “Sometimes,” Pinho says, “we suddenly have to change hats and become a short-run stamping supplier. Our prototypes become production-types or ‘prodotypes.’ This capability can be as valuable to the customer as our prototyping know-how.”
So Duggan employs more than 40 mechanical and hydraulic presses for low-volume production and production-intent projects.
Transferring from prototype to ‘prodotype’ can occur in a hurry, as illustrated by this example. Duggan, the prototype supplier of stamped automotive-seat side-member assemblies, was called on to produce 20,000 right- and left-hand seat side assemblies immediately. Why? The production fixturing for an operation that welded in place a series of studs and grommets was not completed in time for product launch. Duggan was tasked with producing the stampings as well as assembling the studs and grommets. Using the prototype laser-cutting process and available press tooling, Duggan, in less than two weeks, set up a production schedule for the stampings, fabricated a series of fixture plates for the right- and left-hand parts, and organized and programmed one of three flexible robotic welding cells to weld the three stud/grommet components into each of the stampings. The first order, for 300 pairs of parts, was placed on a Friday and delivered on Sunday. The cell operated 24 hr./day for eight days to complete the required quantity.
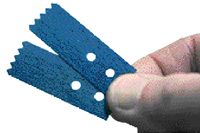 |
Providing Duggan another opportunity to turn prototype work into a production run, a customer needed these airbag brackets delivered within 4 days due to a late design change on the air-bag system and the inability for new tooling to be built in time for initial production. Key to helping the customer: Duggan’s ability to have prototype tooling ready and proved robust enough to hold up through the 15,000-part run and meet an SPC requirement that dictated checking every 300th part for tolerance variation. The order was placed on a Wednesday, the parts fabricated on Friday and delivered the following Monday.
|
Another customer, due to production dies not being ready in time for product launch, needed 56,000 parts—child-seat-belt anchor tethers—within five weeks. Duggan got the call for two reasons: It had supplied the prototype; and it had been approved as a quality supplier of this safety-related part.
Within 10 days the press tooling was refined, the stampings and wire forms scheduled for production, and one robotic-welding cell programmed and set up with multiple-part fixturing to weld the wire forms to the brackets. All 56,000 parts were delivered within the five-week schedule.
A safety-related component, an airbag bracket made of spring steel and encompassing specific SPC requirements, yet again offered Duggan the opportunity to turn prototype work into a production run. The customer needed 15,000 of the brackets delivered within four days due to a late design change on the air-bag system and the inability for new tooling to be built in time for the initial production run. The key to helping this customer: Duggan’s ability to have prototype tooling ready and proved robust enough to hold up through a 15,000-part run and meet an SPC requirement that dictated checking every 300th part for tolerance variation. The order was placed on a Wednesday, the parts fabricated on Friday and delivered the following Monday.
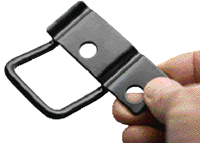 |
Showing its ability to convert from prototype work to production, Duggan fabricated, stamped and robotically welded 56,000 of these child seatbelt-anchor tethers to meet a five-week emergency production schedule. Duggan got the call because it had supplied the prototypes and was approved as a quality supplier of this safety-related part. |
“There was a time that you could make a living just producing stamping prototypes, but that’s not the case today,” Pinho says. “Those companies are disappearing fast. It’s the value-added services that now prove your worth. You not only have to be good at it, but you have to be committed to it, and you have to be able to do it fast.
“To be fast,” he continues, “you have to revolutionize the cultural aspect of your business, and we have done that. Our philosophy, driving all of the manufacturing strategy that we have implemented since we started Duggan Manufacturing in 2000, has been built on lean operations, not just on the product and process, but on the people.” MF
Information for this article supplied by Duggan Manufacturing, Shelby Township, MI; tel: 586/254-7400; www.dugganmfg.com.
Industry-Related Terms: CAD,
Case,
Checks,
CNC,
Compress,
Download,
Fixture,
Model,
Prototype,
Run,
ToleranceView Glossary of Metalforming Terms
See also: MC Machinery Systems
Technologies: Fabrication