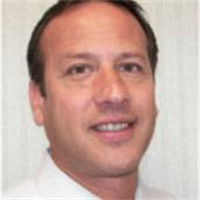
Best Tool Steel for High-Speed Stamping?
April 29, 2024Comments
Q: What’s the best tool steel for my high-speed stamping applications?
This is a very important question. The right tool steel can double—or halve—the number of hits you get from tooling before it requires service. Obviously, this has a serious impact on the tooling bottom line. You need a thorough understanding of the tool steel’s mechanical properties and apply them as needed to suit your specific application. How will the steel flex when mechanical forces are applied? Proper heat treatment also is crucial to success.
Hardness and toughness are the two most critical properties I look for when choosing a tool steel for my cutting and coining processes.
Hardness. Hardness is the ability of a tool steel to withstand indentation after proper heat treatment. If you are stamping relatively light-gauge material (less than 0.015 in. thick), opt for the hardest possible cutting tooling … most of the time that is carbide. That is, of course, if the cutting geometry is not so fine that the geometry lacks the strength to hold up. If that is the case, back down on the hardness and look for increased toughness. I cannot stress enough that you must pay close attention to proper heat treatment, annealing and tempering. You might even double- or triple-temper for maximum toughness.
Toughness. This is the ability of the material to absorb energy and shock without degradation. One job I worked on required a forming arbor with a nonsymmetrical load applied. We tried several materials, based on hardness, to no success. Then we tried materials that were not as hard but were tougher—Crucible 3V. We sacrificed tool life but achieved results that allowed us to run consistently. A high-toughness material, such as the CPM grade of tool steel, will provide maximum break resistance. Proper heat treatment, stress relieving and triple tempering were required. In addition, we added cryogenic freezing between the last two tempers. The cryogenic freezing process, while underutilized, makes all of the difference in achieving success.